By Charlotte Blake and Josh Barras
Background
Extreme High-speed Laser Application (EHLA) is a novel coating technology first developed in 2017 and now entering the market. TWI has acquired the first EHLA system in the UK and is carrying out research to assess the suitability of the technology for various applications. EHLA promises a step-change in coating technology, maintaining a number of the benefits of the conventional Laser Metal Deposition (LMD)/laser cladding process, while addressing some limitations, such as the maximum coating coverage rate, coating thickness (maximum or minimum), surface quality, bond integrity and dilution level between material and substrate.
EHLA technology is similar to laser cladding/LMD, but differs in some details, which result in a significant increase in deposition rate. EHLA coverage rates can be increased to at least 250cm2min-1. This is achieved through an earlier introduction of the metal powder into the path of the laser beam, resulting in lower dilution and ultimately thinner coatings, while using higher power (>1kW) to melt and fuse material quickly. In conventional LMD, the powder and laser beam meet primarily at the melt pool generated on the surface of the substrate. In EHLA a shallower and more quickly solidifying melt pool is generated, with a narrower HAZ. Please see “What is Extreme High-Speed Laser Application (EHLA)?” for more details.
This report provides a brief overview of coating technologies (thermal spraying, conventional LMD, weld overlay, and electrodeposition), and notes the potential Health, Safety and Environmental (HSE) benefits of EHLA for preparing chromium-based hard coatings. The EHLA state-of-the-art and current applications are reviewed; however, this is a new process so there is relatively little published information. Finally, the report includes a short discussion of the growth potential of the technology.
Key Findings
EHLA is an emerging technology for the application of coatings to rotating substrates, with potential for future development to freeform surfaces and additive manufacturing applications. However, while significant knowledge can be carried over from conventional LMD to support the development of understanding around the EHLA process, there are key differences between the technologies. These require detailed investigation, ranging from process physics and modelling, to the characteristics of the resultant materials. Fundamental process research will support the maturing of this technology and strengthen understanding of its applications, benefits, and limitations.
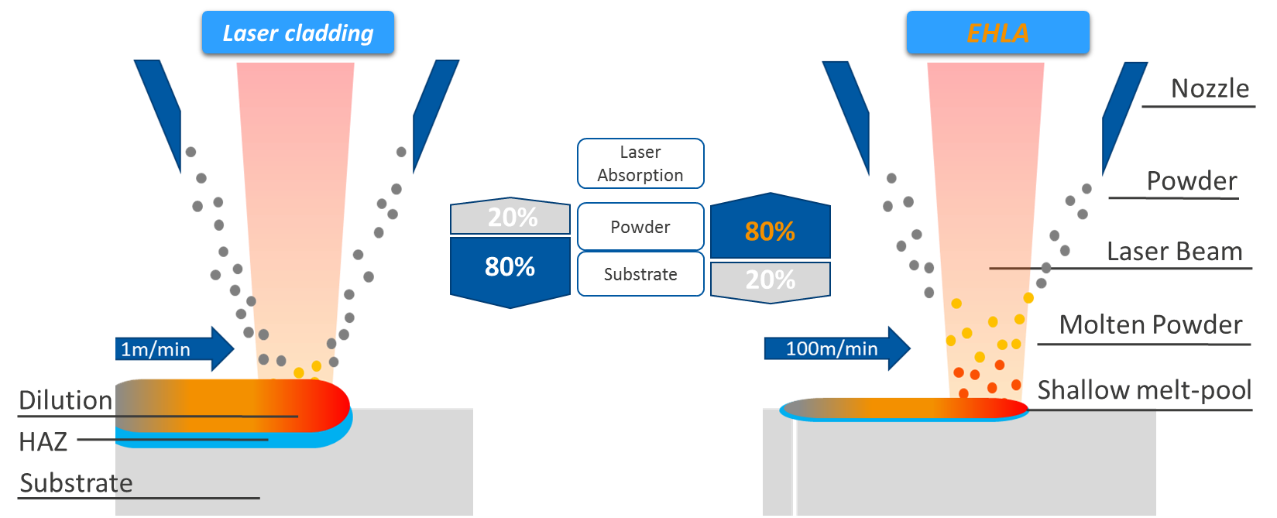
Laser power input, high speed, and powder melting in the beam for EHLA (right) contribute to high coverage rate, thin coatings with low dilution and a narrow HAZ, compared with conventional LMD (left)