Residual stresses are those stresses that remain in an object (in particular, in a welded component) even in the absence of external loading or thermal gradients. In some cases, residual stresses result in significant plastic deformation, leading to warping and distortion of an object. In others, they affect susceptibility to fracture and fatigue.
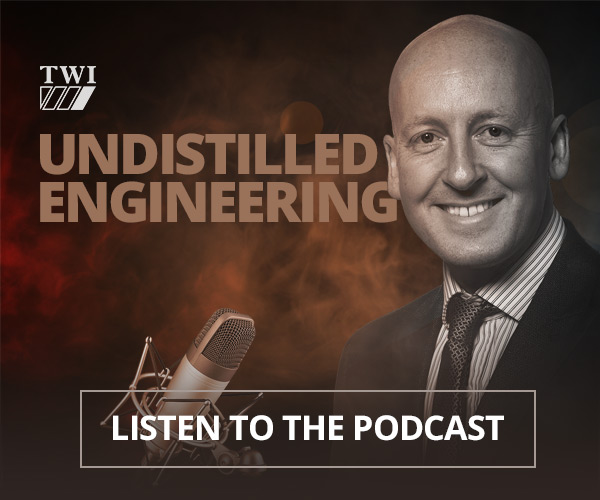
Contents
Residual stresses are generated when an object (especially a welded component) is stressed beyond its elastic limit, resulting in plastic deformation. There are three primary reasons for these stresses arising:
Thermal Variations
When an object is cooled from a high temperature (eg after welding), there is often a large difference in the rate of cooling throughout the body. The difference in cooling rates experienced by the surface and interior of the object results in localised variations in thermal contraction. The differing thermal contractions develop non-uniform stresses. During cooling, the surface cools at a quicker rate, compressing the heated material at the centre. As the material in the centre tries to cool, it is constrained by the cooler outer material. Consequently, the inner portion will have a residual tensile stress and the outer portion of the component will have a residual compressive stress.
Phase Transformations
When a material undergoes a phase transformation, a volume difference between the newly formed phase and the surrounding material, which has yet to undergo phase transformation, occurs. The volume difference causes expansion or contraction of the material, resulting in residual stress.
Mechanical Processing
Residual stress also occurs when plastic deformation is non-uniform through the cross-section of an object undergoing a manufacturing process, such as bending, drawing, extruding and rolling. When a material undergoes deformation, one part is elastic and another plastic. Once the load is removed, the material tries to recover the elastic part of the deformation, but is inhibited from full recovery due to the adjacent plastically deformed material.
Depending on the application, residual stresses can be positive or negative. For example, residual stresses are implemented in the designs of certain applications for positive effects. This can be achieved through laser peening, which imparts compressive residual stresses to the surface of an object, allowing for the strengthening of thin sections or the toughening of brittle surfaces.
Typically, however, residual stresses have negative effects. Residual stresses are often invisible to a manufacturer, unless they result in significant distortion, but can negatively affect structural integrity. For example, thick-walled structures in the as-welded condition are more prone to brittle fracture than a structure that has been stress-relieved.
The undesired stresses also have an effect on the fatigue performance.
It has long been recognised that, for non-welded materials under fatigue loading conditions, only the tensile parts of the applied stress cycle contribute to fatigue crack growth (see the lower part of Figure 1.) Conversely, for joints in the as-welded condition, the effects of welding residual stress need to be added to those of applied cyclic stress, with the result that the whole fatigue cycle (tensile and compressive) gives rise to fatigue damage (see the upper part of Figure 1).
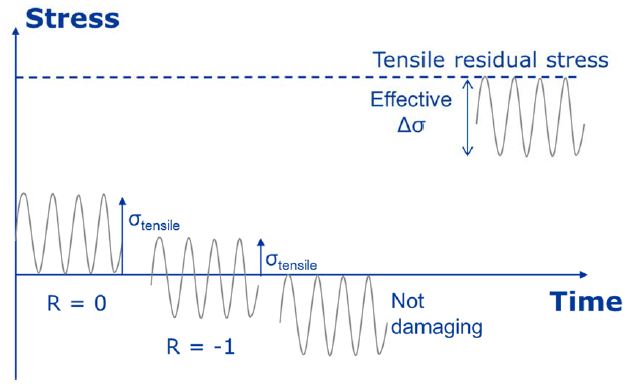
Figure 1 Effect of welding residual stress on fatigue damage.
Fortunately, the effects of welding residual stresses on both fracture and fatigue have been written into codes and standards in such a way that most users are unaware of them, and do not need to consider them explicitly. Nevertheless, there are particular cases where quantification of residual stresses is necessary.
There are many techniques used to measure residual stresses. These are broadly categorised into three areas: Destructive, semi-destructive and non-destructive. The approach to be used is often dependent on the information required. Owing to the complexity of some of the measurement techniques, the measurement must be performed in a specialised facility. This is particularly true for many non-destructive techniques.
The three primary categories are listed below:
Destructive
These techniques involve destruction of the object being measured and are typically used from a research and development perspective. Destructive testing is often far cheaper to implement than non-destructive testing.
Examples techniques include:
- Contour method. The contour method determines residual stress by cutting an object into two pieces and measuring surface height maps along the free plane created by the cut. The average contour determines the deformations caused by residual stress redistribution and is used to compute residual stresses through an elastic finite element model of the specimen. The result is a 2‐D map of residual stress normal to the measurement plane.
- Slitting. The slitting method is a technique for measuring through thickness residual stress normal to a plane cut through an object. It involves cutting a thin slit in increments of depth through the thickness of the workpiece and measuring the resulting deformations as a function of slit depth. The residual stress is then calculated as a function of through thickness position determined by solving an inverse problem using measured deformations.
Semi-destructive
Semi-destructive techniques are comparable to destructive techniques in that they use a strain release principle to determine the residual stress. However, only a small amount of material is removed, allowing the structure to better maintain its integrity.
Examples include:
- Deep hole drilling. Deep hole drilling involves drilling of a hole through the thickness of an object, measuring the diameter of the hole, cutting a circular slot around the hole to remove a core of material from around the hole and then re-measuring the hole diameter. The residual stress is determined from the geometric change.
- Centre hole drilling. Centre hole drilling works on the principle of drilling a small hole into an object. When the material containing residual stress is removed the remaining material reaches a new equilibrium state, which has associated deformations around the hole. The deformations around the hole are measured during the analysis using strain gauges or optical methods. The original residual stress in the material is calculated from the measured deformations.
Non-destructive
There are numerous techniques used for non-destructive testing which involve measuring the effects of relationships between the residual stresses and their material changes in the crystal lattice spacing.
Examples of non-destructive techniques include:
- Neutron diffraction. Uses neutrons to measure the crystal lattice spacing in an object. The neutrons exiting the object have comparable energy to the incident neutrons, allowing the residual stress to be determined from the lattice spacing.
- Synchrotron X-ray diffraction. Requires a synchrotron to accelerate the electromagnetic radiation to allow a through thickness understanding of an objects lattice spacing. The process uses a similar approach to neutron diffraction to calculate the residual stress.
- X-ray diffraction. This process allows for surface residual stress measurement, as the x-ray only penetrates the object surface by a few hundred microns.
There is a range of techniques that can be used to redistribute or relieve residual stresses. Appropriate manufacturing design and selection of welding parameters can reduce residual stress formation. For example, welding processing techniques that reduce the thermal gradient within an object will reduce the magnitude stresses generated.
Subsequent to a manufacturing process, additional steps can be taken to drastically reduce residual stresses contained within an object. This can be achieved via thermal or mechanical processing. Post-weld heat-treatments are often used to relieve or redistribute the residual stresses in a welded object. From a mechanical perspective, techniques such as shot peening, cold rolling, and stretching can be applied to achieve the desired effect.
How can TWI Help?
TWI currently provides a number of services to its Members in relation to process induced residual stresses, including:
- Measurement
- Numerical modelling
- Advice on:
The impact of residual stresses on structural integrity (primarily fracture and fatigue)
Residual stress mitigation methods (e.g. post-weld heat-treatment, peening etc)
Distortion control
In addition, several past and present NSIRC projects address measurement, modelling or interpretation of various aspects of welding residual stresses.
Residual stress expertise at TWI therefore covers the entire Technology Readiness Level (TRL) spectrum, from university-affiliated research and development through to on-site application of residual mitigation measures.
TWI has a long history of working with its Members to overcome the challenges associated with residual stresses. Please contact us to learn more.
contactus@twi.co.uk