Increasing thickness capability
A second family of tools has been developed by Element Six capable of welding steel up to 12mm thick and these too are now undergoing testing at TWI. Single pass, square butt welds have been produced in a range of steels including S355, S460 and DH36 using these tools. 2D lap welds, simulating the attachment of a patch to a ship’s hull plate have also been performed with these 12mm tools. Such a weld is shown below.
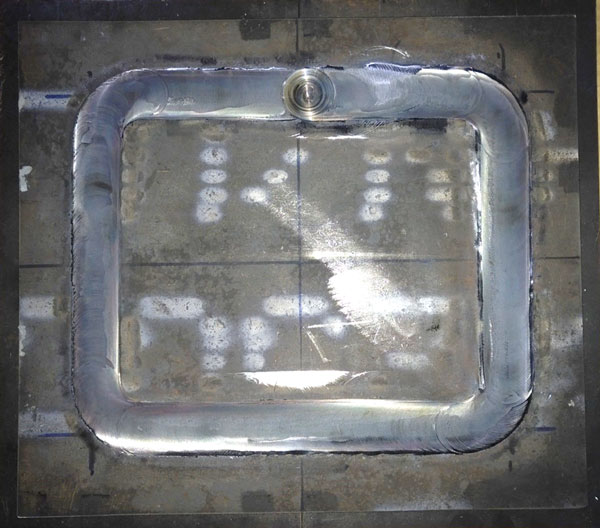
DH36 steel patch welded, as a 2D lap weld, to a plate of S460 steel
Weld mechanical properties
The fine grained microstructure seen in friction stir welds generally provides them with tensile strength properties closer to the parent metal than is typically the case with conventional fusion welding. With steel, this benefit is further enhanced by the fact that welding takes place in the transformation temperature range and careful selection of the welding parameters can exert a useful degree of control over the phase transformations that take place during the welding process. It is possible, for example to make welds optimised for strength or for toughness, or a combination of both, depending upon the service requirement. It is generally the case that friction stir welds in steel are found to be stronger than the parent metal in which they were made. Where friction stir welds are made between dissimilar grades of steel, for example a carbon steel and a stainless steel, the failure tends to occur in the weaker of the two parent metals and away from the weld zone.
A number of samples were taken from a single pass butt weld made in 6mm thick S355 steel with E6 tools that had accumulated more than 60m of welding and subjected to mechanical testing. These samples passed a root and face bend test, an indication that the samples had no significant defects and had a good degree of ductility in the weld zone. The cross weld tensile test specimens failed in a ductile manner in the parent metal some distance from the weld and HAZ.
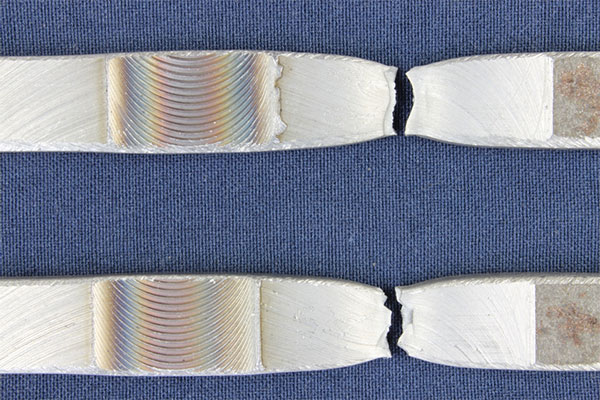
Cross weld tensile test specimens in S355 steel showing parent metal failures
The fine, multiphase microstructures generated by steel FSW give rise to welds that can also be tougher than the parent metal. Samples were taken from a FSW weld in 6mm thick S355 steel produced by a tool that had made over 60m of accumulated weld and subjected to Charpy impact testing. The Charpy impact testing was performed at -20oC and in accordance with BS EN ISO 148-1:2016. The samples were removed from mid weld thickness and notched in the welding direction through the thickness on the weld metal centreline.
Impact strengths of 49, 57 and 61 Joules KV were recorded for the three test pieces, with the mean being 56J. This is considerably in excess of the minimum specified parent metal value for S355 at -20oC, which is 27 J KV.
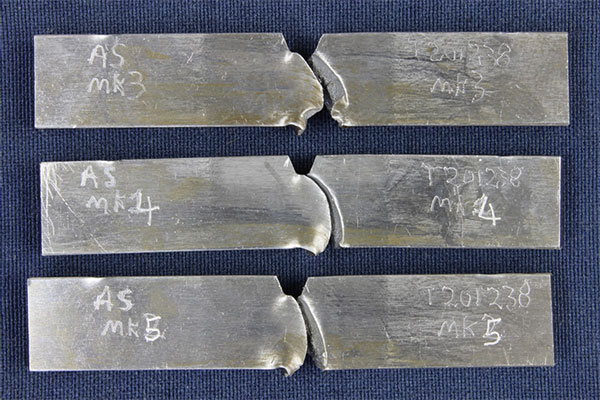
Charpy impact test specimens, notched in the weld zone
Dissimilar welds
As FSW is a solid state, i.e. no melting, welding process it is far less influenced by the alloy content of the steels being welded. It is therefore possible to weld different grades of steel together more easily than with other techniques, including carbon to Duplex stainless steels, and to weld steel grades that are found challenging to weld by other processes.
The image below shows a dissimilar metal weld made between S355 carbon steel and S32205 Duplex stainless steel. From the micrograph it can be seen that no alloying has taken place between the two different steel grades, the joint is made purely by mechanical mixing. No alloying elements have been lost from either of the two grades in the weld zone, nor has elemental segregation occurred in this region. The Duplex stainless steel retained the phase balance of the original parent metal, albeit with a much finer grain size in the weld zone.
Samples taken from the weld passed both face and root bend tests, and under tensile testing the sample failed in the parent carbon steel away from the weld area.
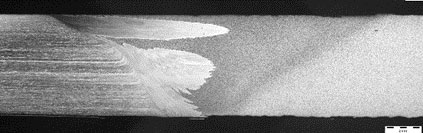
Metallographic section through a weld made between 8mm thick S355 carbon steel and S32205 Duplex stainless steel
Potential uses of FSW in steel
TWI is looking at a wide range of potential FSW applications in steel. These include:
Underwater fabrication and repair
Friction stir welding works underwater, where it produces high integrity welds with none of the issues associated with other underwater welding techniques. This capability is being developed in the RESURGAM (Robotic Survey, Repair & Agile Manufacture) project which will combine the development of FSW technology for steel with the introduction of digital manufacturing techniques for both the initial modular fabrication of ships across multiple sites and the in water repair of damaged ships or marine structures. The FSW element of the project will look at developing a suite of FSW tools able to weld multiple grades of steel from 2 to 12mm in thickness, in air and under water. These tool developments will be accompanied by the development of a modular FSW system that can be retrofitted to existing CNC milling and machining centres and a robotic system that can be deployed underwater to make in situ repairs.
Live oil pipeline repair
In addition to working under water, FSW has been shown to be capable of working under oil too, allowing repair welds to be made in live oil pipelines and fuel storage tanks. This application is being developed in the FSWBOT project, where a robotic system derived from a PIG will be utilised to travel through a pipeline to repair corrosion defects without the need for the oil flow to be halted.
For more information on friction stir welding of steel and how TWI can support you in this process, please contact us.