Seam welding is the joining of work pieces made of similar or dissimilar materials along a continuous seam. Seam welding can be broken down into two main techniques, resistance seam welding and friction seam welding.
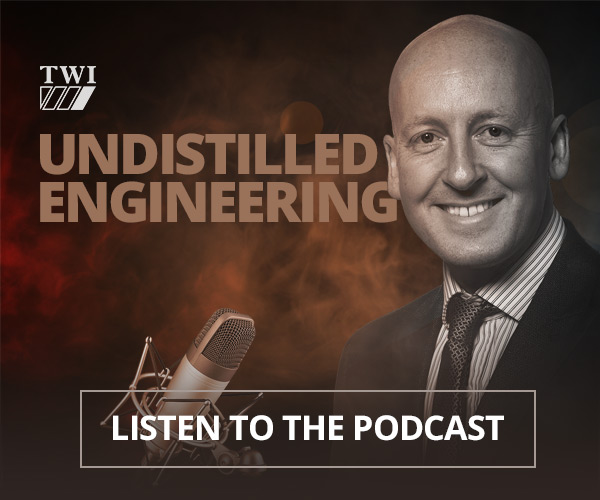
Resistance Seam Welding
Resistance seam welding is a variation of resistance spot welding with the main difference being that the welding electrodes are motor driven wheels rather than stationary rods. Ideal for sheet metal fabrication, this welding method passes an electric current through the sheets of metals to be joined while they are held together by a mechanical force in a lap configuration between shaped copper electrodes. As with other types of resistance welding, fusion is produced where the sheet surfaces come into contact due to this being the point of highest electrical resistance and thereby the place where heat generation is at its greatest.
The heat from the disc-shaped electrode wheels creates a continuous weld as the work pieces are fed between them, resulting in a rolling resistance weld or a non-hermetic seam weld.
Resistance seam welding can either use an intermittent motion, where the speed of the roller is not predetermined, or continuous motion seam welding where the speed of the electrode roller is predetermined before the current is supplied.
Consumable Wire Resistance Seam Welding
An alternative method, called consumable wire resistance seam welding is similar to standard resistance seam welding, except the electrode wheel is grooved so that a shaped copper wire can be introduced between the wheel and the material to be joined. This copper wire is fed from a spool and passes around the electrode wheel at welding speed before being discharged into a scrap container. This ensures that a clean, uncontaminated surface is always presented to the work.
Suitable for welding coated and stainless steel, this process is highly reliable and is able to achieve welding speeds of over 70 metres per minute. While the consumable wire adds to the cost of this type of welding, the expense is offset by the scrap return value of copper.
Resistance Seam Welding Precautions
As with any process that uses an electrical current, you should take precautions over the amount of current supplied by the welding equipment. If the current is too high the interface between the roller and the materials will be too hot. The heat generated by the electrodes can be mitigated by washing the weld area with water which keeps the rollers cool during the joining process.
It is also important to monitor the welding speed to ensure a good quality join along the entire seam.
Advantages of Resistance Seam Welding
Resistance seam welding has the advantage of creating clear welds with no gas formation or welding fume. There is also no need to use filler materials to make the join, which can be made to be both gas and liquid tight, offering a number of applications.
The process can be fully automated, making it a highly repeatable process. In addition, resistance seam welding can create both a single seam weld and a parallel seam weld at the same time.
Disadvantages of Resistance Seam Welding
While resistance seam welding is fine for producing joins in a straight line, the rollers cannot produce more complex curved welds. Welding is also not possible at internal corners or where other component features obstruct access for the wheel electrodes.
This process is also unsuitable for joining sheets of metal of over 3mm in thickness. Due to the speed of the roller, a highly skilled operator may be required to ensure the quality of the weld, while the welding machinery is also expensive.
Resistance Seam Welding Applications
Due to the ability to make gas or liquid-tight joins, this process is well suited for creating items such as steel fuel tanks for vehicles, as well as tin cans, radiators or steel drums. Resistance seam welds can also be found on many types of barrel and exhaust systems.
Widely used for joining aircraft tanks, refrigerators and oil transformers, this process can be used for welding stainless steel, nickel alloys, and magnesium alloys.
Friction Seam Welding
This joining method uses friction to generate heat for the weld joint rather than using electrodes. As with other friction welding processes, the work pieces are joined in the solid phase without melting the materials, meaning that there is no fusion and thereby virtually no interdiffusion between the consumable and the substrate.
Ideal for joining materials that are difficult to weld using conventional arc welding techniques, friction seam welding creates heat via a rotating consumable bar which is axially pressed into a V or U shaped groove. The work pieces are moved under the rotating consumable as a deposit is laid down in the groove.