Die zerstörungsfreie Prüfung (ZfP) ist eine Prüf- und Analysetechnik, die von der Industrie zur Bewertung der Eigenschaften eines Werkstücks, einer Komponente, einer Struktur oder eines Systems auf charakteristische Abweichungen, Schweißfehler und Unvollständigkeiten verwendet wird, ohne das Originalteil zu beschädigen.
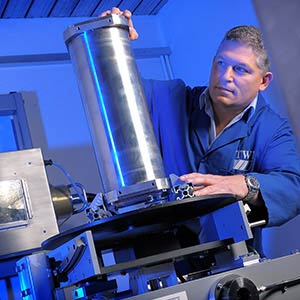
Die Antworten auf häufig gestellte Fragen (FAQs) wurden zusammengestellt, um eine kurze Einführung in jede der Methoden, den Unterschied zwischen zerstörungsfreier und zerstörender Prüfung sowie die Vorteile der Anwendung dieser Prüf- und Analysetechnik zu liefern.
Wenn Sie darüber hinaus gehende Fragen haben oder Hilfe benötigen, senden Sie uns bitte eine englischsprachige E-Mail, um fachkundigen Rat zu erhalten:
kontakt@twi-deutschland.com
Welche zerstörungsfreien Prüfverfahren gibt es?
Zu den aktuellen ZfP-Verfahren gehören:
Akustische Emissionsprüfung
Die akustische Emissionsprüfung (AE) ist ein passives ZfP-Verfahren, das auf der Erkennung kurzer Ultraschallimpulse beruht, die von fortschreitenden Rissen unter einer Belastung ausgehen. Über die Oberfläche der Struktur verteilte Sensoren erkennen die Ultraschallemission. Es ist sogar möglich, die durch die Plastifizierung in hochbeanspruchten Bereichen verursachte akustische Emission zu erkennen, bevor sich ein Riss bildet. Die AE-Prüfung ist eine häufig eingesetzte Methode für einmalige Nachweisprüfungen bei Druckbehältern, lässt sich aber auch zur kontinuierlichen Strukturintegritätsüberwachung einsetzen, z.B. bei Brücken. Auch Lecks und Korrosion lassen sich unter Umständen mit der AE-Prüfung nachweisen.
Weitere Informationen auf Englisch
Elektromagnetische Prüfung
Bei der elektromagnetischen Prüfung werden ein elektrischer Strom bzw. ein Magnetfeld durch ein elektrisch leitendes Teil geleitet. Es gibt drei Arten der elektromagnetischen Prüfung, einschließlich Wirbelstromprüfung, Wechselstromfeldmessung und Fernfeldprüfung:
Bei der Wirbelstromprüfung wird mit einer Wechselstromspule ein elektromagnetisches Feld in das Prüfteil induziert, bei der Wechselstromfeldmessung und der Fernfeldprüfung wird jeweils mit einer Sonde ein Magnetfeld erzeugt, wobei die Fernfeldprüfung im Allgemeinen zur Prüfung von Rohren verwendet wird.
Bodendurchdringendes Radar
Diese geophysikalische ZfP-Methode sendet Radarimpulse durch die Oberfläche eines Materials oder einer unterirdischen Struktur, wie z.B. Fels, Eis, Wasser oder Erde. Die Wellen werden reflektiert oder gebrochen, wenn sie auf ein vergrabenes Objekt oder eine Materialgrenze mit unterschiedlichen elektromagnetischen Eigenschaften treffen.
Laser-Prüfverfahren
Die Laserprüfung kann in drei Unterkategorien aufgegliedert werden: holografische Prüfung, Laserprofilometrie und Laser-Shearografie.
Bei der holographischen Prüfung wird ein Laser verwendet, um Veränderungen in der Oberfläche des Materials zu erkennen, das Belastungen wie Hitze, Druck oder Vibrationen ausgesetzt war. Die Ergebnisse werden dann mit einer unbeschädigten Referenzprobe verglichen, um Defekte aufzuzeigen.
Die Laserprofilometrie verwendet eine mit hoher Geschwindigkeit rotierende Laserlichtquelle und eine Miniaturoptik, um Korrosion, Lochfraß, Erosion und Risse zu erkennen, indem Veränderungen in der Oberfläche über ein aus der Oberflächentopographie erzeugtes 3D-Bild erfasst werden.
Die Laser-Shearografie verwendet Laserlicht, um ein Bild der Oberfläche eines Bauteils aufzunehmen, bevor das Bauteil belastet wird und ein neues Bild aufgenommen wird. Diese Bilder werden miteinander verglichen, um festzustellen, ob irgendwelche Defekte vorhanden sind.
Dichtheitsprüfung
Die Dichtheitsprüfung lässt sich in vier verschiedene Methoden unterteilen - Blasentest, Druckabfallprüfung, Halogendiodentest und Heliumdichtheitsprüfung.
Beim Blasentest wird ein Wasserbad oder bei größeren Teilen eine Seifenlösung verwendet, um Gas (in der Regel Luft) zu erkennen, das in Form von Blasen aus dem Teststück austritt.
Bei der Druckabfallprüfung, die nur bei geschlossenen Systemen verwendet wird, wird entweder Druck oder Vakuum zur Überwachung des Prüfteils verwendet. Ein Druck- oder Vakuumverlust über eine bestimmte Zeitspanne zeigt, dass ein Leck im System vorliegt.
Beim Halogendiodentest wird ebenfalls Druck verwendet, um Lecks zu finden, aber in diesem Fall werden Luft und ein Tracergas auf Halogenbasis zusammengemischt und eine Halogendioden-Detektoreinheit („Schnüffler“) zur Lokalisierung von Lecks verwendet wird.
Bei der Heliumdichtheitsprüfung wird der zu prüfende Behälter mit Helium oder einem Helium-Luft-Gemisch befüllt, um in einem den Behälter umgebenden Gehäuse mit einem Massenspektrometer („Schnüffler“) Veränderungen der Gaszusammensetzung zu erkennen, die auf ein Leck hinweisen würden. Alternativ kann auch ein Vakuum verwendet werden. In diesem Fall entnimmt das Massenspektrometer eine Probe aus der Vakuumkammer, um ionisiertes Helium nachzuweisen, das auf ein Leck hinweist.
Magnetischer Streufluss
Bei dieser Methode wird ein starker Magnet verwendet, um Magnetfelder zu erzeugen, die Stahlstrukturen wie Rohrleitungen und Lagertanks sättigen. Ein Sensor wird verwendet, um Änderungen der magnetischen Flussdichte zu erkennen, die eine Verringerung des Materials durch Lochfraß, Erosion oder Korrosion anzeigen.
Mikrowellenprüfung
Diese Methode ist auf die Verwendung auf dielektrischen, d.h. elektrisch nicht-leitenden Materialien beschränkt und verwendet Mikrowellenfrequenzen, die von einer Prüfsonde gesendet und empfangen werden. Die Prüfsonde erkennt Änderungen der dielektrischen Eigenschaften, wie z.B. Poren, Lunker, Fremdmaterialeinschlüsse oder Risse, und zeigt die Ergebnisse als B- oder C-Scan an.
Eindringprüfung
Bei der Eindringprüfung wird eine Flüssigkeit mit niedriger Viskosität auf das zu prüfende Material aufgetragen. Diese Flüssigkeit sickert in Fehler wie Risse oder Porosität ein, bevor ein Entwickler aufgetragen wird, der die Eindringflüssigkeit nach oben durchsickern lässt und einen sichtbaren Hinweis auf den Fehler erzeugt. Flüssigkeitseindringprüfungen können mit lösungsmittel-entfernbaren Eindringmitteln, wasserauswaschbaren Eindringmitteln oder nachemulgierbaren Eindringmitteln durchgeführt werden. Unterschieden wird zwischen der Farbeindringprüfung und der fluoreszierenden Eindringprüfung.
Magnetpulverprüfung
Die Magnetpulverprüfung verwendet Magnetfelder, um Diskontinuitäten an oder nahe der Oberfläche von ferromagnetischen Materialien zu finden. Das Magnetfeld kann mit einem Permanentmagneten oder einem Elektromagneten erzeugt werden, wobei bei letzterem ein Strom angelegt werden muss.
Das Magnetfeld hebt alle Diskontinuitäten hervor, da die magnetischen Flusslinien Streuungen erzeugen, die durch die Verwendung von magnetischen Partikeln, die in die Diskontinuität gezogen werden, sichtbar werden.
Neutronenradiographie
Bei der Neutronenradiographie dringt ein Strahl niederenergetischer Neutronen in das Werkstück ein. Während der Strahl metallische Materialien durchdringt, wird er von den meisten organischen Materialien absorbiert, so dass diese sichtbar werden und untersucht werden können, um Fehler zu erkennen.
Radiographie
Bei der Radiographie werden Röntgen- oder Gammastrahlen durch ein Prüfstück geleitet, um Fehler zu erkennen. Dabei zeigt die Strahlung aufgrund ihrer Stärke Diskontinuitäten im Material an. Röntgenstrahlen werden üblicherweise für dünne oder weniger dichte Materialien verwendet, während Gammastrahlen für dickere oder dichtere Gegenstände eingesetzt werden. Die Ergebnisse können mittels Filmradiographie, Computerradiographie, Computertomographie oder digitaler Radiographie verarbeitet werden.
Weitere Informationen auf Englisch
Thermografie
Bei der Thermografie werden Sensoren zur Bestimmung der Wellenlänge des von der Oberfläche eines Objekts emittierten Infrarotlichts eingesetzt, um den Zustand eines Prüfstücks zu begutachten.
Bei der passiven Thermografie werden Sensoren zur Messung der Wellenlänge der emittierten Strahlung verwendet. Wenn der Emissionsgrad bekannt ist oder abgeschätzt werden kann, kann die Temperatur berechnet und als digitaler Messwert oder als Falschfarbenbild angezeigt werden. Dies ist nützlich zur Erkennung von überhitzten Lagern, Motoren oder elektrischen Komponenten und wird häufig zur Überwachung des Wärmeverlustes von Gebäuden verwendet.
Die aktive Thermografie erzeugt einen Temperaturgradienten in einer Struktur. Merkmale innerhalb dieser Struktur, die den Wärmefluss beeinflussen, führen zu Oberflächentemperaturschwankungen, die analysiert werden können, um den Zustand eines Bauteils zu bestimmen. Das Verfahren wird oft zur Erkennung von oberflächennahen Delaminationen oder Bindefehlern in Verbundwerkstoffen verwendet.
Weitere Informationen auf Englisch
Ultraschallprüfung
Die Ultraschallprüfung beinhaltet die Übertragung von hochfrequentem Schall in ein Material, um mit Merkmalen innerhalb des Materials zu interagieren, die es reflektieren oder dämpfen. Die Ultraschallprüfung wird allgemein in Reflexionsschall-, Durchschallungs- und Beugungslaufzeittechnik-Verfahren unterteilt.
Weitere Informationen auf Englisch
Reflexionsschallverfahren
Diese Technik leitet einen Schallstrahl in die Oberfläche des Prüfstücks ein. Der Schall wird durch das Material des Prüfstücks geleitet und erreicht entweder die Rückwand des Prüfstücks und kehrt dann zum Wandler zurück oder er kehrt frühzeitig zurück, wenn er von einer Diskontinuität innerhalb des Teils reflektiert wird. Wenn die Schallgeschwindigkeit bekannt ist, kann das aufgezeichnete Zeitintervall zur Ableitung der im Material zurückgelegten Strecke verwendet werden.
Durchschallungsverfahren
Das Durchschallungsverfahren verwendet separate Wandler zum Abstrahlen und Empfangen des Schalls. Die Sendesonde wird auf der einen Seite des Prüflings und die Empfangssonde auf der anderen Seite positioniert. Wenn der Schall das Bauteil durchdringt, wird er durch Merkmale innerhalb des Bauteils, wie z.B. Porosität, gedämpft. Eine Dickenmessung ist mit dieser Technik normalerweise nicht möglich.
Beugungslaufzeittechnik-Verfahren (Time of Flight Diffraction, ToFD)
Das ToFD-Verfahren arbeitet mit der Beugungslaufzeittechnik, d.h. der Änderung der Wellenlänge des Schalls, wenn dieser mit einer Diskontinuität in einem Material interagiert. Dieser Mechanismus wird verwendet, wenn keine echte Reflexion erreicht werden kann, aber eine ausreichende Beugung auftritt, um die Laufzeit des Schalls zu verändern. Damit kann die Spitze eines Defekts erkennt werden, der sich senkrecht zur Kontaktfläche der Sonde befindet. ToFD wird auch für die Rückwandinspektion zum Nachweis von Korrosion verwendet.
Weitere Informationen auf Englisch
Ultraschall-Tauchtechnik
Den Ultraschall nass in das Teil einzukoppeln, kann bei großen oder komplexen geometrischen Prüfstücken eine Herausforderung sein. Zur Vereinfachung werden diese Teile in Wasser, normalerweise in einem Becken, eingetaucht. Diese Methode wird in der Regel mit Anlagen durchgeführt, die das Teil bzw. den Prüfkopf während der Ultraschallprüfung im Tank bewegen.
Luftgekoppelte Ultraschall-Prüfung
Bestimmte Werkstoffe vertragen die Anwendung von nassgekoppeltem Ultraschall nicht. Daher werden unter bestimmten Umständen luftgekoppelte Ultraschallprüfungen durchgeführt. Diese beinhalten die Einkoppelung des Schalls durch einen Luftspalt und erfordern in der Regel den Einsatz von niedrigeren Frequenzen.
Prüfung mit elektromagnetischen Schallwandlern (Electromagnetic Acoustic Transducer Testing, EMAT Testing)
Die EMAT-Prüfung ist eine Art berührungslose Prüfmethode, bei Schallerzeugung und -empfang elektromagnetisch vollzogen werden, d.h. ohne unmittelbaren Kontakt und ohne Nasskopplung mit dem Bauteil. Die EMAT-Prüfung ist besonders für sehr heiße, kalte, saubere oder trockene Umgebungen von Nutzen. Wie bei konventionellem Ultraschall kann die EMAT-Prüfung sowohl normale und abgewinkelte Strahlen als auch andere Modi, wie z.B. geführte Wellen, erzeugen.
Ultaschall-Prüfung mit geführten Wellen
Die Ultraschall-Prüfung mit geführten Wellen ist für die Prüfung von Rohren über große Entfernungen geeignet. Sie wird daher oft Langstreckenultraschalluntersuchung genannt. Die Ultraschall-Prüfung mit geführten Wellen erzeugt und detektiert mithilfe von mehreren Transducern und einem Computer besondere Ultraschallwellenformen, um Änderungen in der Rohrwandung aufzufinden. Die Ultraschall-Prüfung mit geführten Wellen im mittleren Bereich deckt einen Bereich von 25 mm bis 3000 mm ab. Die Ultraschall-Prüfung mit geführten Wellen im Langstrecken-Bereich hat eine größere Reichweite und kann vom Einkoppelungsort aus zur Prüfung im Bereich von bis zu Hunderten von Metern verwendet werden.
Fortschrittliche Ultraschallmethoden
Automatisierte Inspektion
Der Nutzen der Automatisierung wird durch die Integration von ZfP-Sensoren mit handelsüblichen Industrierobotern sowie kollaborativen Robotern, den sogenannten „Cobots“, erreicht. Cobots arbeiten aufgrund von innovativer Hard- und Software eng mit dem menschlichen Bediener zusammen und sind im Produktionsprozess nicht durch Schutzeinrichtungen von diesem getrennt ist. Speziell geschriebene Software für die Erfassung und Visualisierung von Daten schafft eine nahtlose und intuitive Benutzererfahrung, die an spezifische Bedürfnisse angepasst werden kann.
TWI hat mehrere hochleistungsfähige automatisierte Prüfsysteme entwickelt, die sowohl für Forschungs- und Entwicklungsarbeiten als auch für die industrielle Qualitätssicherung geeignet sind.
Phased-Array-Ultraschallprüfung
Phased-Array-Ultraschall-Sonden unterscheiden sich von herkömmlichen Ultraschall-Sonden dadurch, dass sie aus einer Anordnung von Einzelelementen bestehen, die unabhängig voneinander gepulst werden können. Durch die Steuerung der Zeiten, zu denen jedes Element gezündet wird, können die Schallstrahlen fokussiert oder gelenkt werden. Durch das Überstreichen des Strahls durch eine Reihe von Winkeln oder Tiefen können mit einer Sonde Querschnittsansichten erzeugt werden, wo bei herkömmlicher Ultraschallprüfung mehrere Sonden- und Keilkombinationen erforderlich gewesen sein können. Eine virtuelle Sonde kann aus einer Reihe von Elementen bestehen, die elektronisch entlang der Länge des Arrays angesteuert werden, um einen breiten Pinselscan zu erzeugen.
Weitere Informationen auf Englisch
Full Matrix Capture (Vollständige Matrix-Erfassung)
Full Matrix Capture (FMC) ist eine Weiterentwicklung der Phased-Array-Ultraschallprüfung und verwendet die gleichen Sonden. Ihr Hauptvorteil besteht darin, dass es nicht notwendig ist, den Strahl zu fokussieren oder zu lenken, da der gesamte interessierende Bereich im Fokus liegt. Außerdem ist sie relativ tolerant gegenüber fehlausgerichteten Fehlern und strukturellem Rauschen. Dadurch ist er sehr einfach einzurichten und zu verwenden. Der Nachteil ist, dass die Dateigrößen sehr groß sind und die Erfassungsgeschwindigkeit langsamer sein kann als bei der Phased-Array-Ultraschallprüfung.
Weitere Informationen auf Englisch
Virtual Source Aperture
Virtual Source Aperture (VSA) ist eine Variante der Full Matrix Capture, die die meisten Vorteile ihrer überlegenen Bildqualität beibehält, jedoch mit stark reduzierten Dateigrößen und Aufnahmegeschwindigkeiten, die die von der Phased-Array-Ultraschallprüfung übertreffen können. Die Sendeapertur bezeichnet dabei den Bereich des Schallkopfes, der aktiv Ultraschallwellen aussendet. Sie lässt sich bei diesem Verfahren durch eine entsprechende Ansteuerung virtuell ändern.
Schwingungsanalyse
Bei diesem Verfahren werden Sensoren zur Messung der Schwingungssignaturen von rotierenden Maschinen eingesetzt, um den Zustand der Anlage zu beurteilen. Zu den verwendeten Sensortypen gehören Wegsensoren, Geschwindigkeitssensoren und Beschleunigungsmesser.
Visuelle Prüfung
Die visuelle Prüfung, die auch als Sichtkontrolle bekannt ist, ist eine der häufigsten Techniken, bei der der Bediener auf das Prüfteil schaut. Dies kann durch den Einsatz von optischen Instrumenten wie Lupen oder computergestützten Systemen (bekannt als „Remote Viewing“) unterstützt werden.
Diese Methode ermöglicht die Erkennung von Verzug und Versatz, Korrosion, Rissen und vielem mehr. Visuelle Prüfungen begleiten die meisten anderen Arten der zerstörungsfreien Prüfung, da diese im Allgemeinen die Suche nach Fehlern durch einen Bediener erfordern.
Dienstleistungen der zerstörungsfreien Prüfung
TWI bietet eine breite Palette industrieller ZfP-Dienstleistungen an. Finden Sie heraus, in welchen Bereichen wir Sie unterstützen können, indem Sie die hier verlinkten Seiten besuchen oder uns eine englischsprachige E-Mail an folgende Adresse schicken:
kontakt@twi-deutschland.com
Was ist der Unterschied zwischen zerstörender und zerstörungsfreier Prüfung?
Bei der zerstörenden Prüfung wird das Bauteil zerstört oder in irgendeiner Weise verändert, so dass es selbst nach bestandener Prüfung nicht mehr einsatzfähig ist. Beispiele hierfür sind Zugproben, Drei-Punkt-Biegeproben oder Makroschliffe. Bei der zerstörungsfreien Prüfung (ZfP) wird das Teil hingegen nicht zerstört oder verändert, so dass es noch einsatzfähig ist, wenn es die Prüfung besteht.