By Chris Worrall and Michelangelo Mortello
Background
As engineered structures become more optimised, greater emphasis is placed on the use of multi-materials, as designers strive to use ‘the right material in the right place’. Composites offer high specific strength and stiffness, corrosion resistance and fatigue resistance, whereas metals provide solutions for higher temperature resistance, energy absorption, high bearing load resistance, and (typically) lower cost. Automotive and aerospace companies are increasingly looking to use carbon fibre composites to achieve up to 50% weight savings over metallic alternatives. However, it is unlikely that these industries will adopt a 100% composite solution, and the optimum design will inevitably comprise both composites and metals.
Substituting metal parts with composite products is still limited by manufacturing related factors and mechanical requirements, especially when high mechanical forces with variable direction are present. Nevertheless, composites can be used successfully as standalone elements, but can also be adopted alongside metallic materials. The properties of different materials can be jointly utilised to enhance the product performance against specific loads and working environments.
Currently, mechanical fastenings and adhesive bonding are the predominant methods used for joining composites to metals. These methods have found widespread use and may often be the best joining solutions. However, they can suffer from several drawbacks, which limit the adoption of more advanced multi-material joining applications and reduce potential benefits of optimised designs. Consequently, there is a clear need for new, flexible, cost-effective, and rapid methods for joining composites to metals.
This review explores two different approaches to hybrid joining: a composite technology approach (embedded carbon fibre transition zone) and a laser technology approach (laser riveting). The report establishes the current state-of-the-art of composite-to-metal joining, focussing on the two proposed joining approaches.
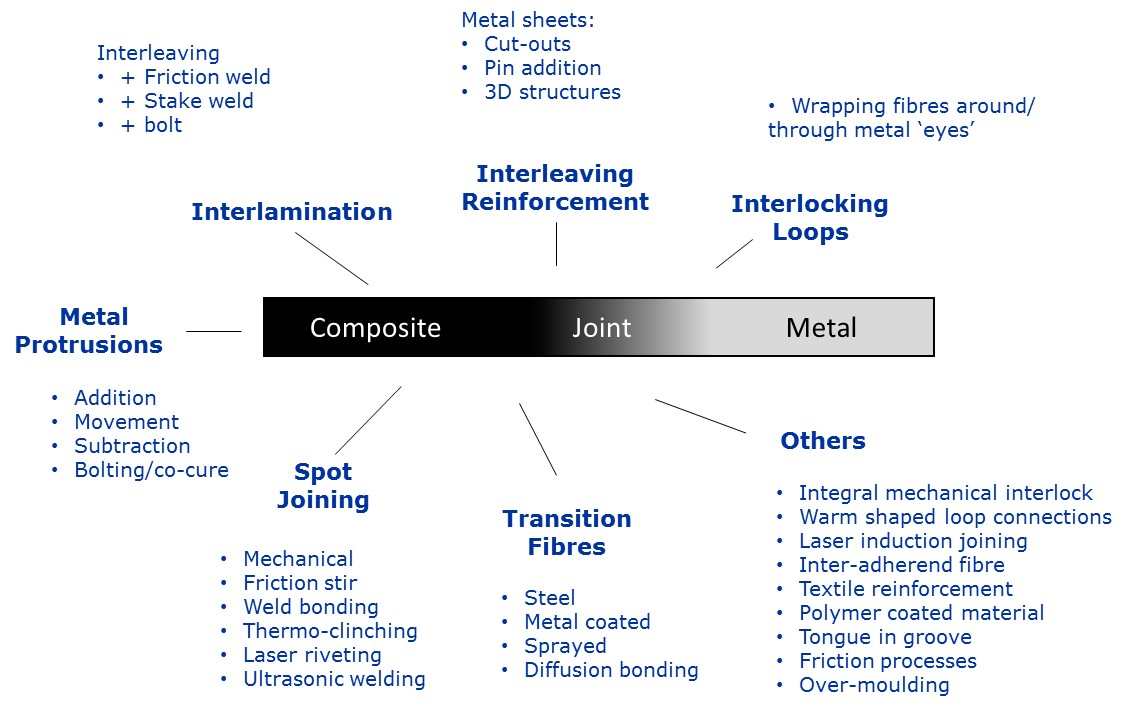
Summary of the main approaches (other than mechanical fastening and adhesive bonding) used for joining composites to metals