A butt weld is one of the simplest and versatile types of weld joint designs. The joint is formed simply by placing two pieces of metal end-to-end and then welding along the join. Importantly, in a butt joint, the surfaces of the workpieces being joined are on the same plane and weld metal remains within the planes of the surfaces. Thus, workpieces are nearly parallel and do not overlap, unlike lap joints, for example.
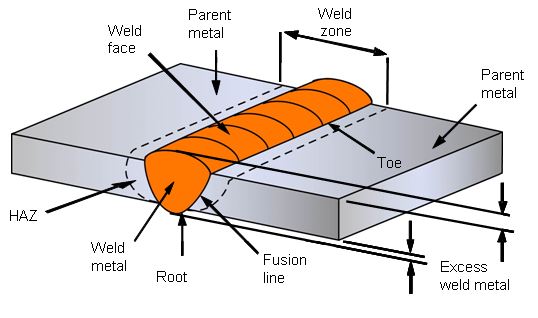
Butt weld diagram
Depending upon the thickness of the metal pieces, different types of grooves can be prepared. Groove preparation is also called weld edge preparation and is necessary for thicker metals. Examples of types of grooves, depending upon their shape are V groove, J groove, and U groove. Groove design changes depending upon full penetration or partial penetration weld requirements. Groove welding can be carried out using different types of welding - whether manual, mechanised or automated processes. Thin sheets are usually welded without any weld edge preparation, such joints are referred as square butt joint.
Butt joints can be welded using arc welding, resistance welding and high energy beam welding and it can even be part of a brazing operation.
At the start, weld pieces can be held together with a tack weld, which is a temporary joint that ensures components stay in a proper alignment while the butt welding is performed. Pre-heating might be required for joining parts at the butt joint area.
Butt welding is commonly employed in various industry sectors varying from piping systems, automotive, energy, power, etc.
Types of Butt Weld Joints
As mentioned earlier, various types of butt welding joints are named for their particular shape. The different types of joints include single V, double V, single and double bevel, single and double U, single and double J joints, square butt joints and even combinations of these. The simplest of these, with regards to alignment, is the square butt weld.
In all cases, the welds are performed with the pieces end-to-end with the thickness of the parent metal. To control distortion of the welded assembly, it is important to control weld penetration by using a double penetration joint design.
For butt welds, depending upon various factors, there is typically a gap of about 2 to 3mm (1/8”) between the workpieces, which is called a root gap. The gap is to ensure that the filler metal fully penetrates the joint. If the gap is too small or too large, it will produce weld defects.
Advantages
Butt welds provide several advantages, including:
- High strength with complete fusion
- Easy to machine
- Distortion control
- Easy to inspect
Disadvantages
There are some disadvantages such as:
- Welding geometry can limit applications
- Fixturing or backing may be required
- Sensitive to faying surface conditions
Butt Weld vs Fillet Weld
The main difference between a butt and a fillet weld is the angle between the joining workpieces. If the surfaces to be joined are on the same plane, then it is a butt weld. If the surfaces are perpendicular (with an angle of 90°), then they are usually joined with a fillet weld. Weld preparation is not required for fillet welds as with a butt joint.
In fillet weld joint, filler metal is deposited at the joint in a triangular section so that it creates an angle of 45° with both the joining workpieces. To achieve the required weld joint thickness, welding is carried out in several passes.
Distortion occurs in both fillet and butt welds as a result of shrinkage as the filler metal cools down. This can be mitigated against by pre-heating and/or by making successive passes on opposite sides of the joint.
Conclusion
Butt welding is the commonly used joint design for a variety of applications in different industry sectors due to its simplicity. This basic technique has a number of different weld formations suitable for varying weld thicknesses.
TWI can offer advice on all aspects of materials and joining. You can find out more about our welding consultancy services here.
Related Frequently Asked Questions (FAQs)