Weld symbols have been used for many years and are a simple way of communicating design office details to a number of different industrial shop floor personnel such as welders, supervisors, and inspectors. Subcontractors are often required to interpret weld symbols on engineering drawings, from perhaps the main contractor or client to determine the type of weld needed. It is essential that everyone should have a full understanding of weld symbol requirements to ensure that the initial design requirement is met.
There are a number of standards which relate to weld symbols, including British, European, International and American (American Welding Society) standards. Most of the details are often similar or, indeed, the same, but it is essential that everyone concerned knows the standard to be used. One of the first requirements therefore is:
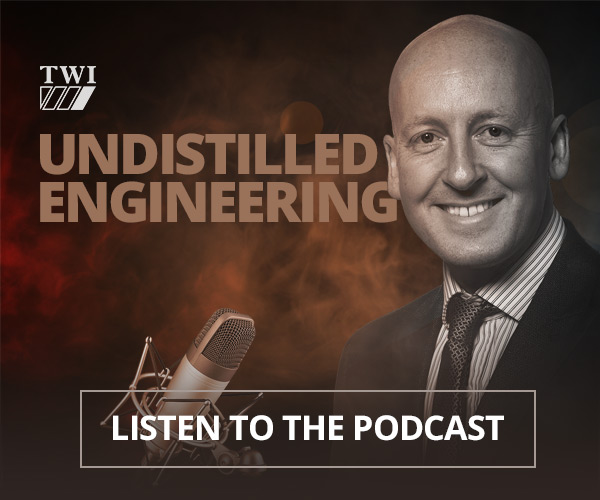
Which Standard?
The UK has traditionally used BS 499 Part 2. This standard has now been superseded by BS EN 22553, however in many welding and fabrication organisations there will be old drawings used that make reference to out of date standards such as BS 499 Pt 2.
BS EN 22553 is almost identical to the original ISO 2553 standard on which it was based. Therefore, we can say, for at least this article's scope, there are no significant differences, but it is essential that the reader consults the specific standard. The American system is also similar in many respects but will not be covered here.
Basic Requirements
All the standards have the same requirements in relation to the following items:
- Arrow line and arrow head
- Reference line
The arrow line can be at any angle (except 180 degrees) and can point up or down. The arrow head must touch the surfaces of the components to be joined and the location of the weld. Any intended edge preparation (i.e. for a groove weld) or weldment is not shown as an actual cross- sectional representation, but is replaced by a line. The arrow also points to the component to be prepared with single prepared components. See Figs. 1-4.
Symbol types
To the basic set-up of the arrow and reference line, the design draughtsperson can apply the appropriate symbol, or symbols for more complex situations.
The symbols, in particular for arc and gas welding, are often shown as cross-sectional representations of either a joint design or a completed weld. Simple, single edge preparations are shown in Fig. 5.
For resistance welding, a spot weld and seam weld are shown in Fig. 6:
Joint and/or weld shape
The above examples can be interpreted as either the joint details alone or the completed weld, however, for a finished weld it is normal to find that an appropriate weld shape is specified. Using the examples above, there are a number of options and methods to specify an appropriate weld shape or finish.
Butt welded configurations would normally be shown as a convex profile (Fig.7 'a', 'd' and 'f') or as a dressed-off weld as shown in 'b' and 'c'. Fillet weld symbols are always shown as a 'mitre' fillet weld (a right-angled triangle) and a convex or concave profile can be superimposed over the original symbol's mitre shape. See Fig. 7.
As previously mentioned, it is essential that all concerned in any project are aware of which standard is being applied.
Weld sizing
In order that the correct size of weld can be applied, it is common to find numbers to either the left or to the right of the symbol.
For fillet welds, numbers to the left of the symbol indicate the design throat thickness, leg length (leg size), or both design throat thickness and leg length requirements. Generally, but not in all cases, fillet welds are of equal legs. Figure 8 gives examples of symbols used in different standards.
For fillet welds:
Superseded BS499 Pt 2 gives
a = design throat thickness
b = leg length
ISO 2553/EN 22553 requirements
a = design throat thickness
z = leg length
s = penetration throat thickness
For butt joints and welds, an S with a number to the left of a symbol refers to the depth of penetration as shown in Fig.9.
When there are no specific dimensional requirements specified for butt welds on a drawing using weld symbols, it would normally be assumed that the requirement is for a full penetration butt weld ( Fig.10).
Numbers to the right of a symbol or symbols relate to the longitudinal dimension of welds, eg for fillets, the number of welds, weld length and weld spacing for non-continuous welds (e.g. intermittent fillet welds), as Fig.11.
On fillet welded joints made from both sides, a staggered weld can be shown by placing a 'Z' through the reference line ( Fig.12).
Supplementary Symbols
Weld symbols indicate the type of preparation to use or the weld type. However, there may still be occasions where other information is required. The basic information can therefore be added to in order to provide further details as shown in Figs.13, 14 and 15. The tail of the weld symbol is the place for supplementary information on the weld.
Weld all Round
For a rectangular hollow section (RHS) welded to a plate, for example:
Weld in the Field or on Site
The box attached to the arrow can be used to contain, or point to, other information.
Welding Process Type
ISO 4063 gives welding processes specific reference numbers. As shown in Fig.16 the appropriate process number is placed in the tail of the arrow. Other processes are given a unique number. In this example, 135 refers to MAG welding.
There are a number of additional symbols given in the standards ( eg ISO 22553) which refer to additional welding or joint requirements. Figure 17 shows the requirement for a sealing run.
Compound Joints/Welds
A compound weld could be a 'T' butt weld which requires fillet welds to be added to increase the throat thickness as shown in Fig.18.
The Broken Reference Line
The main feature that distinguishes weld symbol standards is that for ISO 2553 and BS EN 22553, there is an additional feature of a broken reference line.
This method is used when a weldment or weld preparation needs to be specified on the 'other side' of the arrow as shown in Fig.19.
Any symbol that is used to show a joint or weld type feature on the other side of the arrow line is always placed on a dotted line.
BS 499 and AWS require symbols to be placed above the reference line (which indicate the other side) or below the reference line (indicating the arrow side of the joint).
Summary
Weld symbols are a very useful way of communicating welding requirements from the design office to the shop floor.
It is essential that the 'rules' of the standard used are correctly applied by drawing office personnel. However, it is also important that shop floor personnel are able to read and understand the details of weld symbols.
Much of this requirement can be met by reference to the standard being used within the organisation and by the drawing office personnel considering the needs of the end user such as the welders, welding supervisors, welding inspection personnel and welding engineers in order to minimise costly mistakes due to misinterpretation.
Training of all personnel in the correct use of weld symbol specifications also plays an important role in ensuring that weld symbols are both correctly applied and correctly read.
This article was written by Mark Cozens of Weld-Class Solutions.
The article was reissued by TWI with minor modifications on the 27/04/2020.