P H M Hart
Paper presented at Vanadium 2001. Vanadium Application Technology. International Symposium, Beijing, China, 12-14 Oct 2001.
1 Introduction
The commencement of microalloyed steels was approximately half a century ago with the initial drivers of reducing material costs and increasing strength. Although improved weldability was not amongst these very first incentives forthe development of microalloyed steels the opportunities that microalloying gives for improving weldability by reducing carbon content was fairly quickly recognised and became another major driving force for their development andunderstanding. However, it was not until possibly the first major international conference on these steels, MA75, that a substantial public hearing of the topic occurred. In this paper the aim will be to focus attention on the currentinformation concerning weldability aspects related to vanadium-microalloyed steels for structural, pressure vessel and linepipe applications and will consider the relevant weldability aspects of solidification cracking, reheatcracking, hydrogen cracking during fabrication, HAZ hardening, and HAZ and weld metal toughness. In recent years vanadium additions have also been applied to the Cr-Mo steels for elevated temperature use, and this too will beconsidered. Finally some consideration will be given to the so-called 'vanadium effect' in promoting intragranular nucleation, particularly during welding, in C:Mn microalloyed steels.
2 Weldability topics
2.1 Solidification cracking
Past experience has certainly shown that in relation to arc welding the benefits that microalloying additions can bring to steel composition in terms of a reduction in carbon content, have been overwhelmingly beneficial. Asystematic study of the influence of compositional variables on solidification cracking was carried out some years ago by TWI [1] and the results incorporated into British and now European Standards for arc welding of ferritic steels. The work was done using submerged arc welding which usually involves considerable dilution of the parent steel andtherefore allowed compositional effects of parent steels to be evaluated. A formula was devised which relates crack susceptibility, in terms of units of crack susceptibility, (UCS) to the composition of the weld metal and is:
UCS = 230C+190S+75P+45Nb-12.3Si-5.4Mn-1.
The equation is valid for the following range of weld metal compositions 0.08-0.23%C, 0.010-0.050%S, 0.010-0.045%P, 0.15-0.65%Si, 0.45-1.6Mn, 0-0.07%Nb. It was concluded that the presence of up to 1%Ni, 0.5%Cr, 0.4%Mo, 0.07%V,0.3%Cu, 0.02%Ti, 0.03%Al, 0.002%B had no significant influence on the risk of cracking. One study [2] which examined the effect of vanadium by employing submerged arc welding of pipe containing 0.16%C and 1.4%Mn, showed that vanadium additions apparently reduced the risk of solidification cracking.
While solidification cracking in arc welds is nowadays uncommon, principally because of the lowered C & S levels, as a weldability problem it has reappeared in high speed beam welds, particularly laser welds. It would beinteresting to see if the reported beneficial effect of vanadium in submerged arc welding of pipe also applies to laser welding, which is now being considered for pipe welding.
2.2 Reheat cracking
Reheat, or stress relief, cracking is generally limited to low alloys steels containing at least two of the elements Cr, Mo, V and B. However, as the problem is limited to a few steels there has been little attempt to developuniversal formulae for this type of cracking. Two examples of formulae that have been used are:
i) ΔG = Cr+3.3Mo+8.1V [3]
where ΔG<0 indicates low susceptibility and
ii) P SR = Cr+Cu+2Mo+10V+7Nb+5Ti-2 [4]
when P SR<0 indicates low susceptibility
As the cracking is intergranular, other elements, which influence temper embrittlement can also affect the risk of cracking and so the problem is not solely related to the level of alloying elements present. Certainly with respectto structural steels, the tendency to avoid postweld heat treatment, means that this is a rare and decreasing problem.
2.3 HAZ hydrogen cracking
2.3.1 C:Mn steels
During the early days of development of microalloyed steels, HAZ hydrogen cracking was a significant weldability problem, not least because carbon levels were still relatively high and hydrogen levels from many consumables, eitheras-received, or because of poor storage and handling, were also relatively high. Both of these influencing factors, particularly in the last 10-15 years have beneficially improved, as carbon levels of steels have continued to fall andhydrogen levels in welds significantly reduced as a result of improvements in consumables. The risk of the problem occurring, is still however, related to the risk of producing hardened predominantly martensitic microstructures in theheat affected zone and material sensitivity to the problem is still generally assessed by a compositional characterising parameter generally referred to as a carbon equivalent formula. These parameters are often linked into methods fordevising minimum preheat to avoid the problem. The most comprehensive of these schemes today are probably those used (i) in Britain, [5,6] devised by TWI, (ii) in Japan often referred to as the CEN method, [7] (iii) that incorporated within AWS D1.1 and (iv) the more recent method originating within Germany. [8] These use the following compositional characterising parameters.
Most of these show vanadium to have some small adverse effect on the risk of HAZ hydrogen cracking, although it is interesting to note that the more recent German study which applies to steels up to 0.18%V did not find it necessary to include this element in the compositional characterising parameter. The study by Hart and Harrison [9] in the '80s, on a series of experimentally produced carbon manganese nickel vanadium molybdenum steels, found that the critical cooling time for the avoidance of HAZ cracking could be related to the steel composition by the expression:
The risk of cracking characterised in this expression is a summation of two separate factors. One is the hardenability of the steel, which describes the risk of forming hardened and susceptible microstructures, the other is the inherent susceptibility of the hardened microstructures often expressed as the critical hardness for cracking. Hart and Harrison found that the influence of vanadium was of a different sign in respect of these two factors. For hardnesses around the critical hardness level for that study (~350HV) vanadium had a decreasing effect on steel harden ability (see next section), which by itself would lead to a reduction in risk of cracking.
However this was offset by the finding that the critical hardness was decreased (ie susceptibility increased) by vanadium, as indicated by the equation:
In subsequent regression analysis of a much larger database of C:Mn type steels, many microalloyed with Nb, Hart et al, [10] produced a similar equation for the compositional characterising parameter:
As discussed by Hart et al since the critical microstructures for cracking tend to be martensitic, the strong dependency of HV crit on carbon is not surprising. Moreover they noted that there were several studies which have shown that the final contraction stress, when a weld cools out, is related to the steel composition, being lower forsteels with lower transformation temperatures. Given that, the trend for HV crit to reduce with increasing C, and CE levels, is also not surprising.
In considering the cracking risk of a particular element its effect should be viewed in respect of the increase of likely alloying levels, and since much steel development is against a specific strength level, comparison should be made on alternative alloying to produce the same strength level. Hart and Harrison [9] showed that compared to manganese, albeit in normalised steel, a given strength increase could be achieved for a smaller increased risk of cracking by using V rather than Mn alloying.
2.3.2 Low alloy steels
Particularly in the Cr-Mo steels for elevated temperature service, vanadium additions have been quite prominent in steel development e.g. modified 9Cr1Mo steels, so called P91, the vanadium modified 2.25Cr1MoV steels and the3CrMoVTiB steels. Being more recent developments less work has been carried out on the effect of vanadium although for P91 type compositions Panton-Kent [11] has shown that the risk of weld metal hydrogen cracking is no higher than for the straight 9Cr1Mo composition. For the 2¼Cr1Mo type steels there is data [12] to suggest that V-additions may have distinct benefits as far as hydrogen embrittlement in service are concerned, and this seems to be linked to greater trapping and lower diffusivities in the V-modified steels. Indeed other work [13] has indicated that the problem of disbonding at cladding interfaces can be reduced in V-modified steels. The possible consequence of a reduced hydrogen diffusivity on welding procedures for fabricating v-modified Cr-Mo steels, in particular the application of dehydrogenation heat treatments is the subject of a forthcoming joint industry project at TWI.
2.4 HAZ hardening behaviour
Clearly the influence of microalloying in HAZ hardening behaviour is of importance because of the role of this on the risk of HAZ hydrogen cracking as described above, although, this aspect has become of less importance because ofthe decreased risks of HAZ hydrogen cracking in general, also referred to above. However, HAZ hardening is also important, perhaps increasingly so, from the point of view of avoidance of environmental cracking and in particular that which is HAZ hardness related and specifically those types caused by hydrogen embrittlement either from cathodic protection or sulphide stress corrosion cracking. These forms of environmental cracking are prevented by controlling HAZ hardness to specified limits which for fully sour service will typically be 250HV max.
As well as looking at the risk of HAZ hydrogen cracking, the study by Hart and Harrison [9] also developed equations for prediction of HAZ hardness levels in the range 250-450HV. As can be seen from Table 1 this shows an interesting trend for the influence of vanadium. For the higher hardness levels of 325 HV and above, which will tend to be associated with the more rapid cooling conditions and therefore shorter thermalcycles, it can be seen that vanadium reduces the hardenability, while for the softer microstructures of 300 down to 250HV the influence of vanadium was of an increasingly positive effect. This change in sign of coefficient for vanadiumis not apparent from other work examining HAZ hardness, for example that of Suzuki [14] , Yurioka [15] and Duren [16] but this may be because of their lower levels of vanadium studied and the fact that they did not develop expressions for each specific hardness level.
Table 1 Linear regression equations for predicting cooling times ( Δt 800*-500℃/s)
Equation of Mean Line | Compositional Characterising Parameter (CCP) |
1 |
Log Δt (250HV) = M (CCP 1) + K |
C + 0.1191Mn+0.3010V + 0.0828Ni+0.1777Mo 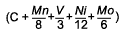 |
2 |
Log Δt (275HV) = M (CCP 2) + K |
C + 0.1032Mn + 0.2480V + 0.0700Ni + 0.1508Mo 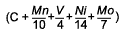 |
3 |
Log Δt (300HV) = M (CCP 3) + K |
C + 0.0828Mn + 0.0213V + 0.0362Ni + 0.1037Mo 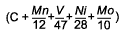 |
4 |
Log Δt (325HV) = M (CCP 4) + K |
C + 0.0641Mn - 0.0293V + 0.0136Ni + 0.0969Mo 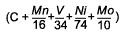 |
5 |
Log Δt (350HV) = M (CCP 5) + K |
C + 0.0485Mn - 0.0565V + 0.0047Ni + 0.0758Mo 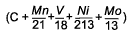 |
6 |
Log Δt (375HV) = M (CCP 6) + K |
C + 0.0508Mn - 0.0390V + 0.0020Ni +0.0836Mo 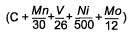 |
7 |
Log Δt (400HV) = M (CCP 7) + K |
C + 0.1972Mn - 0.0996V + 0.0917Ni + 0.1792Mo 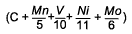 |
8 |
Log Δt (450HV) = M (CCP 8) + K |
C + 0.3743Mn - 0.3930V + 0.0240Ni + 0.3854Mo 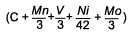 |
The reason for the change of sign is not known but may be due directly from an effect of vanadium on the γ → α transformation. It may also be attributed in part to the effect of vanadium as V(C/N) in providing some pinning of austenite grain boundaries and thus reducing austenite grain growth in the high temperature HAZ. Vanadium only has a weak effect in this respect and thus the effect would be more likely to be observed in fast thermal cycles when there is least time for dissolution of these particles and subsequent grain growth. At the lower hardness levels, which in general would be achieved by longer cooling times, some positive contribution to hardness through a precipitation hardening mechanism might be expected and therefore provide the explanation for the increasingly positive magnitude of vanadium.
2.5 HAZ toughness
There are relatively few studies that have specifically looked at the effect of increasing vanadium content on HAZ toughness. However, the generality of these for the as-welded condition, is that increasing vanadium up to levels of about 0.15% (mostly the upper level studied) either have no effect on the as-welded toughness, or can show useful improvements. The pattern of results is not always as this, since there have sometimes been different trends between studies of simulated HAZ and welded joints and between results produced from Charpy and CTOD testing. However, this author prefers to concentrate on information from welded joints in the strong belief that this is most likely to provide the most realistic representation of what is actually occurring.
Results reported by Mitchell et al [17] showed a strong improvement in Charpy toughness of multipass welds at 2kJ/mm in 0.12% C-steels, but hardly any change in CTOD transition temperature, see Fig.1. In a study of 2-pass welds in a series of lower (0.07%) carbon steels Hart and Sage [18] found that at 0.05-0.10%V there was some improvement in the grain coarsened HAZ toughness of the second pass, see Fig.2. Mitchell et al [17] using their own data, and data produced by Crowther [18] and Wang [19] , looked at the effect of heat input on as-welded toughness of vanadium steels and this information is shown in Fig.3. It indicates some clear differences between vanadium microalloyed and niobium and niobium+vanadium microalloyed steels, in that the vanadium microalloyed steels are more tolerant to increased heat input and when toughness is studied in terms of the CTOD transition temperature, interestingly an improvement in behaviour can be observed.
Fig.1. The effect of vanadium on the HAZ toughness of 0.12%C-1.6%Mn steels multipass welded at 2kJ/mm. ( Δt 8/5 = 12 secs)
Fig.2. The effect of vanadium on the temperature for 0.25mm CTOD in the HAZ of low-carbon (<0.07%) line pipe steels welded at 5kJ/mm, using two passes in the as-welded condition
Fig.3. The effect of heat input on the as-welded HAZ toughness of V, Nb and V + Nb steels
The above studies are essentially where the steel composition had just been differing in respect of the vanadium content and therefore provide the clearest opportunity to study the effect of vanadium on HAZ toughness. However, interesting trends can sometimes be found in steels in which other elements are not constant. For example in the large project reported by Harrison and Hart [20] they showed that when studying the sub-critically reheated grain coarsened HAZ vanadium-bearing steels produced a better 0.1mm CTOD transition temperature, for a given hardness, compared to vanadium-free and niobium-bearing steels, see Fig.4. Interestingly this pattern was observed for both as-welded and postweld heat treated (2 hours at 590°C) conditions. Li et al [21] studying the intercritically reheated grain coarsened (ICGC) HAZ also found that a 0.05% V steel gave better ICGC HAZ fracture toughness than either a plain C:Mn or a C:Mn:0.3Nb steel, although at 0.10% V toughness decreased associated with an increased M-A fraction.
In assessing HAZ toughness of carbon manganese and microalloyed steels consideration must be given to the influence of nitrogen. To the author's knowledge probably all the studies that have investigated the effect of nitrogen on HAZ toughness in C:Mn or C:Mn:Nb steels have tended to show that increasing nitrogen decreases the HAZ toughness and this has been generally ascribed to the presence of free nitrogen in the HAZ. In contrast to this, the position in C:Mn:Vsteels is different in that there have been fewer studies but that the majority of these have tended to show tolerance of increased nitrogen rather than an adverse effect on HAZ toughness. Hannerz [22] found little or no effect on HAZ toughness of increasing nitrogen from 60 to 130ppm. Mitchell et al [17] found increasing nitrogen from 80 to 170 ppm in multipass welds to also have little or no effect and this also mirrored the experience described by Lagneborg et al [19] for multipass welds. However, Lagnaborg also reported on single pass welds made at the high heat input of 8.0kJ/mm when an adverse effect was observed.
As part of the effort to reduce fabrication costs there is an increasing trend to reduce the number of occasions when it is necessary to carry out postweld heat treatment by demonstrating that adequate as-welded joint toughness can be achieved. In this respect the beneficial effects that alloying with vanadium can bring to improving as-welded toughness are significant. Nevertheless, there will be some circumstances where postweld heat treatment is necessary and the behaviour of vanadium-containing steels needs to be considered. As can be see from Fig.1(a) the effect on Charpy toughness shows that for vanadium levels of up to about 0.06% toughness is about equal to or better than that in the as-welded condition. For higher levels of vanadium some deterioration in as-welded toughness is noted. In contrast to the Charpy behaviour, the CTOD transition temperature data for the multipass welds in Fig.1(b) show substantial improvement as a result of postweld heat treatment, the CTOD transition temperature improving by 30-50°C. For thicker section (50mm) higher heat input (5kJ/mm) welds, Hart and Mitchell [24] found for a 0.12C, 0.10V steel that the 40J Charpy transition temperature improved from -24 to -39°C, while the CTOD at -10°C showed only a small fall from 0.46 to 0.30mm. This mixed pattern of behaviour would be asummation of effects of tempering processes and precipitation hardening during postweld heat treatment. The extent of these would also depend on the condition of the prior microstructure, itself a reflection of whether the weld was made at medium or high heat input.
2.5 Weld metal toughness
The influence of parent steel microalloying on weld metal toughness, for arc welding, is really only of concern for those processes that dilute large amounts of the parent material into the weld metal and the principal arc welding process capable of doing this is submerged arc welding. The position for this process in respect of vanadium, and niobium, was reviewed by Dolby [25] some years ago and although the situation showed the usual degree of complexity, it was apparent that vanadium additions were slightly better tolerated than niobium additions. Moreover he noted that vanadium additions were ableto provide some degree of promotion of acicular ferrite type microstructures which in general can improve the toughness of weld metals.
Since that review interest has grown in the use and application of power beam processes which in their preferred mode of use i.e. welding autogenously without filler, dilution is obviously very high. Microstructural development in power beam weld metals is different to that in most of the arc welding processes since in the absence of fluxes and active shielding gases the weld metal oxygen content is very much lower, and similar to that of the parent steel. Inthis respect some work by Abson and Francis-Scrutton [26] is of interest since it showed in the low oxygen content prevailing in TIG welds, analogous to that in power beam welds, vanadium additions of 0.04% to the weld (by dilution from the parent steel) provided useful increases in the acicular ferrite fraction of 20-30%.
3 Discussion
3.1 Vanadium and weld zone microstructures
Particularly in relation to the toughness of welded joints it would be apparent from the above that there are several recorded examples of where vanadium additions to C:Mn steels can either produce some useful improvement or the hardening tendency can be tolerated. Probably the most common theme which runs through the various explanations that have been put forward for these observations relate to changes in the type of transformed microstructure that are produced by vanadium additions. These are changes from a microstructure dominated by grain boundary nucleated products as in C:Mn and particularly C:Mn:Nb steels, to microstructures with a significant degree of intragranular nucleated products, often referred to as intragranular ferrite typical in V-microalloyed steels. The advantage of this change for toughness is that it tends to reduce the effective colony size of bainite or ferrite with aligned second phase, thereby reducing the effective cleavage crack size and improving the ductile to brittle transition temperature. This 'vanadium-effect' on transformed microstructure appears to be able to be active in both HAZ and weld metal microstructure development. Indeed the author has seen it in several instances where it can be contrasted with a coarse type of microstructure that typically develops in its absence. Figure 5 shows the effect in a high heat input (5kJ/mm) weld HAZ from the work of Harrison and Hart [20] and is believed to have contributed to the better performance of the vanadium steels in Fig.4. The effect has also been observed in both laser and electron beam welds in vanadium-containing steels as evidenced by the microstructures in Fig.6 & 7. Finally, the greatest contrast, epitomising the vanadium-effect, is perhaps in Fig.8 which shows the influence of a high level of vanadium on weld metal produced from cellulosic coated electrodes, as part of a development programme in the late 70's and early 80's. [27] From a weldability point of view, the vanadium-effect is a great potential advantage but it would appear that more work would need to be done to give a greater understanding of how it occurs, so that the effect can be maximised.
Fig.4. Influence of SCGHAZ hardness on 0.1mm CTOD transition temperature
Fig.4a) as welded condition
Fig.5. HAZ microstructures at 5kJ/mm
Fig.5a) C:Mn:Nb steel
Fig.6. Fused zone microstructure of autogenous laser welds
Fig.6a) 0.07C, 1.7Mn, 0.43Si, 0.026Al steel
Fig.6b) 0.07C, 1.7Mn, 0.43Si, 0.16V, 0.029Al steel
Fig.7. Fused zone microstructures of autogenous welds in electron beam welds
Fig.7a) 0.07C, 1.7Mn, 0.43Si, 0.026Al steel
Fig.7b) 0.07C, 1.7Mn, 0.43Si, 0.16V, 0.029Al steel
Fig.8. Root run weld metal microstructures of pipe butt welds made with E6010 type electrodes
Fig.8a) 0.07C, 1.7Mn, 0.3Mo, 0.03Nb steel
Fig.8b) 0.03C, 1.7Mn, 0.45V steel
3.2 Intragranular microstructural development
The development of intragranular acicular ferrite in weld metals has now long been recognised to be substantially associated with the presence of non-metallic inclusions, produced in substantial amounts in most arc weld metals. Their precise composition however has often been considered an important aspect to allow them to be effective particle microstructural controlling agents. It's worth asking whether the effect of these particles in weld metals, works solely through a nucleation role for the gamma to alpha transformation, or whether there is another, additional or alternative explanation/mechanism that can explain the vanadium effect, which at least in parent steels, is unlikely to be through an influence on non-metallic inclusions. The current information in the literature that might aid the understanding of the 'vanadium-effect' is sparse but an early brief paper by Uchino et al [28] and Hasegawa et al [29] looking at mechanisms of ferrite grain refinement in normalised high niobium vanadium steels, suggests that it might arise from the effect of interphase precipitation of VN at the gamma alpha interface, preventing ferrite graingrowth as well as from the precipitation of VN within austenite grains. Ochi et al [30] reported they had found that VC, precipitated on VN, itself precipitated on MnS particles provided effective sites for intragranular nucleation of ferrite. More recently still, Kimura et al [31] have described how they believe that VN particles are able to produce a finer ferrite grain size in heavy gauge H-shapes. They believe VN precipitated at both gamma grain boundaries and grain interiors provide effectivenucleation sites for ferrite. The nucleation of ferrite in an allotriomorphic form on VN precipitates at prior gamma grain boundaries is certainly consistent with the blocky grain boundary ferrite which in the author's experience is characteristic of a vanadium containing weld metal and very well emphasised in the microstructure in Fig.8b.
In part the development of acicular ferrite should be seen as a competition between transformation events at and near the austenite grain boundary and intragranular nucleation events. More specifically, a competition between two alternative sequences of events. The first being stable growth of the allotriomorphic ferrite as the temperature decreases, allowing the remaining austenite to transform by intragranular nucleation and growth. The second sequence is that of the α/ γ boundary of the allotriomorphic ferrite becoming unstable and changing to the more rapid Widmanstätten ferrite growth mechanism which sweeps over the austenite grain before any intragranular nucleation and growth can occur. The work of Cuddy and Lalby [32] on HAZ microstructure development in TiN is relevant to this. They noted that in a TiN steel Widmanstätten ferrite growth from the grain boundary allotriomorphic ferrite was markedly restricted, compared with that in a Tifree reference steel, and that blocky, intragranular ferrite was promoted instead. They believe that fine TiN particles retarded the rapid edgewise growth of the Widmanstätten plates and that this allowed time for ferrite tonucleate intragranularly, aided by larger TiN particles. So its worth considering whether the vanadium effect occurs more because of what vanadium does either directly or through VN interface precipitation, on the stability of the α/ γ boundary associated with the allotriomorphic ferrite, thus allowing intragranular nucleation to occur, or whether it has a more direct effect on enhancing intragranular nucleation sites. He and Edmonds [33] have recently reported strongly producing the vanadium acicular ferrite effect in some high purity experimental C:Mn steels. They observed segregation of vanadium both at prior austenite grain boundaries and within austenitegrain interiors, and have suggested [34] that Fe-V clusters might provide suitable sites for embryonic acicular ferrite nucleants.
Clearly a greater understanding of the mechanism of the V-producing acicular ferrite effect is needed so that it can be actively applied to allow the consistent production of acicular ferrite in both the HAZ and weld metal and hence give improvement in joint toughness.
4 Concluding remarks
Just as with other microalloying routes vanadium-microalloying, by facilitating reductions in steel carbon content, can provide improvements in steel weldability. Moreover, there is now clear evidence that vanadium-microalloying canbring additional benefits, especially to weld joint toughness, by virtue of its influence on microstructural development. Specifically the promotion of intragranular decomposition of austenite allows the development of finer effectivegrain sizes with the concomitant improvement in resistance to cleavage fracture.
In contrast to niobium, vanadium-microalloying is most effective with enhanced nitrogen levels, yet there is understandable concern with this, based on the established adverse effect of nitrogen on weld joint toughness in C:Mn andC:Mn:Nb steels. More data are needed on the effect of nitrogen in vanadium microalloyed steels, but at least for lower heat input welding available data shows little or no adverse effect, possibly because of the beneficial effects of vanadium on HAZ and weld metal microstructures.
Power beam welding, especially laser welding, is gaining in areas of application and provides significant opportunities for applying and maximising the 'vanadium effect' to both HAZ and fused zone microstructural development.
5 References
- Bailey N and Jones S B: 'The solidification cracking of ferritic steel during submerged arc welding', Weld. J, 1978, 57, 217s-213s.
- Mandel'berg S L, Rybacov A A and Sidorenko B G: 'Resistance of weld joints in steel tubes to hot cracking', Automatic Welding, 1972, 25, 3, p1-5.
- Nakamura H et al: Proceedings of the 1 st International Conference on Fracture 2, Sendai, Japan, 1965, p863.
- Ito Y and Nakanishi M: IIW document X-668-72.
- Bailey N, Coe F R, Gooch T G, Hart P H M, Jenkins N and Pargeter R J: 'Welding steels without hydrogen cracking', Abington Publishing, 1973.
- British Standard specification for arc welding of carbon and carbon-manganese steels, BS 5315: 1984 (see also BS EN 1011-2:2001).
- Yurioka N and Kasuya T: 'A chart method to determine necessary preheat in steel welding', Welding in the World, 33, 5, p327-334.
- Stahl-Eisen - Werkstoffblatten 088 1993, Weldable fine grained structural steels, Guidelines for processing, particularly for fusion welding (see also BS EN 1011-2:2001).
- Hart P H M and Harrison P L: 'Compositional parameters for HAZ cracking and hardening in C-Mn steels', Weld. J, Oct 1987, 66, 10, p310s-322s.
- Hart P H M, Matharu I S and Jones A R: 'The influence of reduced carbon equivalent on HAZ cracking in structural steels', 7 th Int. Conf on Offshore Mechanics and Arctic Engineering, Houston, February 1988.
- Panton-Kent R: TWI Journal 1, 3, 1992, pp334-364.
- Courdreuse L et al: Proc International Conference on Interaction of steels with Hydrogen in Petroleum Industry Pressure Vessel Service. Paris, France, March 1989, MPC, pp51-59.
- Shimomura J et al: ISIJ International Vol 31 1991, pp379-386.
- Suzuki H: 1983 IIW Doc. IX-1279-83.
- Yurioka N, Ohshita S and Tamerhiro H: March 1981 AWRA Symposium, Pipeline Welding in the '80's, p1-15.
- Duren C and Lorenz K: 1982 IIW Doc. IX-B-11-82.
- Mitchell P S, Hart P H M and Morrison W B: 'The effect of microalloying on HAZ toughness', Microalloying '95, Pittsburgh June 1995.
- Crowther D N: British Steel Contract Report for Vanitec, March 1994.
- Wang G R, North H T and Lewis G K: Weld. J., January 1969, 1, p14s-22s.
- Harrison P L and Hart P H M: 'Relationships between HAZ microstructure and CTOD transition behaviour in multipass C:Mn steel welds', 2 nd Int Conf on Trends in Welding Research, ASM International, Gatlinburg, Tennesee, May 1989.
- Li N et al: ISIJ International Vol 41 2001, pp46-55.
- Hanners N E and Johnson Holmquist B: 'Influence of vanadium on the heat affected zone properties of mild steel', Metal Science 1974, 8, p228-234.
- Lagneborg R, Siwecki T, Zajac S and Hutchinson B: 'The role of vanadium in microalloyed steels', Scandinavian Journal of Metallurgy, 1999, 28, 5.
- Hart P H M and Mitchell P S: 'The effect of vanadium on the toughness of welds in structural and pipeline steels', Weld. J. July 1995, p240s-248s.
- Dolby R E: 'The effect of vanadium and niobium on weld metal properties', Proc of Steel for Linepipe and Pipeline Fittings, The Metals Society, London, October 1981.
- Abson D J and Francis-Scrutton N: 'Influence of Al,Ti,V and O on acicular ferrite formation in TIG weld metal', 15 th Int Offshore Mechanics and Arctic Engineering Conference, June 1996.
- Boothby P J and Hart P H M: 'Welding 0.45% vanadium linepipe steels', Metal Construction, September 1981, 13, 9, p560-569.
- Uchino K, Ohno Y, Yano S, Hasegawa T and Morikawa H: 'Development of high N-V type low Ceq HT50 (development of low carbon equivalent and high N-V HY50 steel plates - II)', Transactions ISIJ, 1982, Vol 22, p405.
- Hasegawa T, Funaki S, Morikawa H, Ohno Y and Uchino K: 'Mechanism of ferrite grain refinement in normalised high N-V steels, Transactions ISIJ, 1982, Vol 22, p404.
- Ochi T, Takahashi T and Takada H: 'Improvement of the toughness of hot forged products through intragranular ferrite formation', 30 th Mechanical Working Steel Processing Conf, Iron & Steel Soc., Warrendale, USA, 1988.
- Kimura T, Kawabata F , Amano K, Ohmori A, Okatsu M, Uchida K and Ishii T: 'Heavy gauge H-shapes with excellent seismic-resistance for building structures produced by the third generation TCMP', ASM Materials Solutions, September 1999.
- Cuddy L J and Lalby J S: International Conf on 'Technology & applications of high strength low alloy (HSLA) steels', ASM Metals Congress, Philadelphia, October 1983.
- Edmonds D V: 'The promption of acicular ferrite microstrucutre in C:Mn steel by vanadium', The 4 th International Conference on HSLA Steels, Nov 2000, Xi'an China, pp260-265.
- Zhang M, He and Edmonds D V: Solid-state Phase Transformations '99 (JIMIC-3), p1477.