The main difference between this gouging technique and the others is that a separate air jet is used to eject molten metal from the groove.
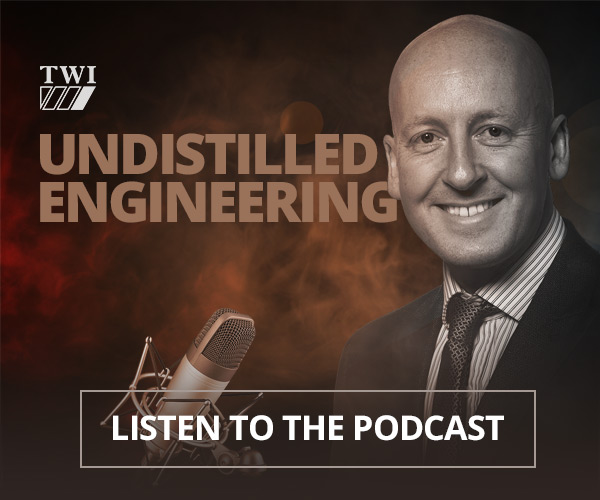
Process description
Air carbon arc gouging works as follows. An electric arc is generated between the tip of a carbon electrode and the workpiece. The metal becomes molten and a high velocity air jet streams down the electrode to blow it away, thus leaving a clean groove. The process is simple to apply (using the same equipment as MMA welding), has a high metal removal rate, and gouge profile can be closely controlled. Disadvantages are that the air jet causes the molten metal to be ejected over quite a large distance and, because of high currents (up to 2000A) and high air pressures (80 to 100 psi), it can be very noisy.
Application
As air carbon arc gouging does not rely on oxidation it can be applied to a wide range of metals. DC (electrode positive) is normally preferred for steel and stainless steel but AC is more effective for cast iron, copper and nickel alloys. Typical applications include back gouging, removal of surface and internal defects, removal of excess weld metal and preparation of bevel edges for welding.
Electrode
The electrode is a graphite (carbon) rod which has a copper coating to reduce electrode erosion. Electrode diameter is selected according to required depth and width of gouge. Cutting can be precisely controlled and molten metal/dross is kept to a minimum.
Power source
A DC power supply with electrode positive polarity is most suitable. AC power sources which are also constant current can be used but with special AC type electrodes. The power source must have a constant current output characteristic. If it does not, inadvertant touching of the electrode to the workpiece will cause a high current surge sufficient to 'explode' the electrode tip. This will disrupt the operation and cause carbon pick-up. As arc voltage can be quite high (up to 50V), open circuit voltage of the power source should be over 60V.
Air supply
The gouging torch is normally operated with either a compressed air line or separate bottled gas supply. Air supply pressure will be up to 100psi from the air line but restricted to about 35psi from a bottled supply. Providing there is sufficient air flow to remove molten metal, there are no advantages in using higher pressure and flow rates.
Carbon pickup
Although carbon is picked up by the molten metal, the air stream will remove carbon-rich metal from the groove to leave only minimal contamination of the side walls. Poor gouging technique or insufficient air flow will result in carbon pick-up with the risk of metallurgical problems, e.g high hardness and even cracking.
Typical operating data for air carbon arc gouging:
Electrode diameter (mm) | Current A Note: DC electrode | Gouging dimensions | Carbon electrode consumed (mm/min) | Gouging speed (mm/min) |
Depth (mm) | Width (mm) |
Manual |
6.4 |
275 |
6-7 |
9-10 |
120 |
609 |
8.0 |
350 |
7-8 |
10-11 |
114 |
711 |
9.5 |
425 |
9-10 |
12-13 |
100 |
660 |
13.0 |
550 |
12-13 |
18-19 |
76 |
508 |
Automatic |
8.0 |
300-400 |
2-9 |
3-8 |
100 |
1650-840 |
9.5 |
500 |
3-12 |
3-10 |
142 |
1650-635 |
13.0 |
850 |
3-15 |
3-13 |
82 |
1830-610 |
16.0 |
1250 |
3-19 |
3-16 |
63 |
1830-710 |
Operation
Gouging is commenced by striking the electrode tip on to the workpiece surface to initiate the arc. Unlike manual metal arc (MMA) welding the electrode tip is not withdrawn to establish arc length. Molten metal directly under the electrode tip (arc) is immediately blown away by the air stream. For effective metal removal, it is important that the air stream is directed at the arc from behind the electrode and sweeps under the tip of the electrode. The width of groove is determined by the diameter of electrode, but depth is dictated by the angle of electrode to the workpiece and rate of travel. Relatively high travel speeds are possible when a low electrode angle is used. This produces a shallow groove: a steep angle results in a deep groove and requires slower travel speed. Note, a steeply angled electrode may give rise to carbon contamination.
Oscillating the electrode in a circular or restricted weave motion during gouging can greatly increase gouging width. This is useful for removal of a weld or plate imperfection that is wider than the electrode itself. It is important, however, that weave width should not exceed four times the diameter of the electrode. The groove surface should be relatively free of oxidised metal and can be considered ready for welding without further preparation. Dressing by grinding the side-walls of the gouge should be carried out if a carbon rich layer has been formed. Also, dressing by grinding or another approved method will be necessary if working on crack-sensitive material such as high strength, low alloy steel.