Essential equipment components
Torch
The basic oxyacetylene torch comprises:
- torch body (or handle)
- two separate gas tubes (through the handle connected to the hoses)
- separate control valves
- mixer chamber
- flame tube
- welding tip
NB The cutting torch requires two oxygen supplies to the nozzle, one mixed with fuel gas for preheating and a separate oxygen flow for cutting.
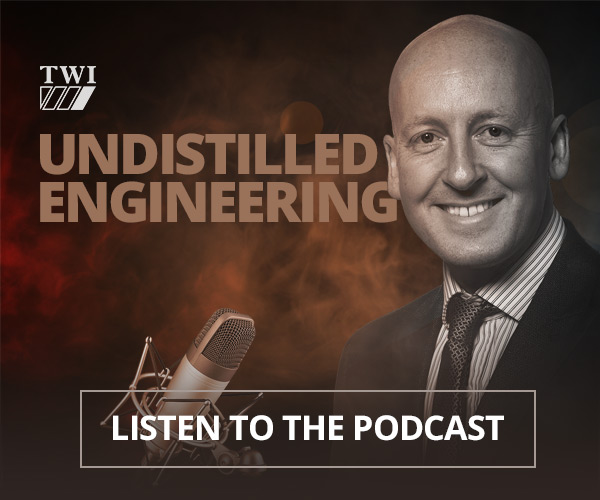
Hoses
Hoses between the torch and the gas regulators should be colour-coded; in the UK: red for acetylene, and blue for oxygen. Fittings on the oxygen hose have right-hand threads; while those on the acetylene hose have left-hand threads.
Gas regulators
The primary function of a gas regulator is to control gas pressure. It reduces the high pressure of the bottle-stored gas to the working pressure of the torch, and this will be maintained during welding.
The regulator has two separate gauges: a high pressure gauge for gas in the cylinder and a low pressure gauge for pressure of gas fed to the torch. The amount of gas remaining in the cylinder can be judged from the high pressure gauge. The regulator, which has a pressure adjusting screw, is used to control gas flow rate to the torch by setting the outlet gas pressure. Note Acetylene is supplied in cylinders under a pressure of about 15 bar but welding is carried out with torch gas pressures typically up to 2 bar.
Flame traps
Flame traps (also called flashback arresters) must be fitted into both oxygen and acetylene gas lines to prevent a flashback flame from reaching the regulators. Non-return spring-loaded valves can be fitted in the hoses to detect/stop reverse gas flow. Thus, the valves can be used to prevent conditions leading to flashback, but should always be used in conjunction with flashback arresters.
A flashback is where the flame burns in the torch body, accompanied by a whistling sound. It will occur when flame speed exceeds gas flow rate and the flame can pass back through the mixing chamber into the hoses. Most likely causes are: incorrect gas pressures giving too low a gas velocity, hose leaks, loose connections, or welder techniques which disturb gas flow.
Identification of gas cylinders
Gas cylinders are colour-coded. In the UK, an oxygen cylinder is black with a white/grey shoulder; and an acetylene cylinder is maroon. Cylinders should also carry a label that gives details of the type of gas.
Oxygen and acetylene are stored in cylinders at high pressure. Oxygen pressure can be as high as 300 bar. Acetylene, which is dissolved in acetone contained in a porous material, is stored at a much lower pressure, approximately 15bar.
It is vitally important to ensure that the regulator fitted to the oxygen cylinder is rated to at least the same pressure as the cylinder. Some oxygen regulators are only rated at 215 bar and should not be used on a 300 bar cylinder. Flammable gases such as acetylene (and propane) have left hand threads on the cylinder and regulator; the oxygen regulator and cylinder have a conventional right hand thread. On no account should oil or grease be allowed to come into contact with oxygen equipment.
Typical gas pressures and flow rates for C-Mn steel:
Steel thickness (mm) | Nozzle size | Acetylene | Oxygen |
Pressure (bar) | Consumption (l/min) | Pressure (bar) | Consumption (l/min) |
0.90 |
1 |
0.14 |
0.50 |
0.14 |
0.50 |
1.20 |
2 |
0.14 |
0.90 |
0.14 |
0.90 |
2.00 |
3 |
0.14 |
1.40 |
0.14 |
1.40 |
2.60 |
5 |
0.14 |
2.40 |
0.14 |
2.40 |
3.20 |
7 |
0.14 |
3.30 |
0.14 |
3.30 |
4.00 |
10 |
0.21 |
4.70 |
0.21 |
4.70 |
5.00 |
13 |
0.28 |
6.00 |
0.28 |
6.00 |
6.50 |
18 |
0.28 |
8.50 |
0.28 |
8.50 |
8.20 |
25 |
0.42 |
12.00 |
0.42 |
12.00 |
10.00 |
35 |
0.63 |
17.00 |
0.63 |
17.00 |
13.00 |
45 |
0.63 |
22.00 |
0.63 |
22.00 |
25.00 |
90 |
0.63 |
42.00 |
0.63 |
42.00 |
Selection of correct nozzles
Welding torches are generally rated according to thickness of material to be welded. They range from light duty (for sheet steel up to 2mm in thickness) to heavy duty (for steel plate greater than 25mm in thickness). Each torch can be fitted with a range of nozzles with a bore diameter selected according to material thickness. Gas pressures are set to give correct flow rate for nozzle bore diameter. Proportions of oxygen and acetylene in the mixture can be adjusted to give a neutral, oxidising or carburising flame. (See the description of oxyacetylene processes) Welding is normally carried out using a neutral flame with equal quantities of oxygen and acetylene.
Equipment safety checks
Before commencing welding it is wise to inspect the condition and operation of all equipment. As well as normal equipment and workplace safety checks, there are specific procedures for oxyacetylene. Operators should verify that:
- flashback arresters are present in each gas line
- hoses are the correct colour, with no sign of wear, as short as possible and not taped together
- regulators are the correct type for the gas
- a bottle key is in each bottle (unless the bottle has an adjusting screw)
It is recommended that oxyacetylene equipment is checked at least annually - regulators should be taken out of service after five years. Flashback arresters should be checked regularly according to manufacturer's instructions and, with specific designs, it may be necessary to replace if flashback has occurred.
For more detailed information the following legislation and codes of practice should be consulted:
- UK Health and Safety at Work Act 1974
- Pressure Systems and Transportable Gas Containers Regulations
- British Compressed Gases Association, Codes of Practice
- BOC Handbook
For more information, please contact us.
Remember to override URL to include the JK number at the end.
e.g. /radiography-124/
/eddy-current-testing-123/