The previous Connect article, number 95, dealt with the methods of determining the weight of deposited weld metal in a joint, enabling the cost of welding consumables to be calculated.
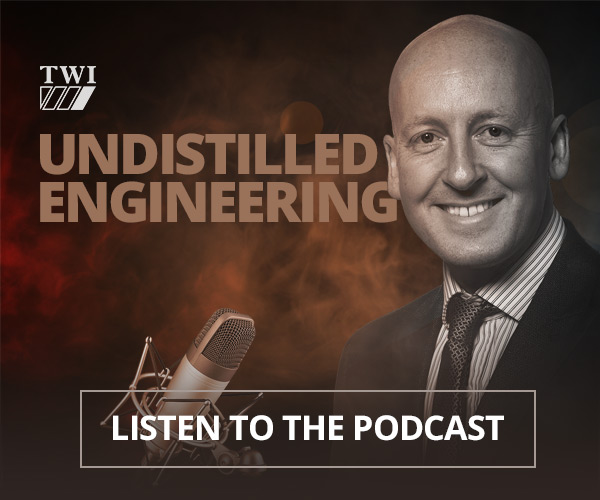
This is obviously the first step towards calculating the cost of actually making a welded joint but there are many other factors that need to be considered but which are beyond the scope of these articles.
The most significant of these costs is the overhead; the cost of providing a welding workshop or site and the costs of managing and running the organisation.
These costs are dependent on the accounting practices of the organisation. They comprise factors such as rent, rates, bank interest, cost of indirect workers, ie those not directly involved in fabricating, depreciation of plant etc. In addition, other accounting decisions (for example, where the costs of machining and assembly are absorbed) may affect the decisions on which is the most cost-effective joining method.
One of the most significant costs is that of labour and this inevitably varies with industry, time and country. The costs mentioned above cannot generally be influenced by the decisions made by a welding engineer. These articles will therefore concentrate on those aspects of welding activities that are not subject to accounting practices, overhead or labour costs.
There are many costs, other than the cost of depositing weld metal that will affect the price of a welded fabrication.
The work done by the designer in designing the most cost-effective joint in an item that can be placed in the most advantageous position for welding will have major effect on costs. For example, the type of joint preparation the designer selects; a single or double-V preparation can be flame cut, a J-preparation must be machined and is generally far more expensive. A machined J-preparation, however, may have less volume than a single-V, depending on thickness; will be more accurate and therefore quicker to assemble within tolerance and may result in a lower repair rate leading to a lower cost than the V preparation.
Costs that are directly affected by welding engineering decisions, in addition to the cost of actually depositing weld metal, are therefore; joint preparation, assembly time (which includes positioning in any jig or fixture and tacking), cleaning and dressing the weld, removal from jigs or fixture, post weld heat treatment, costs of non-destructive testing and cost of repairs.
The amount of weld metal deposited is rarely the same as the amount of filler metal purchased. This is the result of losses when, for example, GMAW or submerged arc welding wire is trimmed back to the contact tip, when the wire reel runs out and the length of wire between the drive roll and the contact tip is scrapped or the wire or reel is damaged.
Such losses tend to be quite small but this is not the case with coated electrodes. Damaged flux coatings, incorrectly stored electrodes and the stub ends discarded by the welder all contribute to as much as a third of the purchased weight of manual metallic arc electrodes being scrapped. Some electrode manufacturers' catalogues give figures for these losses which can vary depending on electrode type and diameter.
To assist in calculating the amount of welding consumables to be purchased Table 1 gives some multiplication factors for the more common arc welding processes. The weight of weld metal in the joint should be multiplied by this factor to give the amount of welding consumable required. These figures assume good housekeeping and shop floor discipline such that consumables are not wasted or scrapped unnecessarily.
Table 1 Multiplication factor. Weight of weld metal to give the weight of filler metal required.
Arc welding process | Multiplication factor |
MMA (SMAW) |
1.5 |
TIG (GTAW) |
1.1 |
MIG/MAG (GMAW) |
1.05 |
Sub Arc (SAW) |
1.02 |
FCAW |
1.2 |
MCAW |
1.1 |
The other consumables in this cost equation are shielding gases or flux.
The conventional shoulder height welding gas cylinder contains approximately 10,000 litres of shielding gas at a pressure of 200bar. As the gas flow rates normally used in production are around 12 to 15 litres per minute, this typical cylinder should provide in the region of 10 to 12 hours of welding time, allowing for losses at the beginning and end of the arcing period.
The rate of flux consumption in submerged arc welding is approximately 1kg of flux for every 1kg of deposited weld metal. This assumes good housekeeping and an efficient flux recirculation system. Calculation of the amount required (and hence the cost) of these consumables is therefore relatively straightforward.
The cost of the welder's time to weld a joint does not depend solely on the deposition rate of the process. A most important factor in determining the time required by the welder is what is known as the 'duty cycle' or 'operating factor'. This is a percentage figure giving the amount of time that the arc is burning and weld metal is being deposited versus the total time that the welder is working.
Table 2 gives some figures for the more common arc welding processes. Note that these do NOT include set-up or assembly time and individual circumstances can increase or decrease these figures.
Table 2 Duty cycles for arc welding processes
Arc welding process | Duty cycle % |
MMA (SMAW) |
15 - 30 |
TIG (GTAW) |
25 - 40 |
Mechanised TIG |
80 - 90 |
MIG/MAG (GMAW) |
30 - 45 |
Mechanised MIG/MAG |
80 - 90 |
Sub Arc (SAW) |
80 - 95 |
FCAW |
25 - 45 |
Mechanised FCAW |
70 - 85 |
MCAW |
30 - 45 |
The lost time in this figure can be accounted for by considering all of the other activities that the welder performs. In MMA welding, for example, time is required for tacking, de-slagging and cleaning a weld pass, for changing electrodes, for changing position, for rest breaks and for removal of the item from a fixture. Similar activities need to be performed using the other welding processes.
Increasing the duty cycle is therefore one method of increasing productivity, either by organising the shop floor such that lost time is reduced or by the use of a higher duty cycle process. However, remember that the arcing time may well be only a very small proportion of the total time to manufacture and attention to other aspects of the manufacturing cycle may give better returns than simply increasing the welding duty cycle.
Reference to Table 2 also suggests that mechanisation is one method to increase the duty cycle. Caution needs to be exercised, however, if the total (floor to floor) time is to be reduced. For one-off or small batch items the time taken to prepare and set up a mechanised system to weld the item may be longer than that taken to weld using a manual process. Note also that if a mechanised system is used, the duty cycle may in fact decrease, as the welding speed is increased and the weld is completed in a shorter time although the number of items welded per day will increase. It is therefore essential to consider the complete manufacturing cycle to achieve the most cost effective solution.
Part 2
This article was written by Gene Mathers.