Carbon equivalent formulae were originally developed to give a numerical value for a steel composition which would give an indication of a carbon content which would contribute to an equivalent level of hardenability for that steel. These formulae were later extended to represent the contribution of the composition to the hydrogen cracking susceptibility of steel. They are also used as compositional characterising parameters for other properties that may be linked to hardness, such as toughness and strength.
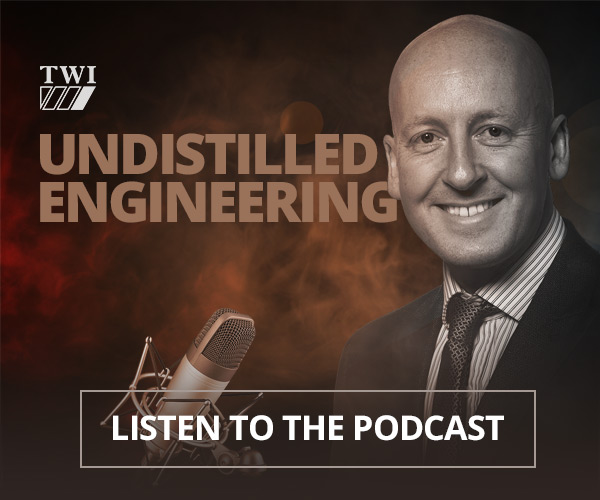
These kind of relationships originate from about 1940 when Dearden and O'Neill proposed a carbon equivalent formula to predict steel strength, hardenability and HAZ hardness [1]. In 1967, the International Institute for Welding (IIW) adopted a somewhat simplified form of Dearden and O'Neill's formula for hardenability which became a generally accepted measure of steel weldability - CEIIW
Since its adoption by IIW, the equation has been incorporated into a number of material standards and codes, including EN 1011-2:2001 [2] (replaces BS 5135-1984 [3] ) and in a modified form in AWS D1.1 [4] , with a "+Si/6" term added to the equation.
Further development of Carbon equivalent formulae has taken place and several can be found in technical literature today. Three of the more common ones are Pcm, CEq and CEN. Ito and Bessyo [5] developed Pcm in Japan based on a wider range of steels than the IIW formula:
The CEq formula devised by Düren [6] has a similar appearance:
Both the Pcm and the CEq formulae were developed for low carbon steels for which the CEIIW is less suitable. Pcm is generally used for modern steels typically used for pipeline manufacture, where carbon contents are no more than ~0.11 wt% [7] .
However, it should be noted that the Pcm formula was derived largely from lower C low alloy steels.
The CEN formula was proposed to evaluate the weldability of a wide variety of steels. For the higher C range, the values of CEN correlate well with carbon equivalents such as CEIIW, whereas for lower carbon steels the values are close to those of the CEq formula. CEN is given by:
Yurioka [8] illustrated a good correlation between Pcm and CEN for structural steels, low-alloy steels (Ni-Cr-Mo type) and carbon steels, provided the carbon content was less than 0.17 wt%. From this comparison the following relationship was derived:
CEN = 2P cm - 0.092 (C ≤ 0.17%)
For carbon steels, the values deviate from this relationship as the Pcm overestimates the cold cracking susceptibility. Where the carbon content exceeds 0.17 wt%, there is a better correlation between CEN and CEIIW :
CEN = CEIIW + 0.012 (C ≥ 0.17%)
Yurioka [8] grouped a number of carbon equivalents for the assessment of weldability, as follows:
Group A are characterised by 1/6 as the coefficient of Manganese; Group B has Carbon as more important than the other alloying elements and is more applicable to modern steels; Group C includes interactions between Carbon and other elements.
Other existing formulae that could be classified as Group B are the CEw developed by Cottrell [9] , and the CET included in the standard EN 1011-2:2001 [3] . Cottrell claimed that the CEw formula could improve the predictions of cracking by a factor of three, compared to CEIIW. The data on which the formula was based was collected from results published in open literature, and covered a wide range of composition and welding conditions. The resulting formula is as follows:
The CET formula is based on similar elements to the CEIIW formula with the exception of Vanadium, although carbon is considered to have more significance than the other elements:
References
N° | Author | Title |
1 |
Dearden J and O'Neill H: |
'A guide to the selection and welding of low alloy structural steel' Transactions of the Institute of Welding, Vol.3, 1940, pp203-214. |
2 |
|
EN 1011-2, 'Welding - Recommendations for welding of metallic materials - Part 2: Arc welding of ferritic steels', British Standards Institution, March 2001 AMD A1 Dec 2003. |
3 |
|
BS5135-1984, 'Process or arc welding of carbon and carbon manganese steels', British Standards Institution, 1984. Superseded by (2) |
4 |
|
AWS D1.1-2010 Annex I, 'Guideline on alternative methods for determining preheat', American Welding Society Inc., 2010 |
5 |
Ito Y and Bessyo K: |
'Weldability formula of high strength steels related to heat affected zone cracking', Published by the International Institute of Welding, 1968, Doc IX-576-68. |
6 |
Düren C F: |
'Prediction of the hardness in the HAZ of HSLA steels by means of the C-equivalent', Select Conference on Hardenability of Steels, Derby, UK, 17 May 1990, Paper 4. |
7 |
Bailey N: |
'Factors Influencing Weldability', In Book 'Weldability of Ferritic Steels', Abington Publishing 1994, ISBN 1 85573 092 8 |
8 |
Yurioka N: |
'Carbon equivalents for hardenability and cold cracking susceptibility of steels', Select Conference on Hardenability of Steels, Derby, UK, 17 May 1990, Paper 3. |
9 |
Cottrell C L M: |
'An improved prediction method for avoiding HAZ hydrogen cracking', Welding and Metal Fabrication, Vol. 58, No. 3, April 1990, pp 178-183. |
See further information about Materials and Corrosion Management, or please contact us.