Hydrogen Embrittlement occurs when metals become brittle as a result of the introduction and diffusion of hydrogen into the material. The degree of embrittlement is influenced both by the amount of hydrogen absorbed and the microstructure of the material. Microstructures which bestow high strength, often monitored by hardness level, or having specific distributions of grain boundary particles or inclusions, can result in increased susceptibility to embrittlement. The phenomenon usually becomes significant when it leads to cracking. This happens when sufficient stress is applied to a hydrogen-embrittled object. Such stress states can be caused both by the presence of residual stresses, associated fabrication operations such as forming and welding, and applied service stresses. The severity of hydrogen embrittlement is a function of temperature: most metals are relatively immune to hydrogen embrittlement, above approximately 150°C.
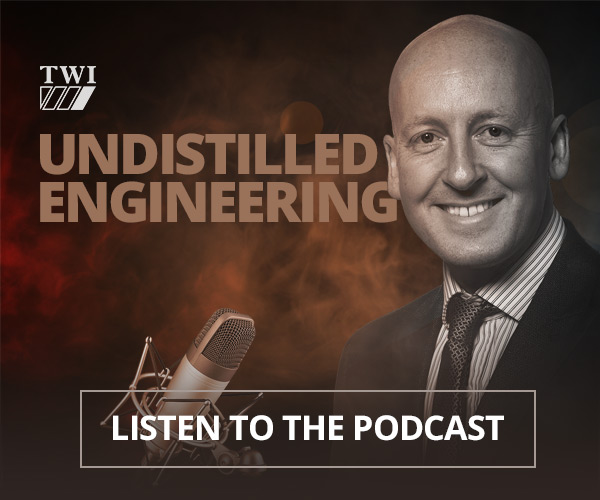
Hydrogen is normally only able to enter metals in the form of atoms or hydrogen ions. Thus, gaseous hydrogen is not absorbed by metals at ambient temperatures, as it is in molecular form, in which pairs of atoms are tightly bound together. However, as the temperature rises, the molecules tend to dissociate into individual atoms allowing absorption at temperatures which, for example, are associated with petroleum refining or heat treatment procedures. Higher rates of absorption are experienced in molten material and this means that casting and welding operations can provide particular opportunities for the entry of hydrogen into metallic materials. Hydrogen ions are also produced by reactions associated with processes such as corrosion, electroplating and cathodic protection. Consequently, there is ample opportunity for the entry of hydrogen into metallic components.
Cracking associated with hydrogen embrittlement has been given a variety of names depending on the situations in which it occurs. Commonly used terms include:
Cold Cracking and Delayed Cracking
These terms are often associated with hydrogen cracks that can form during cooling of the weld metal and workpieces after welding of steels.
Apart from its general meaning, this is a jargon term referring to a specific morphology of cracking occurring in steel pipelines and vessels which absorb hydrogen during service.
This expression was originally applied to service cracking experienced in duplex stainless steels but is now used more widely.
Environmentally-assisted Cracking (EAC)
Refers to cracking that can occur due to interaction between the component and the surrounding service environment. Hydrogen is only one of the agents which can be responsible for this type of cracking.
Disbonding
Apart from its general meaning, its jargon use relates to the spalling of internal, weld-deposited cladding in vessels used for processing with high temperature hydrogenous gases.
Stress Corrosion Cracking (SCC)
Some specific mechanisms of this phenomenon are related to interaction with hydrogen.
Corrosion in environments containing hydrogen sulphide can cause hydrogen absorption and cracking.
The specific crystal structure of metals is important, as it affects the rate at which hydrogen can diffuse and deformation mechanisms. On this basis, ferritic steel has been considered more susceptible to hydrogen embrittlement than alloys with different crystal structures, such as austenitic stainless steels, nickel alloys and aluminium alloys. However, it is apparent that hydrogen can embrittle most engineering alloys, to some extent. Whether this is a practical problem depends on how the application affects microstructure and the availability of hydrogen.
When it does occur, hydrogen embrittlement can cause reduced ductility and a lessening of load-bearing capacity, which can lead to cracking and brittle failures, below the anticipated proof or yield strength of the susceptible materials.