Stress Corrosion Cracking of Ferritic Steel Weld Metal - the Effect of Nickel.
Part 1 - Introduction and experimental
Paper published in Metal Construction, vol.14., no.1, Jan 1982, p29-33.
T G Gooch reports a study of the effect of nickel on the stress corrosion cracking behaviour of weld metals appropriate to structural and pipeline steels. Tests were carried out using nickel-free and nickel containing electrodes, and electrodes without nickel but containing 1.6%Mn. Stress corrosion testing was undertaken on butt welds in the as-welded condition in simulated seawater with cathodic protection or containing c. 100ppm H2S, and under H 2S saturated NACE conditions. As discussed in Part 2 Nickel was not found to have any major effect either on stress corrosion cracking resistance in the various test media or on hydrogen pick-up rate.
T. G. Gooch, BSc, MSc (Eng), PhD, CEng, FIM, FWeldl, DIC, Head of the Materials Department of The Welding Institute, Abington.
Nature of the problem
It is widely recognised that transformable ferritic steels are potentially susceptible to hydrogen-induced stress corrosion cracking (SCC) in a range of environmental conditions, the hydrogen being formed by a cathodic corrosion reaction. [1] The risk of cracking depends inter alia on the amount of hydrogen liberated and entering the steel, and the problem becomes particularly acute in 'sour' media where hydrogen sulphide is present, [1] apparently because the formation of a sulphide scale on the metal surface inhibits the hydrogen atom combination reaction and thus promotes rapid and severe hydrogen ingress into the steel. As would be expected from a hydrogen embrittlement phenomenon, material susceptibility increases with increasing hardness and strength level, and hence control of the problem in practice is based largely on the avoidance of unacceptably hard microstructures. In sour media, a limiting hardness of Rockwell C22 (HV243*) is applied on this basis. [2]
Over and above the effect of hardness, it has been reported that the presence of nickel as an alloying element in steel promotes increased susceptibility to cracking [3] , and specifications have been issued [2] debarring this element from material for service in sour conditions. At the same time, as the section sizes of ferritic steel constructions increase and as more demanding toughness requirements are imposed, it can be difficult to obtain acceptable weld metal toughness unless the weld deposit contains a small amount of nickel. Where both high weld metal toughness and good stress corrosion resistance are required, it has therefore been uncertain whether or not nickel additions can be safely employed.
Background
Virtually all studies aimed at elucidating the role of nickel have been based on tests in sour media, mainly following the NACE test solution of 3%NaCl+0.5% acetic acid, saturated with H2S. [4] To a large extent, concern over the possible effect of nickel stems from work by Treseder and Swanson [3] on the effect of composition and hardness on susceptibility to SCC in such sour conditions. It was found that a number of wrought alloys containing nickel showed appreciable sensitivity to cracking, even at hardnesses below Rockwell C22 (HV243), and this was the case also in a later investigation by Burns. [5] In contrast, early findings by Snape [6,7] identified an effect of microstructure and hardness on SCC sensitivity, but not one of nickel over the range 0-3%Ni, and it may be noted that Snape's work [7] included study of materials apparently derived from split heats and differing compositionally only in nickel content. Snape suggested [8] that the nickel-bearing materials examined by Treseder and Swanson had been tempered at above Acl (nickel having the effect of reducing the Acl), so that the samples tested contained small amounts of untempered martensite which could markedly raise SCC susceptibility. This was disputed by Treseder and Swanson on the basis that they did not observe such untempered martensite on optical metallographic examination of their specimens.
Kowaka and Nagata [9] found cracking in nickel-free steel at below Rockwell C22 (HV243) hardness, but concluded that nickel had an adverse effect, at least in the hardness range HRC 19-29 (HV225-285), as did manganese and copper, although to a lesser extent. Work by Fraser and Eldredge [10] also indicated that nickel reduced SCC resistance, but again other elements had a similar effect, molybdenum apparently being particularly adverse. Alloying must in general be expected to promote SCC susceptibility, since material hardness will tend to be increased, as a result both of solid solution effects and from the formation of harder transformed structures. In this respect, the results of Keller and Cameron [11] show no difference in susceptibility between AISI 4140 (nickel-free) and 4130 (nickel-containing steels) tempered to the same strength level, although relatively few tests were carried out.
Turning to weld metals, Watanabe and Mukai [12] concluded that nickel reduced SCC resistance in tests on consumables for structural steel applications in sour media. However, the electrodes studied varied in respect of elements other than nickel, rendering it difficult to draw distinction between the effects of individual alloying elements, while, from the stress/failure time data reported, it is questionable whether a threshold stress was adequately defined in all cases. A similar conclusion to Watanabe and Mukai's was drawn by Kihara et al [13] yet Nakayama et al who also studied [14] structural steel weld metals in sour media, demonstrated that, for constant welding conditions, all the alloying elements Cr, Si, Mo and Ni had an adverse effect, as might be expected since each would tend to increase deposit hardness as noted above.
From trials under NACE conditions on both weld metal and parent steels, Schmid [15] found no correlation between nickel level and SCC behaviour. The materials employed varied considerably in composition, but the results obtained certainly indicated that nickel did not have an overriding effect on susceptibility to cracking. In addition, it may be noted that virtually nickel-free weld metal (0.06%Ni) showed SCC at only Rockwell B87 (HV173), i.e. well below the Rockwell C22 (HV243) level.
The above investigations essentially examined the influence of nickel by direct SCC testing. Okada et al [16] studied hydrogen pickup under sour conditions and concluded that nickel enhanced the rate of hydrogen ingress into wrought steel. However, the two materials studied varied in elements other than nickel, and, in particular, the lower nickel material was also of somewhat higher copper content and it is well established [17,18] that copper can reduce hydrogen pickup in sour media. At the same time, the possibility that nickel promotes SCC by increasing hydrogen pickup rate cannot be discounted, since Yukawa et al [19] showed that, at least with high nickel levels ( c. 9%Ni), the corrosion rate in sour media is increased, with more rapid formation of a sulphide scale.
Work by Dunlop [20] on nickel steels for low temperature service is noteworthy in several respects. Susceptibility was found at hardness levels well below Rockwell C22 (HV243) with an apparently much lower threshold stress than obtained by Schmid [15] working on the same material grade. Moreover, no cracking occurred in sour conditions with cathodic protection applied, and Dunlop therefore concluded that the role of nickel was to change the failure mechanism from one of hydrogen embrittlement to one of 'active path' cracking. However, Dunlop did not study nickel-free materials, and it is possible that the absence of cracking with cathodic protection was due, not to a change in failure mechanism, but to the cathodic polarisation preventing the formation of a sulphide scale on the steel surface, with an associated reduction in hydrogen pick-up rate.
The question of whether SCC of ferritic steels develops by hydrogen embrittlement or an active path has been most widely debated in respect of high strength steels in marine conditions [21,22] and it is now generally considered that failure in fact results from hydrogen embrittlement. [22,23] Whatever the mechanism, a parallel may be drawn with cracking in sour conditions, and if nickel had an adverse effect on intrinsic SCC resistance, it might be expected that this would be apparent from comparative evaluation studies on high strength steels. No such trend is evident from available data, [23,24] and, for a range of strength level, similar SCC resistance can be obtained with nickel-free and nickel-containing alloys, although some propensity for increased pitting may be associated with very high nickel grades ( e.g. 18%Ni maraging steels) which could facilitate SCC initiation in service. [23] In terms of high alloy steels, it may also be noted that Kane et al [25] found the 13%Cr/4%Ni CA6NM grade to exhibit higher SCC resistance in sour media than the nickel-free 13%Cr CA15 or AISI 410 materials.
Overall, although a number of investigators have indicated that nickel has a singular effect in reducing SCC resistance, this has not been established unambiguously. With the possible exception of studies by Snape, [6] elements other than nickel have been varying in the different test programmes (and this is certainly true for weld metal investigations), rendering it difficult to assess the role of nickel in isolation, while cracking at low hardness levels cannot be ascribed solely to the presence of nickel.
Present investigation
Since the role of nickel on SCC resistance has not been positively established, and in view of the benefits of this element in terms of weld metal toughness, the present investigation was initiated to examine the influence of nickel on the SCC behaviour of weld metals appropriate to carbon manganese structural steel fabrications. The most widespread practical concern regarding hydrogen-induced SCC arises in respect of two types of service, namely, ( i) under marine conditions with cathodic protection applied; and ( ii) in sour media. The present investigation has studied the role of nickel under such environmental regimes, with, in the latter case, attention being paid both to the NACE test as representing a severe standard laboratory test, and to conditions simulating the practical seawater environment with low H2S levels as might arise from the decay of organic matter. [26]
Three consumable types were employed, viz: a nickel-containing example (AWS E8018 Cl type), a nickel-free consumable for structural steel applications (AWS E7018 type) and a nickel-free electrode alloyed with increased manganese (c. 1.6%) to give a similar strength to that of the 8018 Cl consumable. Parent material to BS 4360 Grade 50D was used as a representative structural steel, and comparative studies were carried out on weld heat affected zones (HAZs) of low and high hardness.
Experimental
General approach
From the above considerations, the experimental programme was based on the use of three environmental conditions, viz:
- simulated seawater with cathodic protection
- standard NACE solution, i.e. 3% sodium chloride with 0.5% acetic acid, saturated with H2S
- simulated sea water with c. 100ppm H2S.
In respect of the first and third of these, the work involved pre-cracked samples, both as reproducing the severe practical situation of a pre-existing defect, and to enable the results to be assessed using linear elastic fracture mechanics principles. Moreover, the method enabled individual sampling of weld metal and HAZs of test welds. Studies in the second environment employed tensile samples, following the NACE standard procedure. [4] Initially, the tensile tests were carried out using transverse weld samples so that the relative susceptibilities of all areas of a weld could be gauged in a single specimen. In the event, preferential parent material failure was noted, and subsequent tests were based on the use of all weld metal tensile samples.
Material susceptibility was assessed primarily on the basis of 'threshold' stress or stress intensity levels as appropriate. In addition, the effect of nickel on hydrogen pick-up rate was examined by exposing small samples to the different test media with subsequent hydrogen analysis.
Materials
Parent material
The particular heat of BS 4360 Grade 50D employed was selected as having a carbon equivalent (CE) level high enough for both 'hard' and 'soft' HAZ microstructures to be obtained in the test programme for comparative purposes. The material thickness was 25mm, and analysis is given in Table 1 with associated mechanical properties.
Welding electrodes
As indicated above, three consumable types were employed, viz:
- E7018
- E8018-C1
- 1.6%Mn
The consumables were manufactured and supplied by BOC Murex Ltd, and were based on a common core wire and basic flux formulation with nickel and manganese being added via the flux as necessary so that other elements would remain substantially constant. The electrodes were made on a laboratory scale to ensure consistency of coating formulation, but under conditions typical of normal industrial manufacturing practice. An electrode diameter of 4mm was employed throughout the programme, and deposited weld metal analyses are given in Table 2. The relative consumable compositions are essentially as required ( viz. elements other than nickel and manganese held constant), although it will be recognised that weld metal composition in the butt welds prepared as described below will vary to some extent, at least through the joint thickness, because of local variation in dilution.
Table 1. (a) Parent material analysis and (b) tensile properties
(a)
Composition, wt%
C | S | P | Si | Mn | Ni | Cr | Mo |
0.17 |
0.011 |
0.022 |
0.37 |
1.35 |
0.02 |
0.01 |
<0.01 |
V | Cu | Nb | Ti | Al | B | CE |
<0.01 |
0.01 |
0.031 |
<0.01 |
0.036 |
<0.001 |
0.40 |
CE=Carbon equivalent= |
 |
(TWI analysis ref. S78/261) |
Table 2 Weld metal analyses
Weld metal type | Composition, wt% |
C | S | P | Si | Mn | Ni | Cr | Mo | V |
(a) Pad samples |
7018 |
0.06 |
<0.005 |
0.013 |
0.16 |
0.94 |
0.03 |
0.03 |
<0.01 |
0.02 |
8018-C1 |
0.05 |
<0.005 |
0.013 |
0.19 |
1.02 |
2.17 |
0.03 |
<0.01 |
0.01 |
1.6%Mn |
0.06 |
<0.005 |
0.013 |
0.15 |
1.66 |
0.03 |
0.03 |
0.01 |
0.02 |
(b) Top runs of butt welds |
7018 |
0.06 |
0.005 |
0.014 |
0.22 |
1.08 |
0.03 |
0.03 |
0.01 |
0.02 |
8018-C1 |
0.06 |
<0.005 |
0.002 |
0.22 |
1.11 |
2.16 |
0.03 |
0.01 |
0.01 |
1.6%Mn |
0.06 |
0.005 |
0.015 |
0.21 |
1.80 |
0.04 |
0.04 |
0.01 |
0.02 |
Weld metal type | Composition, wt% |
Cu | Nb | Ti | Al | B | Pb | Sn | Co |
(a) Pad samples |
7018 |
0.02 |
0.005 |
0.01 |
0.007 |
<0.0005 |
<0.01 |
<0.01 |
0.02 |
8018-C1 |
0.02 |
0.006 |
0.02 |
0.008 |
<0.0005 |
<0.01 |
<0.01 |
0.02 |
1.6%Mn |
0.02 |
0.005 |
0.02 |
0.012 |
<0.0005 |
<0.01 |
<0.01 |
0.02 |
(b) Top runs of butt welds |
7018 |
0.02 |
0.008 |
0.02 |
0.009 |
<0.0005 |
<0.01 |
<0.01 |
0.03 |
8018-C1 |
0.02 |
0.008 |
0.02 |
0.009 |
<0.0005 |
<0.01 |
<0.01 |
0.02 |
1.6%Mn |
0.02 |
0.009 |
0.02 |
0.014 |
<0.0005 |
<0.01 |
<0.01 |
0.03 |
(TWI analysis ref. S79/520)
Test weld preparation
For evaluation of weld metal mechanical properties and SCC resistance, butt welds were prepared using the different consumables, with an asymmetric double V preparation as in BS 5135:1974, preparation (f). Following deposition of the root run, the welds were completed on the second side, with backgouging and filling on the first. All welding was carried out with a preheat of 100°C and an interpass temperature of 100-150°C.
For HAZ SCC studies a K preparation was employed with the vertical leg being buttered to give an overlay 5-10mm thick prior to joint completion. Current and travel speed were varied during buttering to achieve different HAZ hardness levels. Following buttering, joint completion was carried out as for the V-preparation test panels intended for weld metal assessment.
Welding conditions are given in Table 3. All welding was carried out in the flat position with DC electrode positive polarity, electrodes being baked for lhr at 450°C and stored at 150°C prior to use.
Table 3 Welding conditions
Sample type | Current, A | Voltage, V | Travel speed, mm/min | Arc energy, kJ/mm |
Double V butt welds |
150 |
22 |
210 |
0.9 |
K butt weld hard HAZ: Butter |
130 |
22 |
260 |
0.7 |
Fill |
150 |
22 |
250 |
0.8 |
K butt weld: soft HAZ: Butter |
185 |
22 |
210 |
1.2 |
Fill |
150 |
22 |
250 |
0.8 |
Weld metal Charpy V-notch samples were prepared and tested at -25°C and -45°C, with results as indicated in
Table 5. All electrodes comply with the requirements of the Department of Energy 'Guidance on the design and construction of offshore installations, 1971'.
Table 5 Charpy impact test results
Weld metal type | Test temperature °C* | Absorbed energy, J |
7018 |
-25 |
60, 50, 32 |
|
-45 |
40, 17, 26 |
8018-C1 |
-25 |
140, 138, 144 |
|
-45 |
85, 102, 36 |
1.6%Mn |
-25 |
52, 40, 70 |
|
-45 |
14, 50, 54 |
*Test temperatures of (a) -25°C and (b) -45°C were selected on the bases of:
(a) 'Guidance on the design and construction of offshore installations', Dept of Energy, 1977.
(b) AWS A5.1-78 and A5.5-69
Results of hardness measurements are shown in Tables 6 and 7.
Table 6 Hardness results from double V butt welds
Sample | 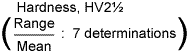 |
Parent material |

|
7018 test weld: Weld metal |
|
HAZ |
|
8018-C1 test weld: Weld metal |

|
HAZ |

|
1.6%Mn test weld: Weld metal |

|
HAZ |
|
b) NACE tensile test machine. Note that for studies in seawater with cathodic protection, neither the H2S inlet nor the water bath was employed: temperature control was obtained as necessary by circulating glycerine/glycol coolant through a coil in the test solution
Fig.2. Test configurations
Testing was carried out at +20°C and +4°C. No sample showed complete separation on SCC testing, and the remaining unfractured ligament was therefore broken following cooling to liquid nitrogen temperature for measurement of the total crack depth and calculation of the stress intensity both initially applied and corresponding to failure. For comparison, samples were also tested in air to determine the fracture toughness in the absence of a corrosive environment.
NACE testing
Cylindrical tensile test samples were machined as indicated in Fig.lb according to NACE requirements. In the first instance, samples were machined transverse to test welds made using each of the three consumable types employed. Constant load testing was carried out at +25°C under NACE conditions ( Fig.2b) with a range of applied loads, time to failure being recorded in each case. However, all specimens showed parent material failure and further tests were therefore carried out using all weld metal samples machined from pads deposited using welding conditions as above.
Low H2S studies
The aim was to assess SCC resistance in seawater containing about 100ppm H2S. For this purpose, testing was carried out with simulated seawater through which a commercial high purity 10%H2S/90%N2 mixture was passed. Despite this control of input gas composition and careful attention to flow rate and bath temperature, it proved impossible to maintain constant H2S level. The concentration of H2S was held generally between about 70 and 200ppm, but excursions from 50-280ppm were experienced. Similar variation in H2S level has been reported by other workers studying low H2S concentrations. [28]
Pre-cracked samples were prepared as described above, and stressed in three-point bend ( Fig.2a) in the test corrodant at +25°C under constant load for a period, followed by incremental loading. Because the effect of 100ppm H2S was not known, initial samples of 7018 and 8018-Cl weld metal were exposed under static load for 1200hr, this being in excess of the 720hr required for NACE tensile tests. The samples were then incrementally loaded to a value approaching the 'threshold' in the seawater tests with cathodic protection, and removed for examination. No evidence of SCC was found. Subsequent tests were carried out with shorter exposure periods.
Hydrogen determinations
Blocks 10x10x20mm were machined from the parent material and the test weld metals, and exposed to the above test media concurrently with SCC samples. Following exposure durations appropriate to each SCC condition they were removed, and stored in liquid nitrogen. They were then cleaned by shot blasting, and the hydrogen levels determined. Diffusible and residual levels were obtained, the former by collection over mercury at 25°C for 21 days and the latter by hot vacuum extraction. Control samples not exposed to the test media were also shot blasted and analogous hydrogen levels measured.
Metallographic examination
Transverse sections were prepared from the various test welds and examined under the optical microscope. Transverse and longitudinal sections were taken through NACE specimens for assessment of the location of cracking. Representative fracture faces were examined in the scanning electron microscope (SEM).
Part 2
References
- Uhlig H H: 'Corrosion and corrosion control'. Publ. John Wiley and Sons Inc, New York, 1963.
- NACE Standard, MR-01-75 (1980 revision).
- Treseder R S and Swanson T M: Corrosion 1968 24 (2) 31-37.
- NACE Standard, TM-01-77.
- Burns D S: Mat Perf 1976 15 (1) 21-28.
- Snape E: Corrosion 1967 23 (6) 154-172.
- Idem. Ibid 1968 24 (9) 261-282.
- Snape E: vide ref. 3.
- Kowaka M and Nagata S: Proc. 'Twelfth Japan Congress on Materials Research'. Soc. Mat. Sc. 1969, 141-145.
- Fraser J P and Eldredge G G: Corrosion 1958 14 (11) 44-50
- Keller H F and Cameron J A: Proc. 'Corrosion 74', NACE, Chicago, 1974.
- Watanabe M and Mukai Y: Osaka University Technical Reports, 1964 14 (602)
- Kihara M et al: Proc. 'Seventh World Petroleum Congress'. 1967, 235-260.
- Nakayama H et al: Welding World 1968 20 (11) 509-515.
- Schmid G C: Proc. 'Corrosion 79'. NACE, Atlanta, Georgia, 1979.
- Okada H et al: Proc Conf 'Stress corrosion and hydrogen embrittlement of iron-base alloys', Firminy, France, 1973, publ NACE, 1977.
- Moore E M and Warga J J: Mat Perf 1976 15 (6) 17-23.
- Inagaki H et al: Trans ISIJ 1978 18 149-156.
- Yukawa K et al: Corrosion Eng 1966 15 (10) 445-451.
- Dunlop A K: Corrosion 1978 34 (3) 88-96.
- Phelps E H and Loginow A W: Corrosion 1960 16 (7) 325t-335t.
- Barth C F, Steigerwald E A and Troiano A R: Corrosion 1969 25 (9) 353-358.
- Gooch T G: PhD Thesis, University of London, 1975.
- Judy R W Jr. and Goode R J: NRL Report, No. 6988, Nov. 1969.
- Kane R, Watkins M and Greer J B: Proc. 'Corrosion 76', NACE Houston, 1976.
- Efird K D and Lee T S: Corrosion 1979 35 (2) 79-83.
- Biefer G J and Garrison J G: Agard Conf Proc: No. 98, Paper 11, NATO, Brussels, 1971.
- Hudgins C M et al: Corrosion 1966 22 (8) 238-251.
- ASTM STP 381, 1965.
- Robinson J L: Welding Institute Research Bulletin 1977 18 (5) 121-126.
- Iino M: Met TransA 1978 (9a, Nov) 1581-1590.
- McDonald R D: Weld Res Abroad 1972 XVIII, June-July 23-34.
- Townsend H E: ASTM STP 518, 1972, 155-166.
- NACE Standard RP-04-72.
- Towers O L and Garwood S J: Proc 'Third Colloquium on Fracture,' London, Sept. 1980, 57-68.
- Tsuru S and Garwood S J: Proc Third Int Conf on 'Mechanical Behaviour of Materials,' Cambridge, Aug. 1979, 519-528.