Project Code: 35268
Start date and planned duration: January 2023, 24 months
Objective
- Establish AE’s detectability and GW sizing accuracy of pit-to-crack transition and crack propagation stages on specimen 3 m long pressurized pipelines.
- Investigate advanced digitalisation techniques for fusing AE and GW data.
- Validate AE and GW results with conventional Ultrasonic Testing (UT) and Fitness-For-Service (FFS) assessments.
- Provide recommendations for optimum implementation of AE and GW for SHM of pipelines.
Project Outline
Since the only pressure containing structures that TWI has access to are pipes, the proof of concept will use these. The project will be carried out in two stages.
First stage entails testing a 10 metre long pipe currently located at TWI’s graveyard. This pipe was previously inspected using GW as part of PN 25607 therefore the acquisition settings and the procedure is known. This stage will simulate active corrosion using an electrochemical method while continuously monitoring the pipe. AE has been proven to detect corrosion as part of SCP 33526 and CRP 34244. However, the maximum sensor spacing has not been investigated and will be established. GW inspections will be carried out at certain time intervals in order to size the metal loss coming from active corrosion. The corrosion will be simulated at the centre and both ends of the pipe as shown in Figure 1. The objective is to establish the maximum AE sensor spacing for corrosion detection as well as to assess the sizing accuracy of GW and provide recommendations for a potential field implementation.
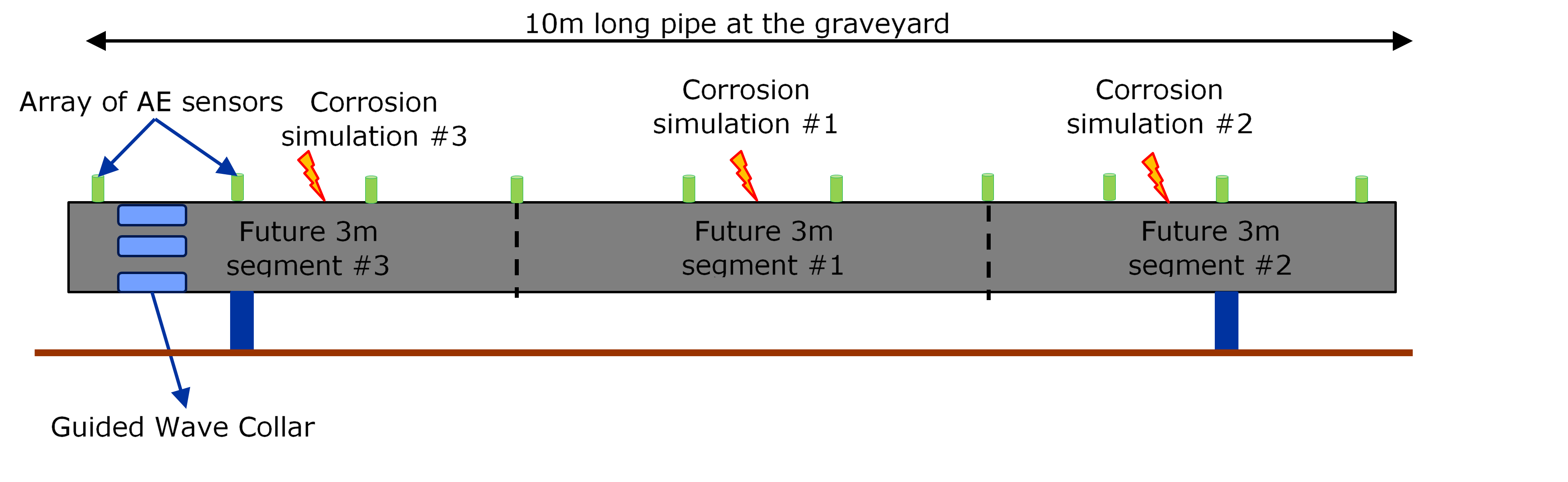
Figure 1 10m long pipe – Active corrosion simulation
The second stage entails pressure testing 3m long pipe segment cut from the original 10m long pipeline. The 3 metre long segment is selected due to current limitations for pressure testing. The segment will feature a corrosion defect at the centre as shown in Figure 2. The defect will act as a realistic stress raiser and by subjecting it to normal operating pressure, a pit-to-crack- transition is promoted. The pipe will be instrumented with a coarser array of AE sensors in order to localise and track the signals coming from this transition. AE has been proved to detect and localise fatigue cracks as part of PN 33526. Therefore a successful detection and localisation of crack is expected. GW shear transducers will be used in this stage as these are more suitable for sizing cracks. UT scans will be carried out to validate results from AE and GW. In addition, FFS will also be carried out in order to inform about the integrity of the pipe.
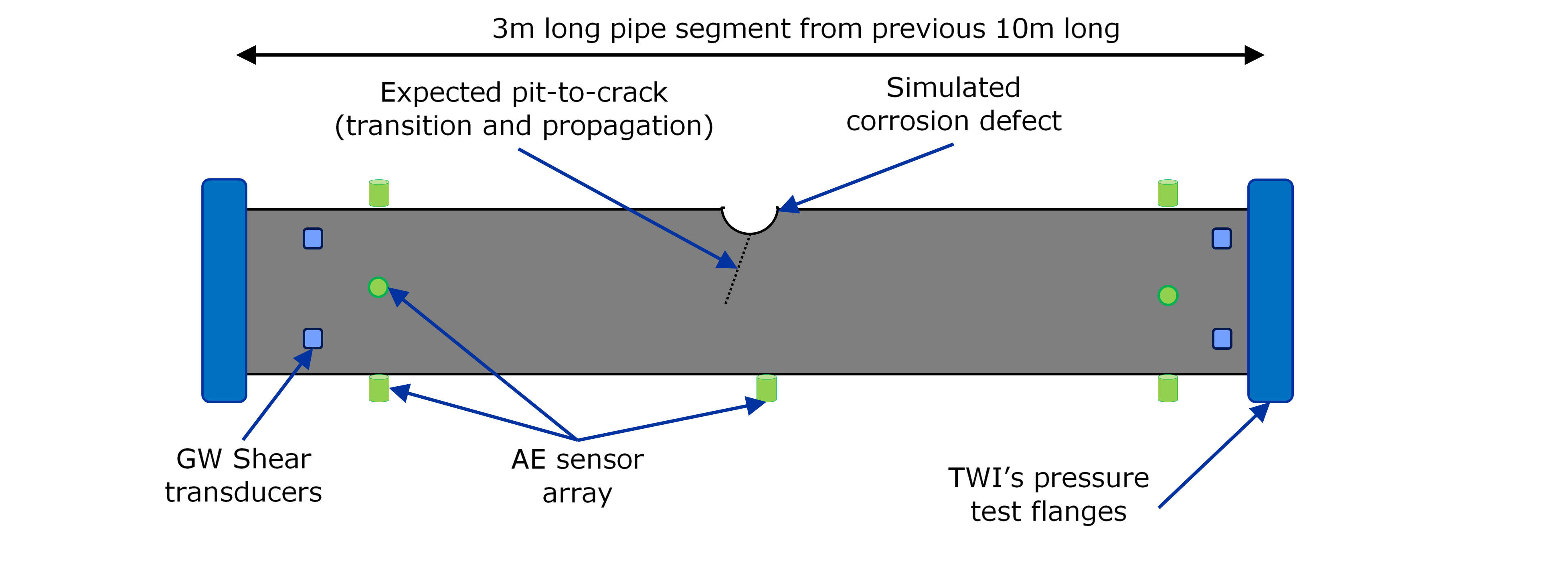
Figure 2 Pressure test of 3m long pipe with AE & GW monitoring.
The objective of this stage is to assess the accuracy of AE and GW to detect the pit-to-crack transition which is critical to pipeline operators. Three test are proposed and, if successful, an AE alarm will be derived to inform the detection of this stage.
Based on FFS results and confirmed crack lengths by UT, the test will be carried out until failure in order to record the full damage progression with AE and GW. Having AE and GW data of the ultimate stages of the pipe life-cycle will be beneficial for field monitoring pipelines at this critical stage.
Industry Sectors
Nuclear Power
Oil and Gas
Benefits to Industry
- The development of a dual sensing SHM technology based on AE and GW for Structural Health Monitoring of pipelines.
- Fusion of dual sensing SHM technology with advanced NDT technology, such as phased array ultrasonics to offer continuous and calibrated monitoring of pipeline degradation.
- Pipeline monitoring technology for use in high radiation and high temperature environments.
- Improved monitoring of existing pipelines re-purposed for use in CO2 and hydrogen transportation as part of carbon capture, utilisation and sequestration and the hydrogen economy.
- Improved SHM and NDT data analysis for input to future digital twins of pipelines for their lifetime integrity management.
- Possible further development of the technology into other applications such as wind turbine towers and blades, rails and structural I-beams for bridges and cranes.