Near net shape (NNS) manufacturing is a term given to processes that aim for the initial fabrication of a component to be close in size and shape to the finished product. This approach reduces production costs and times associated with subsequent finishing steps, such as machining, and initial raw material investment costs. Near net shape manufacturing is particularly appealing for components manufactured with high-value materials, such as titanium alloys.
Near net shape manufacturing techniques are associated with lean manufacturing methods, as the core focus is to reduce waste involved with producing the final shape.
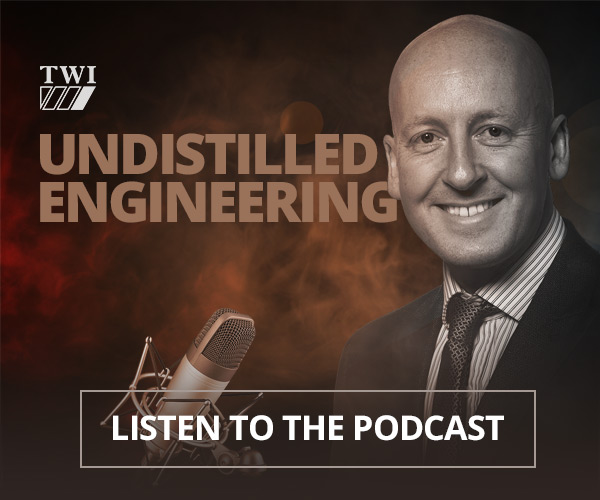
There numerous processes that fall under the category of NNS manufacturing, including:
The advantages most associated with NNS manufacturing include:
- Reduced material usage (saving on procurement costs)
- Reduced waste material (saving on recycle and waste disposal costs)
- Reduced finishing steps (saving on production time and costs, and reducing ‘wear and tear’ on machining equipment)
How Can TWI Help?
TWI has a long history of working with its Members, across a range of industry sectors, on near net shape manufacturing technologies. Discussed below are examples of these collaborations.
TWI collaborated with an industrial consortium on the application of linear friction welding (LFW) for the efficient manufacture of aerospace components. Rising material costs and the growing use of difficult-to-machine materials are spurring on designers to explore alternative, cheaper production methods. The TiFab project showed how LFW can be used to boost production of aerospace-quality near-net-shape titanium alloy components for the airframe sector.
TWI recently completed a three year partnership with CAV Advanced Technologies (AT), Leonardo MW and TISICS Titanium Composites, along with the MTC, and the NITC at Queen’s University, Belfast, for the Innovate UK ‘OLIVER’ project.
The OLIVER project has, through a series of case studies supported by IPG Photonics, helped these aerospace supply chain companies to develop their understanding of how laser welding can fabricate new, lightweight, near-net-shape, titanium (Ti) alloy and titanium metal matrix composite (Ti-MMC) assemblies.
TWI collaborated with BAE Systems and the Ministry of Defence on a project to identify an alternative to high strength steel castings in the manufacture of safety-critical hull penetrating valves. This collaboration came up with the concept of employing the electron beam (EB) process to fabricate the valve components and developed the procedure for manufacture.