Destructive testing is undertaken in order to understand a specimen’s performance or material behaviour, these procedures are carried out to the test specimen’s failure. Destructive testing procedures can either follow specific standards or can be tailored to reproduce set service conditions.
Destructive testing methods are commonly used for materials characterisation, fabrication validation, failure investigation, and can form a key part of engineering critical assessments, which also involves non-destructive testing (NDT) techniques such as digital radiography.
If you have any questions or need help, email us to get expert advice:
contactus@twi.co.uk
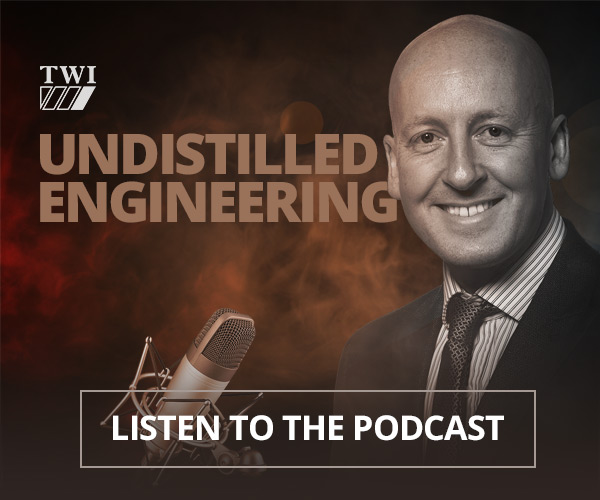
Types of Destructive Testing
Aggressive Environment Testing
This includes fracture and fatigue testing in sour (H2S), sweet (CO2) and other corrosive environments; at a range of temperatures and pressures. These test allow industry to assess the impact of these conditions on materials and performance.
Corrosion Testing
This covers non-toxic, small-scale, aqueous corrosion testing in a variety of different environments including fresh and sea water.
Fracture and Mechanical Testing
This includes different types of destructive testing methods such as tension tests, bend tests, Charpy impact tests, Pellini drop weight testing, peel tests, crush testing, pressure and fracture testing. As well as the testing of metals, fracture and mechanical tests can be carried out on different materials, such as welded polymers including plastic pipes.
Fatigue Testing
Performed in air or seawater environments, these tests are used to test parent materials and the endurance of welded joints under constant or variable amplitude loading. This destructive testing method can also be used for fatigue crack growth testing of welds, base metals, and heat affected zones.
Hydrogen Testing
This type of testing covers materials that have a risk of corrosion from exposure to hydrogen. These tests can be carried out at a variety of different temperatures and strain rates.
Residual Stress Measurement
Residual stresses are those that remain in a solid material after the original causes of any stresses have been removed. These can be intentional, such as with the scratch-resistant glass on smartphones, or unintentional which can lead to premature failure of a structure. Measurement of residual stresses allows for designers and engineers to determine factors like near-surface and through-thickness residual stress distribution, which can be used in engineering critical assessments.
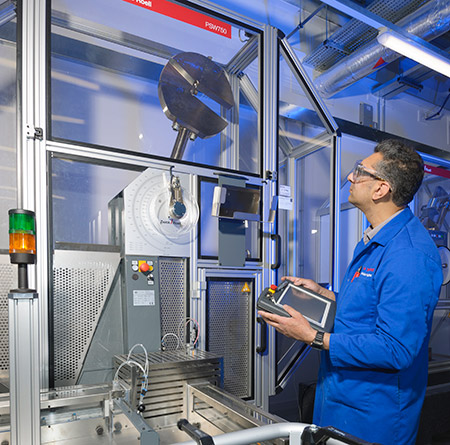
Charpy Impact Testing at The Test House