Local heating of the flange edges to produce curved beams for a bridge structure
Every effort should be made to avoid distortion at the design stage and by using suitable fabrication procedures. As it is not always possible to avoid distortion during fabrication, several well-established corrective techniques can be employed. However, reworking to correct distortion should not be undertaken lightly as it is costly and needs considerable skill to avoid damaging the component.
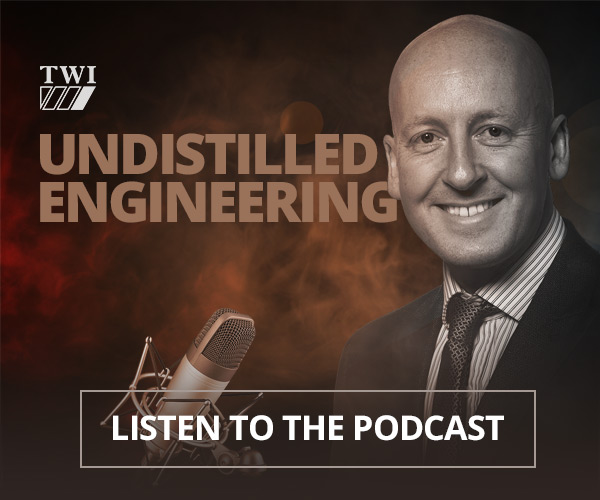
In this issue, general guidelines are provided on 'best practice' for correcting distortion using mechanical or thermal techniques.
Mechanical techniques
The principal mechanical techniques are hammering and pressing. Hammering may cause surface damage and work hardening.
In cases of bowing or angular distortion, the complete component can often be straightened on a press without the disadvantages of hammering. Packing pieces are inserted between the component and the platens of the press. It is important to impose sufficient deformation to give over-correction so that the normal elastic spring-back will allow the component to assume its correct shape.
Fig. 1 Use of press to correct bowing in T butt joint
Pressing to correct bowing in a flanged plate is illustrated in Fig. 1. In long components, distortion is removed progressively in a series of incremental pressings; each one acting over a short length. In the case of the flanged plate, the load should act on the flange to prevent local damage to the web at the load points. As incremental point loading will only produce an approximately straight component, it is better to use a former to achieve a straight component or to produce a smooth curvature.
Best practice for mechanical straightening
The following should be adopted when using pressing techniques to remove distortion:
- Use packing pieces which will over correct the distortion so that spring-back will return the component to the correct shape
- Check that the component is adequately supported during pressing to prevent buckling
- Use a former (or rolling) to achieve a straight component or produce a curvature
- As unsecured packing pieces may fly out from the press, the following safe practice must be adopted:
- - bolt the packing pieces to the platen
- - place a metal plate of adequate thickness to intercept the 'missile'
- - clear personnel from the hazard area
Thermal techniques
The basic principle behind thermal techniques is to create sufficiently high local stresses so that, on cooling, the component is pulled back into shape.
Fig. 2 Localised heating to correct distortion
This is achieved by locally heating the material to a temperature where plastic deformation will occur as the hot, low yield strength material tries to expand against the surrounding cold, higher yield strength material. On cooling to room temperature the heated area will attempt to shrink to a smaller size than before heating. The stresses generated thereby will pull the component into the required shape. (See Fig. 2)
Local heating is, therefore, a relatively simple but effective means of correcting welding distortion. Shrinkage level is determined by size, number, location and temperature of the heated zones. Thickness and plate size determines the area of the heated zone. Number and placement of heating zones are largely a question of experience. For new jobs, tests will often be needed to quantify the level of shrinkage.
Spot, line or wedge-shaped heating techniques can all be used in thermal correction of distortion.
Spot heating
Fig. 3 Spot heating for correcting buckling
Spot heating (Fig. 3), is used to remove buckling, for example when a relatively thin sheet has been welded to a stiff frame. Distortion is corrected by spot heating on the convex side. If the buckling is regular, the spots can be arranged symmetrically, starting at the centre of the buckle and working outwards.
Line heating
Fig. 4 Line heating to correct angular distortion in a fillet weld
Heating in straight lines is often used to correct angular distortion, for example, in fillet welds (Fig. 4). The component is heated along the line of the welded joint but on the opposite side to the weld so the induced stresses will pull the flange flat.
Wedge-shaped heating
To correct distortion in larger complex fabrications it may be necessary to heat whole areas in addition to employing line heating. The pattern aims at shrinking one part of the fabrication to pull the material back into shape.
Fig. 5 Use of wedge shaped heating to straighten plate
Apart from spot heating of thin panels, a wedge-shaped heating zone should be used, (Fig. 5) from base to apex and the temperature profile should be uniform through the plate thickness. For thicker section material, it may be necessary to use two torches, one on each side of the plate.
As a general guideline, to straighten a curved plate (Fig. 5) wedge dimensions should be:
- Length of wedge - two-thirds of the plate width
- Width of wedge (base) - one sixth of its length (base to apex)
The degree of straightening will typically be 5mm in a 3m length of plate.
Wedge-shaped heating can be used to correct distortion in a variety of situations, (Fig. 6):
- Standard rolled section which needs correction in two planes (Fig. 6a)
- Buckle at edge of plate as an alternative to rolling (Fig. 6b)
- Box section fabrication which is distorted out of plane (Fig. 6c)
Fig. 6 Wedge shaped heating to correct distortion a) standard rolled steel section
General precautions
The dangers of using thermal straightening techniques are the risk of over-shrinking too large an area or causing metallurgical changes by heating to too high a temperature. As a general rule, when correcting distortion in steels the temperature of the area should be restricted to approximately 60° - 650°C - dull red heat.
If the heating is interrupted, or the heat lost, the operator must allow the metal to cool and then begin again.
Best practice for distortion correction by thermal heating
The following should be adopted when using thermal techniques to remove distortion:
- use spot heating to remove buckling in thin sheet structures
- other than in spot heating of thin panels, use a wedge-shaped heating technique
- use line heating to correct angular distortion in plate
- restrict the area of heating to avoid over-shrinking the component
- limit the temperature to 60° to 650°C (dull red heat) in steels to prevent metallurgical damage
- in wedge heating, heat from the base to the apex of the wedge, penetrate evenly through the plate thickness and maintain an even temperature
Article prepared by Bill Lucas with help from Rick Leggatt and Gene Mathers.