CoreFlow® is a highly disruptive, sub-surface machining technique invented at TWI. This solid state process is a development of friction stir welding (FSW) and friction stir channelling (FSC) which allows for sub-surface networks of channels to be integrated into two-dimensional or three-dimensional monolithic parts in a single manufacturing step. These channels can then be used for heat exchange or other applications.
History and Development of CoreFlow®
For over 75 years, our customers have trusted us to deliver Technical Excellence, and TWI has remained at the forefront of solid phase friction welding and processing technology. Active and innovative in welding research and development since the 1960s, TWI has been responsible for many key innovations and developments in solid phase joining. The most notable examples are friction stir welding (FSW), which was invented at TWI in 1991, and the development of linear friction welding (LFW) into a mature joining process for turbine blades.
Friction stir channelling (FSC) is an innovative solid-state process, derived from FSW, for integrating sub-surface networks within metal structural elements. In 2005, the original FSC concept was patented by Rajiv S. Mishra. In his work, poor material consolidation during FSW was deliberately promoted in order to produce a continuous void along the tool path. However, despite its great potential, this technology had not been adopted by industry, mainly by not fulfilling the required repeatability, surface finish or design flexibility.
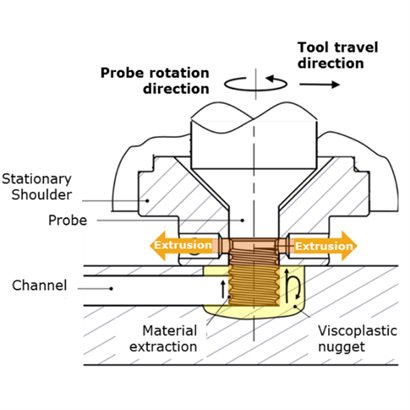
CoreFlow® tooling description and main process parameters
TWI invented and patented a new stationary shoulder variant of FSC (SSFSC) which has proven to overcome many of the drawbacks of conventional FSC. A stationary shoulder is employed to confine the nugget of viscoplastic material, limiting the flow of material extracted by the probe. With the appropriate rotation direction, the geometrical features of the probe cause part of the nugget material to be conveyed into the shoulder. The material extracted is then re-directed towards a series of vents in the shoulder and expelled.
As the tool assembly traverses along a pre-defined path, the process of extracting the material leads to the formation of i) a closed channel within the workpiece and ii) the production of extruded wire. Process parameters and tool designs are combined such that the rate of material extraction per unit distance is limited to maintain a fully consolidated channel ceiling.
The cycle is initiated by plunging the rotating probe into the plate. Once the probe reaches its target plunge depth, the machine initiates its traverse motion. As the tool traverses along the workpiece, the plasticised material is conveyed upwards by the rotating probe threads, into the shoulder and then expelled as extruded material. This subtraction of material leads to the formation of a closed sub-surface channel.
It is interesting to note that the material extruded from the plate in the form of wire could be used as feedstock for other processes, like wire-based additive manufacturing, or could be used simply as welding wire. CoreFlow®, indeed, is capable of extruding an unlimited length of wire from a plate or a pipe.
This process, labelled ForgeWire, is of great interest for producing spool of wire from materials with poor extrudability, such as alloys of aluminium or magnesium. Wire manufacturers or additive manufacturing process developers now have a quick option for producing wire with a tailored chemical composition and from experimental alloy formulations (e.g. Aluminium-Lithium or Aluminium-Scandium), potentially even directly from rolled product or cast billets.
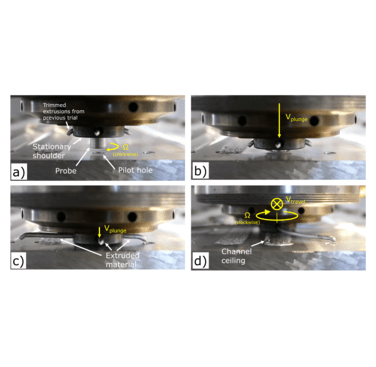
Main stages of the CoreFlow® cycle: (a) Start of probe spindle rotation; (b) Plunge into workpiece; (c) Probe is engaged with the workpiece and shoulder contacts the workpiece surface which initiates material extrusion; (d) Tool traverses along a defined path to form a sub-surface channel with consolidated channel ceiling, extruding material as it travels
Demonstrators and Channel Cross Section
In the last few years, the CoreFlow® concept has been demonstrated and further developed by TWI. AA6082-T6 and AA1050-H14 plates have been successfully processed, with a thickness varying from 5 to 50 mm. Moreover, flat and tubular demonstrators were successfully manufactured, featuring channels along linear, curved and helical trajectories. The demonstrators passed both leaking and pressure testing, with leak rates well below 10-8 mbar∙L/s and pressure up to 9 bar.
The channel cross-section geometry varies from rectangular to triangular, depending on the parameters used. All channels feature a flat bottom surface, with well-defined edges, coincident with the probe outline, as shown in the figure. From the micrograph it is also possible to appreciate how the anisotropic grain orientation in the parent material, caused by the plate sample rolling process, transforms into a fully recrystallized microstructure in the channel ceiling due to the stirring action of the probe in the viscoplastic material.