Fusion welding is a process that uses heat to join or fuse two or more materials by heating them to melting point. The process may or may not require the use a filler material. External application of pressure is not required for fusion welding processes, except for resistance welding, where substantial contact pressure is required during welding for sound joining.
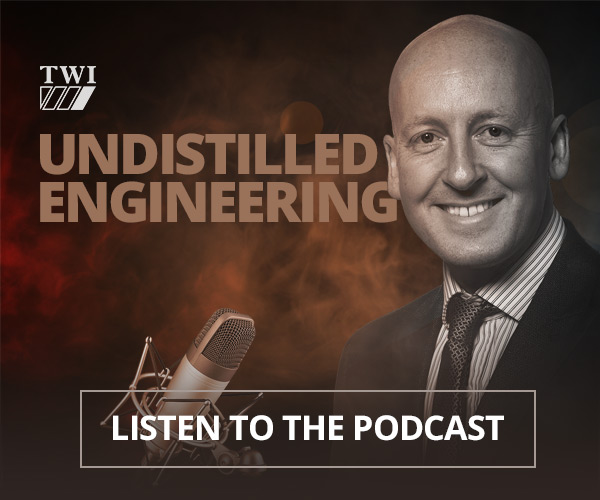
Fusion Welding Processes
Fusion welding processes can be grouped according to the source of the heat, for example, electric arc, gas, electrical resistance and high energy.
These processes include:
Arc Welding Processes - with the most common processes being:
Shielded Metal Arc Welding (SMAW), also known as manual metal arc welding (MMA or MMAW), flux shielded arc welding or stick welding. Suitable for welding ferrous and non-ferrous materials in all positions.
Metal Inert Gas Welding (MIG) and Metal Active Gas Welding (MAG), also known as Gas Metal Arc Welding (GMAW). MIG and MAG welding are the most common arc welding processes, in which an electric arc forms between a consumable wire electrode and the workpiece leading them to melt and join. Both use a shielding gas to protect the weld from airborne contaminants, or oxidation in the case of MIG welding.
Tungsten Inert Gas Welding (TIG), also known as Gas Tungsten Arc Welding (GTAW). This arc process uses a non-consumable tungsten electrode to create the arc between the electrode and the base plate. An inert shielding gas is used to protect from oxidation or other atmospheric contamination. This process can be used autogenously on thin parts, but will require the addition of a wire, rod, or consumable to be added for thicker parts.
Plasma Arc Welding (PAW). This process uses an electric arc created between an electrode and the torch nozzle. The electric arc ionises the gas (usually argon) in the chamber creating what is called a 'plasma.' It is then forced through a fine bore copper nozzle that constricts the arc and directs it to the workpiece, allowing the plasma arc to be separated from the shielding gas (which is usually made from a mixture of argon and hydrogen).
Submerged Arc Welding (SAW). This frequently-used arc welding process uses a continuously-fed consumable electrode and a blanket of fusible flux which becomes conductive when molten and provides a current path between the workpiece and the electrode. The flux also prevents spatter and sparks while suppressing ultraviolet radiation and fumes.
Flux Cored Arc Welding (FCAW). Developed as an alternative to SMAW, this process uses a continuously fed consumable electrode with a flux and a constant voltage or constant current power supply. Sometimes using a shielding gas this process can also just use the flux to provide protection from the atmosphere.
Learn more
Gas Welding Processes - the most common process being:
Oxy-Fuel Welding, also known as Oxyacetylene Welding but commonly called gas welding, this process uses a hand-held torch or blow pipe and a mixture of oxygen and acetylene which combusts to create a flame.
Resistance Welding Processes
Resistance Spot Welding. This fast welding process delivers heat between two electrodes according to the material properties and thickness of the workpieces. The welding current is concentrated to a small spot as the workpieces are simultaneously clamped together.
Resistance Seam Welding. This variant of spot welding produces a series of overlapping nuggets of a continuous joint by replacing conventional spot welding electrodes with wheels which rotate as the workpieces are fed between them.
High Energy Welding Processes - with the main ones being:
Electron Beam Welding (EBW). This fusion process is performed under vacuum conditions, using a beam of high velocity electrons to melt the workpieces as the electrons generate heat upon penetration into the material. Welds are often deep and narrow.
Laser Beam Welding (LBW). Often used in high volume applications, LBW uses a laser beam to provide a concentrated heat source with high levels of accuracy which can be used to join metal and polymers.