Friction stir welding (FSW) is a solid state joining process that uses frictional heat generated by a rotating tool to join materials.
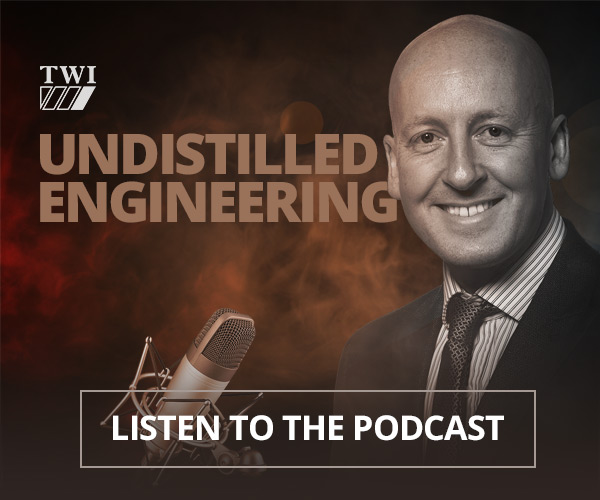
The non-consumable tool, with a profiled probe and shoulder, is rotated and plunged into the interface between two work pieces. It then traverses along the joint line, causing the material to heat and soften. The shoulder also acts to contain this plasticized material, which is mechanically mixed to create a solid phase weld.
Applications
The process is primarily used in industry to join aluminium alloys of all grades, whether cast, rolled or extruded. FSW has been shown to weld aluminium alloy butt joints with a thickness of between 0.3mm and 75mm in a single pass, depending on the alloy grade and capability of the FSW machine.
Other materials that have been joined with FSW include magnesium, titanium, copper, nickel and steel alloys, while plastics and metal matrix composites (MMC) have also been explored. This process has also been shown to be able to join dissimilar combinations of these materials including aluminium to steel.
FSW has been used for a variety of applications across industries ranging from aerospace to shipbuilding and rail to electronics, including EV battery trays.
Mechanical Properties and Microstructure
The mechanical properties of friction stir welded aluminium alloys have been proven better than those found with other welding processes, such as arc welding.
With regard to the mechanical properties of FSW, this process typically has three main microstructural regions; a weld nugget, a thermo-mechanically affected zone (TMAZ) and a heat affected zone (HAZ).
While both the weld nugget and the TMAZ are ‘thermo mechanically affected zones,’ they are considered separately when it comes to the microstructural features. This is because the weld nugget experiences dynamic recrystallization while the TMAZ does not. However, the exact composition and extent of the microstructural composition in these zones depends upon the material and processing conditions. These can, for example, alter depending on factors such as welding parameters and the design of the FSW tool used.
What are the Advantages?
Friction stir welding offers a number of advantages over conventional arc welding processes. These include:
- As a solid state welding process, FSW is a largely defect free joining method with no hot cracking, porosity or solidification cracks
- Due to the lower temperatures there is a reduction in shrinkage and distortion in the material being joined
- No filler materials, flux or shielding gas requirement for aluminium alloys
- FSW is environmentally friendly as it produces no fume, spatter, or UV radiation
- Uses machine tool technology, making the process easy to automate, highly repeatable and reducing need for skilled welders
- Can work in any position
- Good mechanical properties, which for aluminium alloys typically equals or exceeds those obtainable by competing processes
- Energy efficient
- Able to join many ‘non-weldable’ aluminium alloys, such as those from the 2xxx and 7xxx series
- No requirement for special edge preparation in most applications
What are the Disadvantages?
While friction stir welding provides many advantages, there are a few limitations associated with the process. These include:
- Exit hole left after withdrawing tool from the materials to be joined; however, this can usually be accounted for in the design of the part or by using run on/off tabs
- The need for significant down force and traversing forces means that clamping on the parts to be joined is more substantial than for arc welds
- Gaps between the parts to be joined needs to be controlled as no filler material is used in the process
History
Friction stir welding was invented by Wayne Thomas at TWI in 1991, with patents filed in Europe, the USA, Japan and Australia. Further work to study the process was undertaken at TWI in 1992 with the project titled, ‘Development of the New Friction Stir Technique for Welding Aluminum.’ Industrial production using FSW was in progress by the mid-1990s, making it one of the shortest time periods for any welding process to go from invention to widespread use.
Our Expertise
TWI has gone on to develop extensive knowledge of the friction stir welding process over many years of research and development. This has led to the creation of a number of variants and associated processes, such as Bobbin FSW, Stationary Shoulder FSW, Supported FSW and AdStir.
Find out more about TWI’s work