What is Industry 4.0?
Industry 4.0 refers to the fourth industrial revolution, although it is concerned with areas that are not usually classified as industry applications in their own right, such as smart cities.
What is the Fourth Industrial Revolution?
The first industrial revolution came with the advent of mechanisation, steam power and water power.
This was followed by the second industrial revolution, which revolved around mass production and assembly lines using electricity.
The third industrial revolution came with electronics, I.T. systems and automation, which led to the fourth industrial revolution that is associated with cyber physical systems.
Industry 4.0 Technologies
Generally-speaking, Industry 4.0 describes the growing trend towards automation and data exchange in technology and processes within the manufacturing industry, including:
This automation creates a manufacturing system whereby machines in factories are augmented with wireless connectivity and sensors to monitor and visualise an entire production process and make autonomous decisions.
Wireless connectivity and the augmentation of machines will be greatly advanced with the full roll out of 5G. This will provide faster response times, allowing for near real time communication between systems.
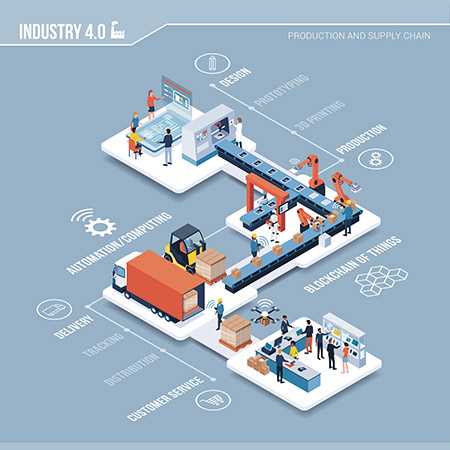
The fourth industrial revolution also relates to digital twin technologies. These digital technologies can create virtual versions of real-world installations, processes and applications. These can then be robustly tested to make cost-effective decentralised decisions.
These virtual copies can then be created in the real world and linked, via the internet of things, allowing for cyber-physical systems to communicate and cooperate with each other and human staff to create a joined up real time data exchange and automation process for Industry 4.0 manufacturing.
This automation includes interconnectivity between processes, information transparency and technical assistance for decentralised decisions.
In short, this should allow for digital transformation. This will allow for automated and autonomous manufacturing with joined-up systems that can cooperate with each other.
The technology will help solve problems and track processes, while also increasing productivity.
What is an Example of the Industry 4.0 Revolution?
Industry 4.0 has already been demonstrated through business models such as offline programming and adaptive control for arc welding, taking the process from product design through simulation and onto the shop floor for production.
There are also examples of businesses implementing Industry 4.0 in automotive manufacture and a variety of smart factories across the world.
Industry 4.0 at TWI
TWI has been exploring Industry 4.0, with a particular focus on its application to joining and associated technologies. Digital manufacturing is a key area for development through TWI projects and industrial case studies.
These projects include those related to areas such as rapid prototyping, electronics and sensors, and also digital twin for inspection purposes.
TWI’s expertise means that we remain at the forefront of this emerging array of processes, technologies and applications across a variety of industry sectors.
What are the Details of Industry 5.0?
Industry 5.0 is already being spoken about and involves robots and smart machines allowing humans to work better and smarter.
Esben Østergaard, Universal Robots chief technology officer and co-founder, explained, “Industry 5.0 will make the factory a place where creative people can come and work, to create a more personalised and human experience for workers and their customers."
By connecting the way in which man and machine work together, estimates say that Industry 5.0 will mean that over 60% of manufacturing, logistics and supply chains, agri-farming, and the mining and oil and gas sectors will employ chief robotics officers by 2025.
The European Economic Social Committee asserts that, "The proliferation of robotic automation is inevitable.”
Further Information