Integrity of FPSO [Floating Production Storage and Offloading] Hull Structures
J R Still, J B Speck and G R Razmjoo
Published in 'The Naval Architect', International Journal of the Royal Institution of Naval Architects , March 2000, London, pp 28-36
(Jack Still is at Amerada Hess Ltd; while Julian Speck and Reza Razmjoo are from TWI Ltd)
FPSO options
An oil producer, contemplating the development of an oil and gas field, has to select the most economical way to exploit a field's reserves. In a recent offshore development, an operator decided on the use of a floating production storage and offloading (FPSO) vessel as the most efficient and cost effective way to produce 'first oil', i.e. in the shortest possible time. A decision, based on the economics of the field, was subsequently required to select one of the following FPSO options:
-
A purpose-built FPSO
-
A conversion of an existing tanker
-
An interception of a new build tanker (prior to, or during construction)
The 'purpose-built' and 'converted tankers' options are self-explanatory, whereas interceptions refer to an order placed with a shipyard for a tanker, where the future owner of the vessel is prepared to sell the slot in the shipyard's programme. Although such a vessel would be designed as a tanker, modifications can be made to meet the service requirements of an FPSO.
Conversion of a new-build tanker
In the case of an interception, with the exception of minor modifications, the vessel hull is designed and constructed in accordance with class rules. Structural alterations to the hull, such as the construction of a moon pool, through the bottom of the hull for the mooring system and risers, can either be incorporated into the shipyard building programme, or carried out at another location.
Several factors [1] must be taken into account to ensure that the vessel structure can operate successfully without suffering significant in-service fatigue damage. Although fatigue crack initiation does not discriminate between steels with different mechanical properties, suitable hull materials must be selected with improved fracture initiation toughness and crack arresting properties.
To ensure that any future fracture and fatigue programme can be implemented with confidence, consideration should also be given to additional inspection of critical areas during construction. Poor weld quality, Figure 1, can considerably reduce in-service fatigue life and promote fracture. It is advisable for the FPSO operator to agree with the shipyard to apply additional inspection during construction, i.e. undertaken either by the shipyard, or by the operator's on-site inspection team.
Fig. 1. Examples of poor weld profiles a)
Vessel hull materials
Trading tankers are built to a standard design where hull materials are selected for a particular service. Similarly, the design of a FPSO must take into account its service conditions. The fabrication of hull structures in the early 1940's had a high incidence of failure by brittle fracture [2,3] . However, considerable improvements in steel making techniques over the last fifty years, have produced materials with higher toughness levels and improved weldability.
Intercepting a suitable slot within a shipyard's programme, for modification of a trading tanker as an FPSO, can be difficult. The operator may have to pay a high price for the slot, and the hull materials originally specified for the intercepted tanker are unlikely to be ideal for the vessel's intended service. Shipyards will accommodate changes to the grade of hull steel, provided the operator accepts the costs involved.
The design of a recent interception, new-build FPSO originally specified Grade A for the tanker's side shell plates and Grade AH32 for the tanker's deck and bottom shell plates. In this instance, the operator approached the shipyard and agreed to change the hull materials to Grade D and Grade DH32, as outlined on Figure 2. Selection of the higher grade materials was based on the improved toughness requirements for these grades. In addition to the enhanced grade, the thickness of the deck and bottom shell plates was increased from 16.5 to 19.5 mm. The specification and the typical chemistry and mechanical properties for Grade D and Grade DH32 steels, compared with Grade A and Grade AH32 steels, are presented in Table 1 and 2 respectively.
Fig. 2. FPSO Hull materials
Location | Original Material | Thk mm | ABS Base Material | Thk mm |
A (Deck) |
Gr. AH32 |
16.5 |
Gr. DH32 |
19.5 |
B |
Gr. AH32 |
16.5 |
Gr. DH32 |
19.5 |
C (Side shell) |
Gr. A |
17.5 |
Gr. D |
17.5 |
D |
Gr. AH32 |
16.5 |
Gr. DH32 |
19.5 |
E (Bottom) |
Gr. AH32 |
16.5 |
Gr. DH32 |
19.5 |
Table 1: Chemical properties and product analysis
Grade | Chemical analysis |
C | Si | S | P | Mn | Ni | Cr | Mo | V | Ti | Cu | Nb | Al Soluble | N |
Chemical composition (All values quoted are maximum unless otherwise stated) |
A |
0.21 |
0.50 |
0.035 |
0.035 |
2.5 x C min |
See Note 1 |
|
|
See Note 1 |
|
|
|
AH32 |
0.18 |
0.10/0.50 |
0.035 |
0.035 |
0.90/1.60 |
0.40 |
0.20 |
0.08 |
0.05/0.10 |
0.02 |
0.035 |
0.02/0.05 |
0.015 min |
- |
D |
0.21 |
0.10/0.35 |
0.035 |
0.035 |
0.60 min |
See Note 1 |
|
|
See Note 1 |
|
|
|
DH32 |
0.18 |
0.10/0.50 |
0.035 |
0.035 |
0.90/1.60 |
0.40 |
0.20 |
0.08 |
0.05/0.10 |
0.02 |
0.035 |
0.02/0.05 |
0.015 min |
- |
Typical product analysis |
A |
0.12 |
0.24 |
0.008 |
0.02 |
0.97 |
0.02 |
0.03 |
0.01 |
- |
- |
0.03 |
- |
- |
- |
AH32 |
0.12 |
0.34 |
0.003 |
0.011 |
1.32 |
0.02 |
0.05 |
Tr |
- |
- |
0.01 |
- |
0.026 |
- |
D |
0.14 |
0.26 |
0.004 |
0.02 |
1.27 |
0.02 |
0.003 |
Tr |
- |
- |
0.01 |
- |
- |
- |
DH32 |
0.14 |
0.39 |
0.008 |
0.014 |
1.22 |
0.02 |
0.03 |
Tr |
- |
- |
0.02 |
0.02 |
0.039 |
- |
Note 1 - When Ni, Cr, Mo and Cu to be reported. When the amount does not exceed 0.02% these elements to be reported as < 0.02%. |
Table 2: Mechanical properties for hull materials
Grade | Thickness mm | Mechanical properties | Charpy impact properties |
UTS min N/mm 2 | Yield min N/mm 2 | Elongation Min % | Test Temperature °C | Longitudinal Joules | Transerves Joules |
Specification | | | | | | |
A |
< 50 |
400 |
235 |
22 |
- |
- |
- |
AH32 |
< 50 |
440 |
315 |
22 |
Zero |
34 |
24 |
D |
< 50 |
400 |
235 |
22 |
-20 |
27 |
20 |
DH32 |
< 50 |
440 |
315 |
22 |
-20 |
34 |
24 |
Typical Product Mechanical Properties | | | | | Average Impact Values |
A |
16 |
450 |
302 |
28 |
- |
- |
AH32 |
16 |
496 |
381 |
30 |
Zero |
366 |
D |
17.5 |
461 |
318 |
28 |
-20 |
210 |
DH32 |
19.5 |
541 |
449 |
25 |
-20 |
206 |
Hull weld metal selection
Welding procedures qualified for vessel construction are not unique to individual hull structures, i.e. they cover a range of steels and thicknesses. Hull materials are divided into three groups, i.e. Ordinary Strength, Higher Strength and Higher Strength, Quenched and Tempered (Q&T). Each group of materials has a range of acceptable filler metals approved by the classification societies. The grading system for welding consumables incorporates various categories depending on the grade of the parent material to be welded. Although filler metal grades are available for all grades of parent material, the most common filler materials used in tanker construction are Category 1Y, 2Y, 3Y and 4Y.
The filler metal grading system adopted by classification societies for Grades D and DH32 steels falls into either Category 2Y or Category 3Y. The filler metals nominated for the interception FPSO by the shipyard, for Grade D and Grade DH32 hull steels, were Category 2Y. (Category 2Y welding consumables are required to be Charpy impact toughness tested at zero °C). This selection was considered unacceptable by the FPSO operator, as Grade D and Grade DH32 steels are required to be impact toughness tested at -20°C. Since the vessel was destined for service in the North Sea, the operator requested that the shipyard change the filler metal to Category 3Y (which impact toughness tested at -20°C). This change was deemed to be an 'extra' to the contract, since the original Category 2Y welding consumables had been approved by the classification society.
Fracture control programme
Weld test plates
Summary details of the welding processes and consumables used for the construction of the outer hull are presented in Figure 3. The hull weld seams of particular interest were the Grade D and Grade DH32 steels that were welded using gas shielded flux cored arc welding (GSFCAW) and electro gas welding (EGW). The welding consumables for these seams were selected by the shipyard and comprised of two GSFCAW consumables, i.e. No. (1) and No. (2) to AWS A5.29, E80T1-K2 [4] , and an EGW consumable to AWS A5.26, EG70T-2 [5] .
Fig. 3. Welding processes used for block assembly and erection
Location | Welding Process | Application | Position |
A (Deck) |
GSFCAW (Root) GSFCAW |
Semi-automatic Automatic |
1G (Ceramic Backing) 1G |
GSFCAW |
Semi-automatic |
1G (Ceramic Backing) |
B |
GSFCAW |
Semi-automatic |
1G (Ceramic Backing) |
C (Side shell) |
GSFCAW |
Semi-automatic |
3G (Ceramic Backing) |
EGW |
Automatic |
3G (Ceramic Backing) |
D |
GSFCAW |
Semi-automatic |
3G (Ceramic Backing) |
E (Bottom) |
GSFCAW (Root) GSFCAW |
Semi-automatic Automatic |
1G (Ceramic Backing) 1G |
GSFCAW |
Semi-automatic |
1G (Ceramic Backing) |
Five weld test plates were manufactured, under conditions similar to those used during completion of the outer hull welds. Figure 4 is an example of a completed test plated welded with GSFCAW. Figure 5 illustrates the start of welding using the EGW process. The test plates were restrained with five strong-backs to prevent rotational distortion during welding. Examples of the welding parameters and run sequence for both GSFCAW and EGW welds are presented in Table 3 and Table 4, respectively. On completion of welding, the test plates were inspected by ultrasonic testing (UT) and magnetic particle inspection (MPI).
Fig. 4. Example of a GSFCAW test panel
Fig. 5. Welding of a EGW test panel
Table 3: GSFCAW procedures
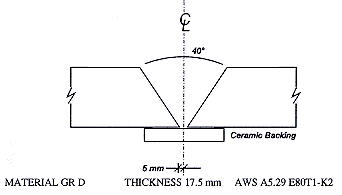 | 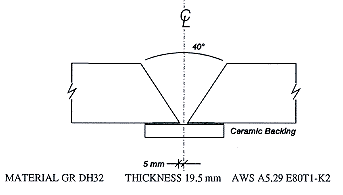 |
Bead4 Layers | Dia mm | Polarity | Amps | Volts | Weld Speed cm/min | Heat Input KJ/cm | Bead5 Layers | Dia mm | Polarity | Amps | Volts | Weld Speed cm/min | Heat Input KJ/cm |
1 |
1.2 |
DCRP |
180 |
26 |
7.5 |
39.5 |
1 |
1.2 |
DCRP |
210 |
27 |
11.6 |
29.3 |
2 |
1.2 |
DCRP |
210 |
28 |
16.7 |
21.1 |
2 |
1.2 |
DCRP |
210 |
29 |
19.6 |
18.6 |
3 |
1.2 |
DCRP |
210 |
28 |
14.4 |
24.5 |
3 |
1.2 |
DCRP |
220 |
32 |
14.8 |
28.5 |
4 |
1.2 |
DCRP |
180 |
28 |
13.9 |
23.0 |
4 |
1.2 |
DCRP |
200 |
27 |
15.7 |
20.6 |
|
|
|
|
|
|
|
5 |
1.2 |
DCRP |
190 |
27 |
13.2 |
23.3 |
Shielding Gas Shielding gas flow rate 25 Litres/min using 99% CO 2 |
Shielding Gas Shielding gas flow rate 25 Litres/min using 99% CO 2 |
Table 4: EGW procedures
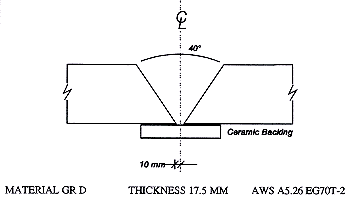 |
Bead | Dia mm | Polarity | Amps | Volts | Weld Speed cm/min | Heat Input KJ/cm |
1 |
1.6 |
DCRP |
410 |
38 |
9.6 |
97.4 |
Shielding Gas Shielding gas flow rate 25 Litres/min using 99% CO 2 |
Fracture initiation and crack arrest toughness
The purpose of a fracture control programme is to ensure that the external 'driving forces' (stress, temperature, flaw size, etc.) do not exceed the internal 'resistance factors' (yield strength, fracture toughness, etc.) The conventional approach to fracture control in welded steel vessels is based on Charpy impact energy requirements. However, Charpy impact energy is essentially a quality control parameter, and a more quantitative measure of toughness is required for fracture control, e.g. in terms of crack-tip opening displacement (CTOD), determined in accordance with BS 7448 [6,7] . Under severe loading conditions, e.g. accidental collision, the avoidance of crack initiation, cannot be guaranteed. In the event, the most important fracture property is then the ability of the material to arrest a fast propagating crack. The optimum combination of these two properties is seen as the most pragmatic engineering solution to the issue of fracture control.
A comprehensive programme of materials testing was subsequently undertaken on the five weld test panels to characterise the toughness of the weldments. The tests included CTOD fracture toughness tests and Pellini drop-weight tests, to determine the nil-ductility transition temperatures (NDTT) [8] , in the three regions of the hull seam welds, i.e. weld metal, heat-affected zone (HAZ), and parent plate.
Engineering assessment of failure by fracture
The purpose of an engineering critical assessment (ECA) is to determine the critical sizes of flaws, e.g. fatigue cracks, that can be tolerated by the vessel's hull without leading to failure by fracture. ECAs are based upon the expected in-service stresses and the measured fracture toughness of the materials. The range and the appropriate value ( δ mat) of CTOD fracture toughness test results at -10°C, for each of the test panels, are presented in Figure 6. The results of the fracture ECA subsequently indicated that the one-pass, high heat input EGW weldments were the most critical in terms of initiating a failure by fracture, Figure 7.
Fig. 6. CTOD test results performed at -10°C. The horizontal bar indicates the second lowest CTOD test results for a set of six tests
Fig. 7. Idealised failure loci for tolerable surface-breaking flaws for specific EGW and GSFCAW weldments. A surface-breaking flaw of dimensions a x 2c that falls above the respective failure locus would be unacceptable
Ideally, if a crack initiates from a pre-existing welding flaw, or an in-service fatigue crack, it should be arrested in the surrounding material without unduly affecting structural integrity. The use of hull steels with superior crack arrest properties can greatly enhance the safety of a FPSO vessel. The Pellini test is one of the simplest and most cost effective methods to quantify the crack arrest capability of steels.
The crack arrest temperatures (CAT) of the weldments were consequently estimated from the experimentally determined Pellini NDTTs, Table 5. CAT was then estimated using the following relationship [9] :
where CAT and NDTT are in °C, the applied stress level in this case was assumed to be σ = 150 N/mm 2, and section thickness B, is in millimetres. The CATs of the ABS Grade D and Grade DH32 parent materials were estimated to be -20°C and -43°C, respectively. The CATs of all of the three welds were estimated to be between -43°C and -85°C. However, the CAT in the HAZ of the electrogas welds (which was found to have the worst HAZ properties in this respect) was calculated to be 39°C. In the unlikely event of fracture in the FPSO's EGW hull side seam welds, a crack may not arrest in the HAZ of the electrogas welds, at operating temperatures below 39°C.
Table 5 Measured Pellini NDTTS
Description | Region | NDTT, °C |
ABS Gr. D |
Parent material |
-30 |
ABS Gr. DH32 |
Parent material |
-55 |
Gr. D, FCAW, E80T1-K2 (1) |
HAZ |
< 0* |
Weld metal |
-90 |
Gr. D, FCAW, E80T1-K2 (2) |
HAZ |
< -5* |
Weld metal |
-95 |
Gr. DH32, FCAW, E80T1-K2 (1) |
HAZ |
< -20* |
Weld metal |
-95 |
Gr. DH32, FCAW, E80T1-K2 (2) |
HAZ |
< -10* |
Weld metal |
-55 |
Gr. D, EGW, E70T-2 |
HAZ |
< +15* |
Weld metal |
< -80* |
* Insufficient specimens to confirm second no-break at NDTT +5°C |
Fatigue assessment programme
Weld toe improvement techniques
Some converted-tanker FPSOs have a tendency to develop fatigue cracks in fillet welded structural details in the hull. The poor fatigue performance of these details can be explained, firstly in terms of the overall geometric stress concentrations due to the details themselves, e.g. stiffener brackets, Figure 8. Secondly, the shape of the weld, which enhances the stress concentration. Thirdly, microscopic crack-like discontinuities, which are inherent in the toes of fusion welds and effectively eliminate the initiation phase in fatigue. And finally, the presence of high tensile welding residual stresses that effectively make all applied fluctuating stresses completely damaging.
Fig. 8. Potential sites for fatigue crack propagation from typical hull details
As part of the fatigue assessment programme, an investigation of two commonly used fatigue life improvement techniques was undertaken, i.e. weld toe rotary burr grinding and weld toe needle-peening. The aim of this programme was to quantify the magnitude of the fatigue life improvement provided by these techniques relative to as-welded details, Figure 9. Fillet welded fatigue test specimens of the two different grades of steel were fatigue tested in the as-welded, needle-peened and ground conditions, Figure 10. A variable amplitude load spectrum, based on the WASH spectrum for offshore structures was applied to obtain a ranking of the improvement techniques [10,11] . It was anticipated that in the case of the burr ground high strength steel, a more significant crack initiation period would be introduced than in the ordinary strength steels. However, in the case of needle peening, there was a concern that occasional compressive overloads could relax the beneficial compressive residual stresses induced by this technique.
Fig. 9. Typical improvement in fatigue strength of mild steel fillet welds resulting from selected weld toe improvement techniques
Fig. 10. Rotary ground fillet welded test specimens tested under variable amplitude fatigue loading
Surprisingly, it was consequently found that the calculated life improvement factors did not favour the use of one or the other life improvement technique. Both fatigue life improvement techniques were found to enhance the fatigue performance of non-load carrying fillets by a factor of at least two, compared to as-welded fillet welded joints, irrespective of the grade of parent material. The operator's choice of a suitable life improvement technique could therefore be based on practical considerations, e.g. ease of quality control, speed of application, required level of operator skill, etc.
In-service inspection programme
In-service inspection or survey programmes intended to ensure that no feature of the FPSO will pose a threat to the life of operating personnel, or to pollution of the environment. Once the critical weld joints on the vessel hull were identified, Figure 7, an in-service hull inspection programme could be established. The fatigue ECAs were closely tied to non-destructive examination (NDE) used during construction. (The detection and sizing limitations of the NDE technique were another input to the assessment to identify the critical hull welds. Any welds not inspected to ascertain that they were free of welding flaws, could therefore be considered to be more critical than welds that were only subjected to random sampling inspection).
In-service cyclic loading causes fatigue cracking in a vessel's welded structural details. By predicting the life of fatigue cracks at the critical weld locations, it is possible to arrange inspections to be carried out at predetermined intervals. However, it was paramount that inspection during construction was such that the weld quality was verified throughout the vessel. Failure to apply appropriate inspection would have nullified the intended benefits of the fracture control programme.
In the more general case of a weld detail experiencing a spectrum of applied loads, the cumulative damage due to individual load cycles would need to be summed. The usual method of doing this is to apply Miner's rule. The procedure is illustrated in Figure 11. A major task is the estimation of the stress history which will be experienced by a particular detail. The stress history can also be used to predict the life of fatigue cracks at critical weld locations, using fracture mechanics-based fatigue life methods. The basis for this is the integration of the 'Paris law' relationship between crack growth rate, da/dN, and the stress intensity factor range ( ΔK) [12] :
Fig. 11. Practical application of miner's rule for variable stress range loading of the vessel hull under wave action
ΔK is commonly expressed as ΔK = Y σ √( πa), where Y is a function of applied loading, crack size and the weld detail geometry. British Standard BS PD 6493 provides guidance on the use of this method for assessing welded structures, including the formulae for calculating ΔK for the weld detail, values of the constants m and C in the 'Paris law', and the method of numerical analysis [13] .
Since a variable inspection interval is not practical for an FPSO, inspections must be carried out a regular times that can be scheduled well in advance. Using this approach, it is possible to optimise the planned period between surveys of the FPSO's critical hull welds. The main purpose of a fatigue crack growth analysis is to ensure that flaws will not grow to an intolerable size leading to failure between inspections, Figure 12. The precise methods for achieving this goal depend on the practical and economic circumstances surrounding the operation of the FPSO.
Fig. 12. Illustration of use of crack depth versus endurance curve predicted by fracture mechanics to estimate remaining fatigue life
Conclusions
Ship-based FPSOs are relatively new concepts and unlike conventional tankers, they are semi-permanently moored and may experience rough sea conditions for much of their lives. Two factors have a bearing on the long-term structural integrity of the vessel's hull, i.e. the fracture properties of the outer hull's weldments, and the fatigue performance of fillet welded internal structural details. In any event, questions regarding material selection, fracture and fatigue performance and fabrication practices, with regard to the hull, must be resolved in order to ensure the vessel hull is suitable for its intended service. A fracture control and fatigue assessment programme is one method of establishing the structural integrity of an FPSO vessel's outer hull.
Acknowledgements
The authors acknowledge the guidance of Dr Mike Dawes (Principal Consultant, Fracture Testing, TWI) in preparation of this paper.
References
1 |
Specialist Panel V.6: |
'Structural design of floating production systems', 13 th. International Ship and Offshore Congress, Trondheim, Norway, August 1997 |
2 |
Bannerman D B and Young R T: |
'Some improvements resulting from studies of welded ship failures', Welding Journal, Volume 25, Number 3, March 1946 |
3 |
Acker H G: |
'Review of welded ship failures', Ship Structure Committee Report, Serial Number SSC-63, National Academy of Sciences, National Research Council, Washington, D.C. December 15, 1953 |
4 |
E80T1-K2, ANSI/AWS A5.29: |
'Specification for low alloy steel electrodes for flux cored arc welding', American Welding Society, Miami, 1998 |
5 |
EG70T-2, ANSI/AWS A5.26: |
'Specification for carbon and low alloy steel electrodes for electrogas welding', American Welding Society, Miami, 1998 |
6 |
BS 7448 - Part 1: |
'Fracture mechanics toughness tests, Method for the determination of K lc, critical CTOD and critical J values of metallic materials', British Standards Institute, London, 1991 |
7 |
BS 7448 - Part 2: |
'Fracture mechanics toughness tests, Method for the determination of K lc, critical CTOD and critical J values of welds in metallic materials', British Standards Institute, London, 1997 |
8 |
Pellini W S: |
'Guidelines for fracture-safe and fatigue-reliable design of steel structures', The Welding Institute, Cambridge, 1983 |
9 |
Wiesner C W: |
'Predicting structural crack arrest using small-scale material characterisation tests', Int. J. of Pressure Vessel & Piping, 69, 185-196, 1996 |
10 |
Technical Software Consultants: |
'User manual for WASH (Ver. W) time history', Milton Keynes September 1989 |
11 |
Schutz W and Pook L P: |
'WASH (Wave action standard history), A standardised stress-time history for offshore structures', Steel in Marine Structures, Ed. Noordhoek C and de Back J, Elsevier Science Publishers, Amsterdam, 1987 |
12 |
Paris P C and Erdogan F: |
'A critical of Crack Propagation Laws', Journal Basic Engineering, Vol. 85, 1960, pages 528 to 534 |
13 |
BS PD 6493: |
'Guidance on methods for assessing the acceptability of flaws in fusion welded structures', British Standards Institute, London, 1991 |