By Tom Pinto
Industrial need
Surfi-Sculpt is a novel power beam materials processing technology implemented using either a laser beam or an electron beam (EB). Surfi-Sculpt and electron beam texturing (EBT) are neither additive nor subtractive processes. Instead, this process locally melts and moves the molten parent material of the workpiece to form a modified surface once it has cooled. The potential benefit of Surfi-Sculpt is its ability to rapidly manufacture a range of features with the same size, shape and distribution all of which can be varied to produce a surface tailored for a specific application.
Key Findings
- EB Surfi-Sculpt has been studied using slow motion analysis allowing greater understanding of the process highlighting that there are four distinct phases in the formation of a Surfi-Sculpt feature.
- Slow motion analysis has shown that the movement of molten material initially caused by the interaction of the EB is much more controlled than for laser Surfi-Sculpt.
- A Surfi-Sculpt catalogue has enhanced TWI’s knowledge management process surrounding Surfi-Sculpt and EBT, ensuring more effective knowledge sharing, storage and refinement.
- Heat exchanger testing has shown that the use of Surfi-Sculpt may approximately double the heat transfer coefficient at similar pressure drop for a 1000W heat load, compared with a conventional design and was able to maintain the operating temperature of a power resistor 30 degrees lower compared with a conventional design.
- For composite to metal joining (Comeld™) use of a lower fibre density or more resin rich composite system may improve the lay up to ensure no voids are left. Shorter and/or blunter features may also be beneficial in this respect.
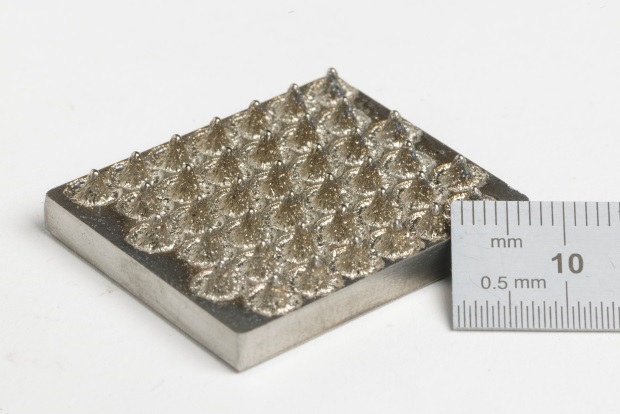
Cone shaped features on 5mm Ti-6Al-4V substrate
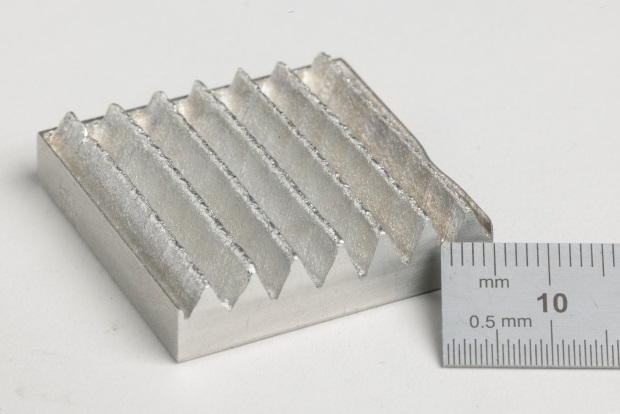
Ridge features on 6mm Al6082-T6 substrate