Friction stir welding (FSW) is a solid state joining process invented by TWI in 1991. The range of materials that can be joined using FSW is continuously expanding.
TWI has been working on the development of FSW for joining titanium alloys since 1995. Titanium alloys present a particular challenge for conventional FSW process because they have a high softening temperature and low thermal conductivity. This means that it is difficult to generate sufficient heat to soften the material at the root (near the probe tip) without causing local overheating of the weld face under the shoulder. A significant breakthrough in this area came via the development of a variant of the FSW process called Stationary Shoulder FSW (SS-FSW as illustrated in Figure 1a) in 2004.
In SS-FSW, the probe rotates and protrudes through a hole in a stationary shoulder. The stationary shoulder adds no heat to the weld face so all of the heat is provided by the probe and the weld is made with an essentially linear heat input profile. Butt welding trials with the SS-FSW process on 6.35mm thickness Ti-6Al-4V plates produced very smooth, almost polished, weld cap with no underfill in cross-section as shown in Figure 1b.
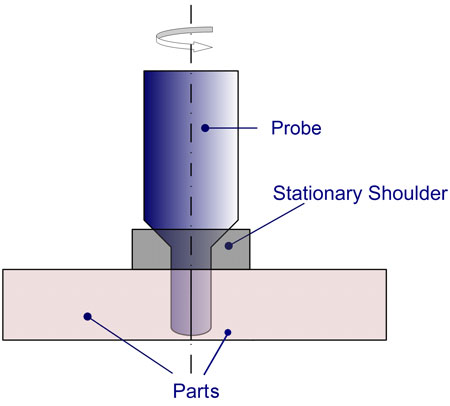
a) Schematic showing the principle of SS-FSW
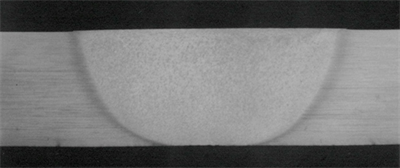
b) Macroscopic cross-section
Figure 1:
a) SS-FSW principle;
b) Typical weld cross-section in 6.35mm Ti-6Al-4V alloy.
In 2016, TWI successfully produced a Ti-6Al-4V launch vehicle propellant tank for the European Space Agency (ESA) by joining thin section parts (<3mm) using SS-FSW. The most recent development was a near net T-joint demonstrator fabricated from two (>10mm) Ti-6Al-4V plates. The details can be found via the links below: