Ageing of Adhesively Bonded Joints - Fracture and Failure Analysis Using Video Imaging Techniques
R S Court 1,*, M P F Sutcliffe 1 and S M Tavakoli 2
1University of Cambridge
2TWI, Cambridge
*Corresponding author. Tel: +44-1223-332781; Fax: +44-1223-332662
E-mail address: rsc26@eng.cam.ac.uk
Paper published in International Journal of Adhesion and Adhesives, Volume 21, No.6. 2001 by Elsevier Science Ltd
Abstract
An investigation into the durability of adhesively bonded joints has been undertaken to help improve the prediction of joint life times. PMMA substrates have been bonded with a two-part acrylic adhesive to make single lap-shear joints. Joints have been aged in a hot/wet environment (40°C and 95% humidity) with no applied stress for up to 4000 hours and were tested in tension. The novel aspect of the research has been the development of a video imaging analysis technique which allows damage initiation and propagation within the joint to be detected as load is applied to the joint. Images of fracture initiation and damage propagation have been correlated with stress/displacement data for joints under tensile loading. The data from aged samples is compared with data from un-aged samples. Both the stresses at which damage is seen to initiate and the final failure stress of the joints decrease as the ageing time increases. The failure mode changes from cohesive failure within the PMMA substrate to failure within the adhesive, near the PMMA/acrylic adhesive interface.
1. Introduction
Predicting the long-term durability of adhesive joints is a significant problem limiting further industrial use of adhesives. There is little doubt about the detrimental effects the environment can have on an adhesively bonded joint. [1,2,3] A major difficulty is in determining which part of the bonded joint is affected by the environment - whether it be the adhesive, the interfacial regions or the adherend. If the affected part of the joint cannot be identified, then the joint failure mode cannot be anticipated and the joint cannot be designed for this failure mode. At present there is no standard design technique available which can predict the environmental degradation of adhesive bonds, [4] and most of the experience in determining joint failure modes has come from examining the fracture surfaces of joints after failure. [5]
These post-failure examinations, from the large number of studies concerned with joint durability (Reference [1] cites 80 references), have established that degradation of the interface between adherend and adhesive is a major cause of in-service joint failures. [1,4,6] These studies also reveal that there is frequently a change in the joint's failure mode, due to the effects of ageing. The main change is from cohesive failure, whether in the adhesive or adherend, to a failure in the interfacial region of the joint. [5,7,8] Previous work investigating joint durability has pre-dominantly used metallic adherends with epoxy adhesives. For example, work on aluminium 2024-T3 [6] identified many factors affecting joint durability, including the permeability of the adhesive to water. Other fracture mechanics based studies [7] used aluminium or steel with an epoxy and identified a change from cohesive failure within the adhesive to failure in the metal oxide layer after ageing.
The aim of the present study was to view damage evolution in the joint. A joint system was developed using transparent polymethylmethacrylate (PMMA) adherends, bonded with a two-part acrylic. The choice of materials was guided by previous work that had used transparent adherends. PMMA was bonded with a polyurethane adhesive [9] and with a two-part epoxy; [10] glass was bonded with polysulfide sealants. [11] Results [9,10] showed that PMMA joints with polyurethanes or epoxies fail adhesively, i.e. these adhesives do not adhere particularly well to PMMA, also confirmed by the authors' own preliminary studies. The glass/polysulfide system is used in glazing applications and is not intended for structural joints. An acrylic adhesive was found to adhere well to PMMA and although not the most widely considered of adhesive types, acrylics have been studied for use by the UK Ministry of Defence for ship based applications [12] and proposed for further study for comparison with epoxies and phenolics. [6] Acrylic adhesives are weaker and more flexible than the more widely used epoxy resins, but have a much greater ductility. [13] Hence a different approach is needed to understand and model the behaviour of acrylic joints, as compared with epoxies.
Three alternative approaches for modelling acrylics joints were considered. A linear elastic fracture mechanics approach [14] is probably not appropriate, due to the extensive ductile behaviour of the acrylic. [15] A second option is a J-integral approach. [16,17] However, there is a possible limitation since the J-integral represents both elastic and plastic energy components in a single value, and it is suggested that changes to adhesives may affect the elastic and plastic components independently. [15] A third option is a crack-bridging model, [18] using a force-displacement relationship to define the mechanical response of the adhesive. The insight gained from the work presented here is intended to help develop crack-bridging type models for ductile adhesives such as acrylics and toughened epoxies.
The work described in this paper presents results for lap shear joints made with PMMA substrates and an acrylic adhesive. By using transparent adherends it is possible to view damage progression both in the ageing and mechanical testing phases. Section 2 details the experimental method and section 3 describes the results both of mechanical testing and from observations. These findings are discussed in section 4.
2. Experimental
2.1 Materials, joint details and testing
Since the aim of the work was to view damage evolution inside the joint, transparent adherends were needed. The adherend material used was polymethylmethacrylate (PMMA) and the adhesive was a two-part toughened acrylic. Acrylic adhesives were successful in bonding glass reinforced plastic
[12] and the chosen acrylic adhered well to grit-blasted PMMA.
The lap-shear joint geometry was selected based on its ubiquitous nature and its ability to produce a realistic stress-state during mechanical testing. Details of materials, joint preparation, ageing environment and mechanical testing are given in Table 1. A schematic diagram of the test set-up is shown in Figure 1.
Table 1: Details of materials, joint preparation and testing
Substrate |
Polymethylmethacrylate (PMMA) sheet, 1.5mm thick |
Adhesive |
Two-part toughened acrylic |
Surface preparation |
Grit-blast; followed by degrease using 'Lotoxane', a petroleum distillate based solvent containing a blend of hydrocarbons |
Joint details |
Adherends: 100mm x 25mm x 1.5mm Single lap-shear samples: overlap length 12.5mm Bond-line thickness: 0.15mm ± 0.05 |
Ageing conditions |
Hot/wet environment: 40°C and 95% humidity, no applied stress |
Ageing times |
0, 500, 1000, 2000 and 4000 hours |
Number of samples |
Four samples for each ageing time |
Mechanical testing |
Tensile loading at a test rate of 1mm/min |
Video recording |
Simultaneously with the tensile test |
Fig.1. Test set-up. Video equipment and tensile lap-shear sample
2.2 Characterisation techniques - video and SEM
Tensile tests of the single-lap shear samples were video recorded using a CCD video camera and a VHS video recorder. The adherends and adhesive were transparent which allowed observation of changes within the adhesively bonded region. Changes were seen both after the ageing process and during mechanical testing. The recorded load-displacement data and video images were synchronised by using the time at which fracture occurred as a reference point.
The video images were used in two ways. Firstly, the areas of the joints which whitened during ageing were determined. Image analysis software was used to measure the grey-scale intensity of each pixel in the video image and, by suitable adjustment of a critical threshold intensity, an estimate was obtained of the percentage of the joint area affected by ageing. Secondly, by carefully examining the video images as the joint was loaded, the load at which the damage growth occurs during loading can be determined. The new damage appears as further whitening, apparently in the adhesive layer, which had a very different appearance to the undamaged adhesive and adherends. Load data was recorded every second, which was found to be sufficiently fast to give an accurate estimate of the load at which damage initiated.
To further understand the mechanisms of failure in the joint, the initial grit-blasted PMMA surface and representative fracture surfaces were gold coated and examined using scanning electron microscopy (SEM).
3. Results
In this section the mechanical response of the joint during loading is presented. In addition, video images are used to determine the amount of damage in the joint after ageing and the stress at which damage initiates during loading of the joint. SEM images of the failed joints provide details of the failure modes.
3.1 Mechanical response
Results from the tensile tests on PMMA/acrylic single lap-shear samples are presented in
Figure 2. This figure gives the joint average shear stress (i.e. load/joint area) versus cross-head displacement effectively measuring the elastic displacement of the sample ends, for samples aged for 0 to 4000 hours. Four samples from each ageing time were tested, with a typical example shown for clarity.
Figure 2 shows that the mechanical response of the joints is significantly affected by the ageing prior to testing. The joint stiffness, proportional to the slope of the stress-displacement plot, decreases by 13% with the first 500 hours of ageing. There is no significant further reduction in stiffness up to 4000 hours of ageing. The joint failure stresses, averaged over the four samples at each ageing time, are shown in
Table 2 and in
Figure 3. The shear stresses at which damage initiates, which were determined for each of the ageing times by examination of the video images, are presented in
Table 2 and
Figure 3. The joint failure modes for each ageing time are summarised in
Table 2.
Fig.2. Average shear stress in joint versus machine cross-head displacement. Tensile tests on PMMA/acrylic single lap-shear joints after various ageing times.
Fig.3. Average shear stress at damage initiation and final failure versus ageing time for PMMA/acrylic single lap-shear joints
Table 2: Data from tests on PMMA/acrylic single lap-shear samples
Ageing time (hours) | % of joint area affected by ageing | Average shear stress (MPa) | Failure mode |
Damage initiation | Final failure | Damage initiation | Final failure |
0 |
0 |
2.01 |
3.84 |
In adhesive fillet |
Cohesive substrate |
500 |
29 |
0.96 |
2.11 |
In adhesive layer |
Cohesive substrate and adhesive/near-interface |
1000 |
56 |
0.64 |
1.34 |
In adhesive layer |
Cohesive adhesive/near-interface |
2000 |
100 |
0.57 |
1.08 |
In adhesive layer |
Cohesive adhesive/near-interface |
4000 |
100 |
0.82 |
1.59 |
In adhesive layer |
Cohesive adhesive/near-interface |
Figure 3 shows that ageing reduces the stresses at which both damage initiation and final failure of the joints occurs. The changes are most marked in the first 1000 hours, with only a small reduction in the following 3000 hours. The slight increase in initiation and failure stress between 3000 and 4000 hours of ageing may be due to experimental scatter, arising from differences in joint preparation or testing. The standard deviations of results from the tensile tests are indicated on Figure 3 by the error bars. Note that there is a reduction in scatter associated with the change in failure mode from adherend failure to cohesive failure within the adhesive near the interface.
3.2 Observations of damage
With increased ageing time the physical appearance of the joint bonded area was changed - the adhesive layer stopped being transparent and became whitened and opaque. The joint area affected increased from 0% with no ageing, to 100% after 2000 and 4000 hours of ageing,
Table 2. Examples of the damage due to ageing are given for 500 and 1000 hour aged samples,
Figures 4 and 5. The observed whitening effect appears to be at, or near to, the interface between the adhesive and the PMMA substrate, based on the focus position from optical microscopy. The nature of the whitening is difficult to assess since through-transmission optical microscopy at the edge of the whitening effect reveals only a diffuse region of opacity,
Figure 6. No major features are apparent other than small particles within the adhesive. Some indication of the effect of the whitening is revealed when the joint is allowed to dry after ageing. The opaque region changes and micro-cracks form at the edge of the whitened region,
Figure 7. This suggests that the original opaque whitening is due to physical absorption of the water, leading to swelling of the adhesive layer. On drying, the adhesive shrinks, forming the micro-cracks.
Fig.4. PMMA/acrylic joint bonded area after 500 hours ageing
Fig.5. PMMA/acrylic joint bonded area after 1000 hours ageing
Fig.6. Through-transmission optical micrograph of edge of opaque region in PMMA/acrylic joint after 500 hours ageing
Fig.7. Through-transmission optical micrograph of edge of opaque region in PMMA/acrylic joint after 500 hours ageing, followed by 100 hours drying in air at 20°C
Figure 3 shows how the failure mode of the joints changes with increased ageing time. With no ageing, damage initiates in the adhesive fillet - apparent as whitening - and final failure is in the adherend. After 500 hours ageing, damage initiation changes to being in the adhesive layer within the joint; there is damage growth in the adhesive and final failure is in the adherend. After 1000, 2000 and 4000 hours of ageing, damage initiates in the adhesive layer in the joint and final failure is by debonding.
Figures 8 and 9 show SEM images of the fracture surfaces of a joint aged for 1000 hours, while Figure 10 shows an image of a grit-blasted PMMA surface, prior to bonding. Figure 8 shows an adherend failure surface that visually appears to have little or no adhesive on it. However, a close comparison of Figures 8 and 10 shows that the morphology of the fracture surface is very different from that of the PMMA surface prior to bonding. This indicates that there is a thin layer of acrylic adhesive present on the surface seen in Figure 8 and that failure of the adhesive occurs near the interface. Figure 9 is a SEM image of the opposite surface to Figure 8, showing the failed toughened acrylic adhesive. Ductile tearing and the presence of micro-voids from the failure process are visible. These micro-voids appear to be similar to those seen in toughened epoxy adhesives. [19]
Fig.8. SEM image of fractured PMMA/acrylic joint with near-interface failure in the adhesive. The scale bar is 10µm long.
Fig.9. SEM image of fractured PMMA/acrylic joint. Opposite face to Fig.8, showing cohesive failure in acrylic adhesive. The scale bar is 10µm long.
Fig.10. SEM image of grit-blasted PMMA surface. No adhesive present. The scale bar is 10µm long.
3.3 Evolution of damage in the joint
By examining the video images it was possible to track the evolution of damage in the joint during loading and investigate the effect of ageing on the way in which damage grew. For all the tests, significant damage was observed in the joint prior to failure.
Un-aged joints showed a typical lap-shear response. Failure starting as cracking in the adhesive fillet, with very visible whitening and final failure occurring in the substrate close to the adhesive fillet. [20] Joints aged for 500 hours had 29% whitening within the bonded area prior to loading. As the joint was loaded this whitening extended. Final failure of the joints was by failure in the adherend, usually at the edge of the whitening damage.
The evolution of damage growth as the joint was loaded is illustrated in Figures 11 and 12. Figure 11 shows the variation in average joint shear stress with cross-head displacement for a joint aged for 500 hours. Figures 12a, b and c show images of the bonded section of the joint corresponding to the three points A, B and C marked on Figure 11. Figure 12a shows the joint with only the damage due to ageing - the whitened area at the edge of the bonded region. At the load shown in this figure, damage is on the point of growing. Figure 12b, taken at a slightly higher load, shows growth of the whitening damage caused by the applied loading, mainly at the bottom edge. The joint at final failure, caused in this case by adherend fracture, is shown in Figure 12c, illustrating still more growth of the damaged region in the joint.
Fig.11. Average adhesive shear stress versus machine cross-head displacement. Tensile test on PMMA/acrylic joint - 500 hours ageing
Fig.12a, b and c. Damage growth in PMMA/acrylic joint under tensile load
For samples aged for 1000 hours, there was rather greater whitening of the joint prior to loading, with 56% of the joint area affected. During loading the damage was seen to extend into the transparent bonded area. Final failure of the joint was by debonding of the two adherends, with no substrate fracture. The 2000 and 4000 hour aged samples had whitening extended over the whole joint area, although the two adherends were still effectively bonded. During loading it was possible to observe further whitening of the joint and a damage front progressing through the bonded area. Final failure was by complete debonding of the two adherends, with no adherend fracture.
4. Discussion
4.1 Damage due to ageing
In this paper ageing is considered to be due to the combined effects of humidity, temperature and time. This ageing process causes damage to the adhesive joint, in the form of whitening in the adhesive. This damage does not totally degrade the mechanical performance of the adhesive, since the adherends are still bonded, even when all of the adhesive is seen to be affected by the environment. Once the adhesive has been degraded, further damage in the adhesive occurs when the joint is loaded. This poses a question as to whether ageing damage is the same as damage caused by loading. Both are characterised by whitening within the adhesive. The SEM images reveal the nature of the damage after tensile loading i.e. micro-voids. It is possible that the whitening seen after ageing is similar to that from tensile testing but of a less severe nature, so that the joint remains intact but with degraded performance. It is unlikely that the whitening is due to adhesive shrinkage on curing, since the joints were transparent before ageing started.
Water diffusing into the adhesive is a likely explanation for the observed whitening. Diffusion is driven by physical processes and once the water is within the adhesive layer, chemical reactions could occur. However, chemical changes, detectable using Fourier transform infra-red (FTIR), were discounted following FTIR spectroscopy studies on acrylic adhesive samples that had been immersed in water and which were whitened. No obvious changes to the FTIR spectrum of the adhesive were seen. If water had been chemically reacting with functionalities in the acrylic, changes would have been expected in the FTIR spectrum. This suggests that water is diffusing into the adhesive and that the whitening effect is probably due to physical effects such as swelling, rather than any chemical reaction.
Table 3 summarises a thermodynamic calculation for the estimated work of adhesion of the PMMA-acrylic joint system, following the method described in [3] . This calculation requires data for the polar, P, and dispersive, D, components of the surface free energies, γ, of the substrate and adhesive. Surface energy values for PMMA and acrylic adhesive have either been measured experimentally or determined from [3] . The calculations have been performed using the experimental data for grit-blasted PMMA, although in fact using the data for as-received PMMA [3] shows the same trend. The positive value of the estimated work of adhesion for PMMA-acrylic in the presence of water suggests that the interface will not be degraded by water. This result is not unexpected for a polymer-adhesive joint system, and is in contrast to metal-adhesive joints where there is usually a negative work of adhesion in the presence of water, making it unstable. [5]
Table 3 - Thermodynamic data for PMMA/acrylic joints
Material | γD (mJ/m2) | γP (mJ/m2) | γT (mJ/m2) |
PMMA - grit blasted (values from experiment) |
29.9 |
11.5 |
41.1 |
PMMA - as received (values from [3] ) |
35.9 |
4.3 |
40.2 |
Acrylic adhesive - estimate (based on [3] ) |
8.3 |
37.2 |
45.5 |
Water [3] |
22 |
50.2 |
72.2 |
Work of adhesion calculations [5] |
|
PMMA/acrylic, dry:- work of adhesion = |
|
|
|
PMMA/acrylic, wet:- work of adhesion = |
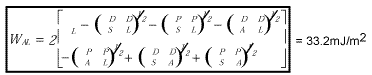
|
|
|
Key γ = Surface free energy. D = dispersive component, P = polar component, T = total surface free energy. Subscripts: S = substrate, PMMA; A = adhesive, acrylic; L = liquid, water. |
A physically controlled diffusion process is consistent with the observed extent of whitening in the joints. The joint area affected by ageing shows a linear increase with time up to 2000 hours, Table 2. Whitening is seen to extend in from all four edges of the joint in an essentially symmetrical manner, Figures 4 and 5. The edge of the whitening is shown as a through-transmission optical micrograph in Figure 6, and is a diffuse region about 0.7mm in width. As described in section 3.2 there are no significant features in the whitened, opaque region, shown as the dark part of the micrograph. However, after drying a joint, cracks appear, Figure 7. This suggests that diffusion of the moisture into the joint is a physical process leading to swelling of the adhesive, which then cracks when it is dried. The cracks in Figure 7 are at a spacing of around 0.2mm and are perpendicular to the edge of the whitening.
A diffusion coefficent, Da , for the acrylic adhesive was found by weighing 2mm thick samples that were aged in the same environment as the joints. An equilibrium percentage mass increase of 7% was reached and using Crank's formula [21] for the diffusion coefficient, Da = 0.049/(t/l2)1/2, with t1/2 = 35hours, and l = 2mm, Da was estimated as 155x10-14m2s-1. Using this value of Da and Comyn et al's work [22] , the fractional water up-take of the joint, Ma / Me , can be estimated from equation 1:
Ma / Me = 1 - (1 - M1 / Me)(1 - M2 / Me) (1)
where M1 / Me and M2 / Me are the fractional up-takes from two perpendicular joint edges, marked as 1 and 2 on Figure 1. M1 / Me and M2 / Me are calculated from equation 2:
where Mt is the mass at time t and Me is the mass at equilibrium. Da is the diffusion coefficient and L is the thickness of the material, which for edge 1 is the overlap length, 12.5mm, and for edge 2 is the joint width, 25mm. The joints were calculated to have a fractional water up-take of 0.87 after 4000 hours ageing. This is in reasonable agreement with the evidence from the video imaging of 100% whitening after 4000 hours, especially since the PMMA adherends do allow water to diffuse into the bonded area, reducing the time for the joint to become saturated.
4.2 Effect of ageing on joint response
The three major effects of ageing on the joint which have been observed are:
- a reduction in the stress at which damage initiates in the joint;
- a reduction in the final failure stress of the joint;
- a change in the joint failure mechanism.
The reductions in initiation and failure strength are due to the effect of the ageing environment on the adhesive and the near-interface region of the joint. It is proposed that the ageing environment changes the mechanical properties of the adhesive and near-interface region, leading to changes in the mechanism by which the joint fails. The changes in joint failure mechanism can be seen since the joints are transparent - the joints initially fail in the adherend; after ageing the failure mode changes to near-interfacial. After ageing, damage is seen to propagate through the adhesive layer interfacial region with final failure either in the adherend or near the interface, dependent on the length of time the joint is aged for. This change in failure mechanism is strong evidence that the adhesive properties have been altered by the ageing environment.
The stress distribution within single lap-shear joints under tensile loading is non-uniform, with shear and through-thickness tensile stresses concentrated at the ends of the joint overlap region. [20] It is this concentration of stresses that leads to failure in the PMMA adherend in the un-aged joints and is a similar result to work using glass reinforced plastic bonded with acrylics. [12] The significantly greater scatter for the un-aged tests with adherend failure probably arises from the sensitivity in this case to details of the stress concentration at the fillet or the edge of the damage zone. The ageing process evidently changes this stress distribution, since the joints now do not fail in the adherend. The change in stress distribution within the joint under load will be as a consequence of changes in adhesive material properties due to the ageing environment.
Although the initiation and final failure stresses of the joints are reduced, it should be noted that the joint stiffness is not changed greatly by the ageing process, a 13% reduction being recorded. This is significant for applications where displacement rather than load is the major design consideration.
The results detailed here have some similarities with other work on adhesive joint durability, which also describe a change in failure mechanism due to the effects of ageing. [5,6,7] Un-aged joints had a conventional failure mode with damage starting in the adhesive fillet followed by adherend failure, similar to that reported in [20] . Aged joints changed to an interfacial type of failure with micro-cracking damage similar to that described in [19] . There are some subtle differences though, mainly in the location of the near-interfacial failure observed after ageing. With metal adherends bonded with epoxy, failure after ageing can be through the metal oxide layer. [7] In the tests reported here with acrylic adhesive, failure is within the adhesive, very close to the interface with the PMMA adherend. Unlike metals, diffusion of moisture in this case can also occur through the adherends. This difference in the detail of the failure location, dependent on both adherend and adhesive type, is an important point, since it emphasises the critical nature of the interface region in joint durability.
5. Conclusions
5.1 Mechanical
Subjecting PMMA-acrylic joints to a hot/wet ageing environment of 40°C and 95% humidity leads to a significant reduction in the joint failure stresses and a change in the failure mode. The failure mode changes from fracture of the PMMA substrate to near-interface failure of the acrylic adhesive. This change in failure mode is evidence that the ageing environment has changed the physical and mechanical properties of the acrylic adhesive and/or acrylic-PMMA interface. By changing the adhesive or interface properties, the stress distribution within the joint is modified, which leads to the changed failure mode and reduced joint failure stresses.
5.2 Video imaging
The video imaging technique was designed to exploit the transparent adherends and adhesive used. By videoing the joint it becomes possible to collect additional information on the modes of damage initiation, damage development and joint failure. During testing, damage in the bonded region of the joint was seen to initiate and grow at loads well before the final failure load.
5.3 Future work and modelling
The change in failure mode is significant, since any predictive model for joint durability will need to be able to deal with changes in physical and mechanical properties that are occurring in the critical region of the adhesive near the interface. The proposed route for modelling of the PMMA-acrylic joint is to use a crack-bridging model, mainly due to the high ductility of the adhesive. The model will require a suitable force-displacement relationship for the adhesive and possibly the interfacial region. This differs from the other routes for adhesive joint durability modelling which have used mechanistic approaches, stress analysis or fracture mechanics. [2]
6. Acknowledgements
Financial support for the research programme, which is part of the Post-Graduate Training Partnership funded by EPSRC and DTI, is gratefully acknowledged. Additional technical and industrial support by Permabond is also much appreciated.
References
- Tavakoli S M: Durability of structural adhesives and adhesively bonded joints - a review. TWI Report No. 7198.01/93/770.03 and 548/1996 Abington: 1996.
- Kinloch A J: Predicting the lifetime of adhesive joints in hostile environments. The Performance of Adhesive Joints - MTS Adhesives Project 3: Environmental Durability of Adhesive Bonds. Report No 5,Document Ref AEA-ESD-0082, August, 1994.
- Kinloch A J: Adhesion and Adhesives - Science and Technology. 1st ed. London: Chapman and Hall, 1987.
- Davis M and Bond D: Principles and practices of adhesive bonded structural joints and repairs. Int J Adhesion and Adhesives 1999; 19: 91.
- Gledhill R A, Kinloch A J: Environmental failure of structural adhesive joints. J Adhesion 1974; 6: 331.
- Armstrong K B: Long-term durability in water of aluminium alloy adhesive joints bonded with epoxy adhesives. Int J Adhesion and Adhesives 1997; 17: 89.
- Taylor A C, Kinloch A J: The durability performance of structural epoxy adhesives. Fifth Int Conference, Structural Adhesives in Engineering V. Bristol, 1998. P. 53.
- Aglan H, Rowell T, Ahmed T, Thomas R: Durability assessment of composite repairs bonded to aircraft structures. J Adhesion Sci and Technol 1999; 13 (1): 127.
- Andersen G P, Devries K L: Predicting bond strength. In Tenth annual meeting of the Adhesion Society Inc. Williamsburg, Virginia, U.S.A 1987.
- Chen N N S, Niem P I F, Lee R C: Experimental investigation of epoxy bonded polymethylmethacrylate joints. J Adhesion 1990; 31: 161.
- Lowe G B, Lee T C P, Comyn J, Huddersman K: Water durability of adhesive bonds between glass and polysulfide sealants. Int J Adhesion and Adhesives 1994; 14: 85.
- Bowditch M R, Stannard K J: Adhesive bonding of GRP. Composites 1982; 13: 298.
- Garg A C, Mai Y W: Failure mechanisms in toughened epoxy resins - a review. Composites Sci and Technol 1998; 31: 179.
- Kinloch A J: Adhesives in Engineering. In Proceeding of the Institution of Mechanical Engineers. Eighty-fourth Thomas Hawksley Memorial Lecture in Institution of Mechanical Engineers, London IMechE,1996.
- Hand H M, Arah C O, McNamara D K, Mecklenburg M F: Effects of environmental exposure on adhesively bonded joints. Int J Adhesion and Adhesives 1991; 11: 15.
- Williams J G: Fracture mechanics of polymers. Chichester: Ellis Horwood Ltd, 1984.
- Knott J F: Fundamentals of fracture mechanics. London: Butterworth & Co, 1973.
- Bao G, Suo Z: Remarks on crack-bridging concepts. .App Mech Rev 1992; 45(8): 355.
- Kinloch A J, Shaw S J, Tod D A, Hunston D L: Deformation and fracture behaviour of a rubber-toughened epoxy: 1. Microstructure and fracture studies. Polymer 1983; 24: 1341.
- Adams R D, Comyn J, Wake W C: Structural adhesive joints in engineering. 2nd ed. London: Chapman and Hall, 1997.
- Crank J: The Mathematics of Diffusion. Oxford: Oxford University Press, 1975.
- Comyn J: Day J, Shaw S J. Durability of aluminium-sealant joints in jet-fuel, water and antifreeze. Int J Adhesion and Adhesives 1997; 17(3): 213.