Seit seiner Erfindung im Jahr 1991 hat TWI das Rührreibschweißen (Friction Stir Welding, FSW) für eine Vielzahl von Anwendungen seiner Mitgliedsunternehmen kontinuierlich weiterentwickelt. Dies beinhaltete die Konstruktion von FSW-Werkzeugen, die Entwicklung von Schweißparametern, Betriebsspezifikationen und Konstruktion von FSW-Maschinen sowie die Herstellung von FSW-Maschinen-Prototypen. Während der gesamten Zeit wurde stets darauf hingewiesen, dass das FSW-Werkzeug eine entscheidende Komponente für die Herstellung qualitativ hochwertiger Schweißnähte ist.
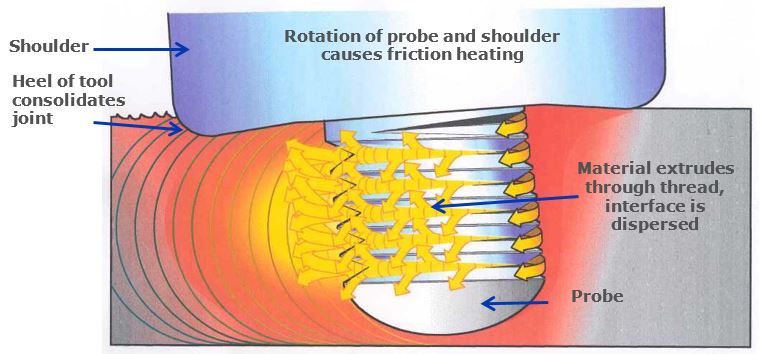
Abbildung 1: Die Rotation des Stifts und der Schulter eines FSW-Werkzeug erzeugt Reibungswärme. Die Schulter wird auf das Werkstück gepresst, die hintere Kante des Werkzeuges staucht das Material zusammen. Der profilierte Stift extrudiert das plastifizierte Material mithilfe des Gewindes und durchbricht und verteilt die Oxidschichten auf den Fügeflächen.
Hintergrund
In den letzten 30 Jahren wurde weltweit eine sehr breite Palette von Stift- und Schulterkonstruktionen für das Rührreibschweißen (Friction Stir Welding, FSW) entwickelt, von denen viele erfolgreich eingesetzt und einige patentiert wurden. Es gab jedoch noch nie eine Standardausführung für die aus Stift und Schulter bestehenden FSW-Werkzeuge, die in Normen und Spezifikationen wie BS EN ISO 25239-1:2020 für das Rührreibschweißen von Aluminium oder die Spezifikation AWS D17.3/D17.3M:2016 für das Rührreibschweißen von Aluminiumlegierungen für Luft- und Raumfahrtanwendungen aufgenommen worden wäre. Obwohl es keine genormte FSW-Werkzeugkonstruktion gibt, gibt es jetzt einige wenige Firmen, die FSW-Werkzeuge „von der Stange“ anbieten. Die Mehrheit der FSW-Anwender behandelt ihre FSW-Werkzeugkonstruktion jedoch als streng vertraulich, und daher gibt es nur sehr wenige Veröffentlichungen, die detaillierte FSW-Werkzeug-Geometrien und -abmessungen oder die genaue Materialzusammensetzung, aus der sie hergestellt werden, beschreiben.
Grundprinzipien
Um ein FSW-Werkzeug zu konstruieren, ist es zunächst erforderlich, seine verschiedenen Aufgaben zu verstehen:
Um eine Pressschweißnaht zwischen Metallstücken zu erzeugen, wird das FSW-Werkzeug, das aus einer Kombination von Stift und die Schulter besteht, gedreht und mit einer hohen Anpresskraft in die Fügezone zwischen zwei Werkstücke aus Platten oder Blechen eingetaucht, z.B. so wie in Abbildung 1 dargestellt. Es ist sehr wichtig, dass die Werkstücke in einer Spannvorrichtung auf der Unterseite durch eine normalerweise aus Stahl hergestellten festen Unterlage aufliegen. Die feste Unterlage hat den Zweck, die Axialkraft aufzunehmen (actio = reactio). Außerdem ist eine seitliche Klemmung erforderlich, um zu verhindern, dass sich die Werkstücke auseinandergepresst werden, wenn das FSW-Werkzeug entlang der Schweißschnittstelle verfahren wird. Die Rotation des Werkzeugs erzeugt Reibwärme und erweicht lokal den Bereich der Fügezone. Wenn das Werkstück in der Nähe des sich drehenden Werkzeugs ausreichend erweicht ist, wird das Werkzeug entlang der Schweißnahtgrenzfläche verfahren.
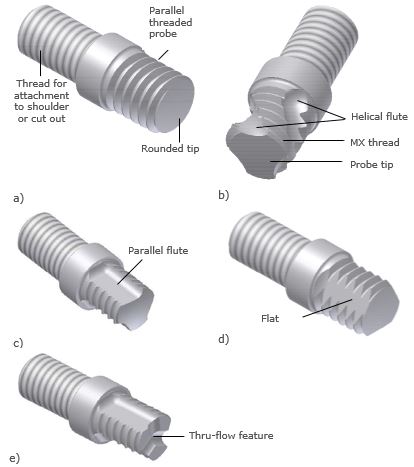
Abbildung 2: FSW-Stift-Geometrien: a) Gewindestift mit Gewinde auf einem zylindrischen Stift, einer gerundeten Spitze und einem weiteren Gewinde zur Befestigung des Stifts in der Schulter; b) MX-Triflute™ (Multihelix-Werkzeug mit Gewinde und drei Wendeln); c) Parallele Nuten; d) MX-Triflat™ (an drei Seiten abgeflachtes Werkzeug); e) Durchflussspitze, an einem Werkzeug mit paralleler Nuten.
Entwicklung der Werkzeugkonstruktion
Als die Entwicklung des Rührreibschweißens voranschritt, verlangten kommerzielle Anwender des Verfahrens höhere Schweißgeschwindigkeiten in hochfesten Aluminiumlegierungen, was dazu führte, dass das MX-Triflute™ genannte Multihelix- Werkzeug entwickelt wurde. Eine Version des MX-Triflute™-Stifts ist in Abbildung 2b dargestellt, der, obwohl nicht offensichtlich, einen leicht konisch zulaufenden Körper hat. Der konisch zulaufende Stiftkörper und die drei gewendelten Nuten, die in Abbildung 2b dargestellt sind, verdrängte während des Schweißzyklus sehr viel weniger Material als der ursprüngliche Stift mit zylindrischem Körper, so dass bei gleichbleibend hoher Qualität wesentlich höhere Schweißgeschwindigkeiten erreicht werden konnten. Die drei gewendelten Nuten und die Multihelix-Gewindeform bewirkten auch eine aktiveres Durchbrechen der Oxidhäute und Vermischen der Werkstückmaterialien sowie eine höhere Erzeugung von Reibungserwärmung, was die FSW-Prozesseffizienz verbesserte. Die MX-Triflute™- Werkzeugstifte sind vor allem zum Schweißen dünnerer Werkstücke bis 15mm Dicke und die an drei Seiten abgeflachten MX-Triflat™-Stifte vor allem für dickere Werkstücke geeignet.
FSW-Werkzeugschultern sind im Allgemeinen weniger komplex in ihrer Konstruktion als die Stifte. Die Werkzeugschulter wird nicht unbedingt parallel zur Werkstückoberfläche ausgerichtet: Bei einfachen linearen Schweißnähten wird das Werkzeug oft so geneigt, dass die hintere Kante der Schulter in das Werkstück eindringt und zusätzlichen Stauch- oder Schmiededruck ausübt. Dawes et al (1995) entwickelten ein konkaves Schulterdesign, das bei einer Werkzeugneigung um den Betriebswinkel von 2-3˚ (Abbildung 3a) zuverlässig funktioniert. Der Wunsch, die Schweißgeschwindigkeiten in Aluminiumlegierungen der 5000er-Serie zu erhöhen, führte zur Entwicklung einer Spiral-Schulter (englisch Scroll-Shoulder, Abbildung 3a-b), bei der in die Stirnfläche der Schulter ein Spirale eingearbeitet ist, die das Material von der Außenkante der Schulter bis zum Übergang zum Stift fördert (Dawes und Thomas, 1999). Diese Idee wurde eigentlich entwickelt, um den vertikalen, nach unten gerichteten Materialfluss zu verbessern, aber erste Versuche zeigten, dass eine solche Konstruktionsänderung auch die Verwendung eines senkrecht zur Oberfläche ausgerichteten, also nicht geneigten Werkzeugs ermöglichte (englisch Zero Tilt Tool). Dieses Schulterdesign wird heute in den meisten Fällen für nichtlineare Anwendungen verwendet, die zwei- und drei-dimensionale Schweißbahnen erfordern.
Das Schulterprofil des FSW-Werkzeugs beeinflusst die Reibwärmeerzeugung während des Rührreibschweißens erheblich. Werkzeugschulterprofile, die das seitliche Herauspressen von plastifiziertem Material einschränken oder verhindern, wie z.B. die Spirale, liefern aufgrund der größeren Oberfläche einen größeren Wärmeeintrag. Daher können durch die Verwendung einer Spirale die Schulterdurchmesser verringert werden. Dies hat sich als besonders vorteilhaft erwiesen, weil es komplexere Stoßgestaltungen und Schweißpfade ermöglicht, wobei die Werkzeugkonstruktion in vielen Fällen auf die vorgegebenen Verbindungs-Geometrien angepasst werden muss.
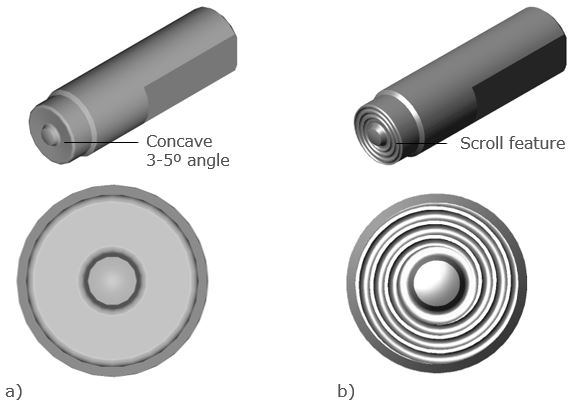
Abbildung 3: Werkzeug-Schulterkonstruktionen, hier vereinfacht dargestellt mit einem nicht-profilierten Stift: a) Konkave Schulter mit 3–5° Winkel; b) Spiralschulter
Werkstoffe der Rührreibschweißwerkzeuge für Aluminium-Werkstücke
Werkstoffe wie intermetallische Legierungen, Silizide, Laves-Phase-Legierungen (zweiphasige Nb-Ti-Cr-Legierungen), Platinlegierungen, Iridiumlegierungen und Keramiken haben im Hinblick auf die Hochtemperaturfestigkeit alle das Potenzial, als FSW-Werkzeugstifte zum Schweißen von Aluminiumlegierungen verwendet zu werden. Frühere Forschungen am TWI haben jedoch gezeigt, dass die meisten dieser Werkstoffe eine sehr schlechte Bruchzähigkeit haben und schnell durch Sprödbruch versagen, wenn sie als Rührreibschweißwerkzeuge verwendet werden. Darüber hinaus ist diese Gruppe von Werkstoffen schwer zu beschaffen und schwierig auf die FSW-Stift-Geometrien zu bearbeiten, die derzeit als notwendig erachtet werden, um Schweißnähte guter Qualität zu erzeugen.
Die Entwicklung am TWI hat in den letzten 25 Jahren zu einer kleinen Gruppe von Werkstoffen geführt, die relativ einfach beschafft und bearbeitet werden können. Frühere Forschungen zum Rührreibschweißen von Aluminium-Legierungen umfassten die folgenden Stiftwerkstoffe:
- Warmarbeitsstähle (Der Werkstoff 1.2344, AISI H13 HWTS wird oft verwendet)
- Schnellarbeitsstähle
- Superlegierungen (Ni- und Co-Basis-Legierungen)
- Sinterkarbide (WC-Co werden gelegentlich verwendet)
Eine vergleichende Auflistung dieser Materialien ist in Tabelle 1 dargestellt.
Werkzeug-Material | Eignung | Relative Bearbeitbarkeit | Relative Kosten | Relative Verfügbarkeit |
Wolframcarbid (WC) |
Gute Festigkeit, schlechte Zähigkeit bei niedriger Temperatur |
Schlecht |
Niedrig |
Befriedigend |
Densimet D176
|
Angemessene Festigkeit und Zähigkeit |
Gut |
Mittel |
Gut |
TZM |
Angemessene Festigkeit und Zähigkeit, erzeugt aber bei erhöhten Temperaturen einen gefährlichen Oxidrauch |
Gut |
Mittel |
Gut |
Nimonische Legierungen |
Gute Festigkeit, aber relativ geringe Zähigkeit |
Befriedigend |
Gut |
Schlecht |
MP159 |
Gute Festigkeit und Zähigkeit |
Befriedigend |
Hoch |
Befriedigend |
Tabelle 1 Relative Eigenschaften verschiedener FSW-Werkzeugwerkstoffe zum Schweißen hochfester Aluminium-Legierungen
Für Al-Legierungen hat sich die hochfeste Kobaltbasislegierung MP159 als die beste verfügbare Wahl erwiesen. MP159 wurde am TWI erstmals im Jahr 2001 als FSW-Stiftmaterial verwendet. Diese Legierung wurde von SPS Technologies Inc. als Legierung für Befestigungselemente entwickelt, die bis zu 590°C betrieben werden kann. Inzwischen wird die Legierung von der Latrobe Speciality Steel Company in den USA hergestellt. Die nominelle chemische Zusammensetzung der Legierung MP159 ist in Tabelle 2 aufgeführt.
Element | Co | Ni | Cr | Fe | Mo | Ti | Ni | Al |
Gew.-% |
35.7 |
25.5 |
19 |
9 |
7 |
3 |
0.6 |
0.2 |
Tabelle 2 Nominelle chemische Zusammensetzung der Kobaltbasislegierung MP159
Die attraktiven Eigenschaften, die zur Verwendung von MP159 für FSW-Stifte geführt haben, sind:
- Hohe Festigkeit (1445 N/mm² bei 540°C) kombiniert mit guter Duktilität und Zähigkeit
- Hohe Betriebstemperatur (bis zu 590°C)
- Hohe Kriechfestigkeit bis zu 590°C
- Kann zu komplexen Formen geschmiedet werden
- Gute Ermüdungsbeständigkeit
- Kann zu einem kommerziell vertretbaren Preis erworben werden
- Kann zu komplexen Formen bearbeitet werden
Schweißnahtqualität und Qualitätsbewertung
Obwohl es oft gefordert wird, ist es oft schwierig, die am besten geeignete FSW-Stiftform und -abmessungen für eine bestimmte Anwendung zu ermitteln, da die Größe des zu schweißenden Bauteils und der Kühlkörpereffekt der erforderlichen Spannvorrichtungen berücksichtigt werden müssen. Dabei wird daher zunächst ein bestimmter FSW-Werkzeugstifttyp auf der Grundlage früherer Erfahrungen sowie der Konstruktion, Geometrie und Abmessungen als Startpunkt ausgewählt. Meistens wird eine kurze Matrixstudie mit unterschiedlichen Schweißnahtparametern und deren Bewertung durchgeführt, um festzustellen, ob der ausgewählte Stift eine gute Schweißnahtqualität erzeugen kann oder wo die Grenze der Schweißnahtparametertoleranzfensters liegt. In vielen Fällen erzeugt die ursprünglich gewählte FSW-Stiftkonstruktion eine gute Schweißnahtqualität, aber gelegentlich ist eine Neukonstruktion des Werkzeugs erforderlich, um festgestellte Nachteile oder Unstimmigkeiten im zu schweißenden Material auszugleichen – z.B. Schwankungen der Dicke, Kantenqualität oder Geradheit von Strangpressprofilen, Blechen oder anderen Werkstücken.
Da es noch keine wirklich zuverlässigen FEM-Modelle gibt, mit denen die genaue Form der FSW-Stifte für eine bestimmte Anwendung, einen bestimmten Legierungstyp und eine bestimmte Platten-/Blechdicke genau bestimmt werden kann, kommt TWI zu der Schlussfolgerung, dass ein empirischer und iterativer Ansatz nach wie vor tendenziell der beste Weg zur Entwicklung der FSW-Technologie für unsere TWI-Mitgliedsunternehmen ist (siehe Abbildung 4). Unser Ansatz hat sich bisher als erfolgreich erwiesen und Vertrauen bei den industriellen Endverbrauchern geschaffen. Ein Aspekt, der bei der Untersuchung aufwendiger „optimierter“ Werkzeugkonstruktionen mit Computermodellen oft übersehen wird, ist die endgültige „Herstellbarkeit“ des Werkzeugs.
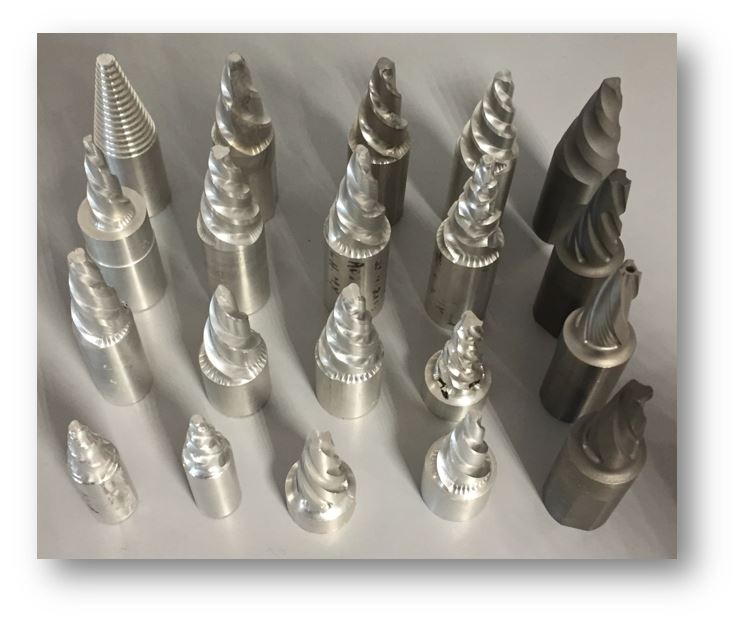
Abbildung 4 Beispiel für verschiedene Design-Iterationen, die während eines großen FSW-Werkzeugentwicklungsprogramms für das Schweißen von Kupfer-Legierungen mit dickem Querschnitt untersucht wurden. Die Zerspanbarkeit ist ein wichtiger Faktor, der bei der Konstruktion neuer FSW-Werkzeuge zu berücksichtigen ist.
FSW-Werkzeuge in TWI-Forschungsprojekten
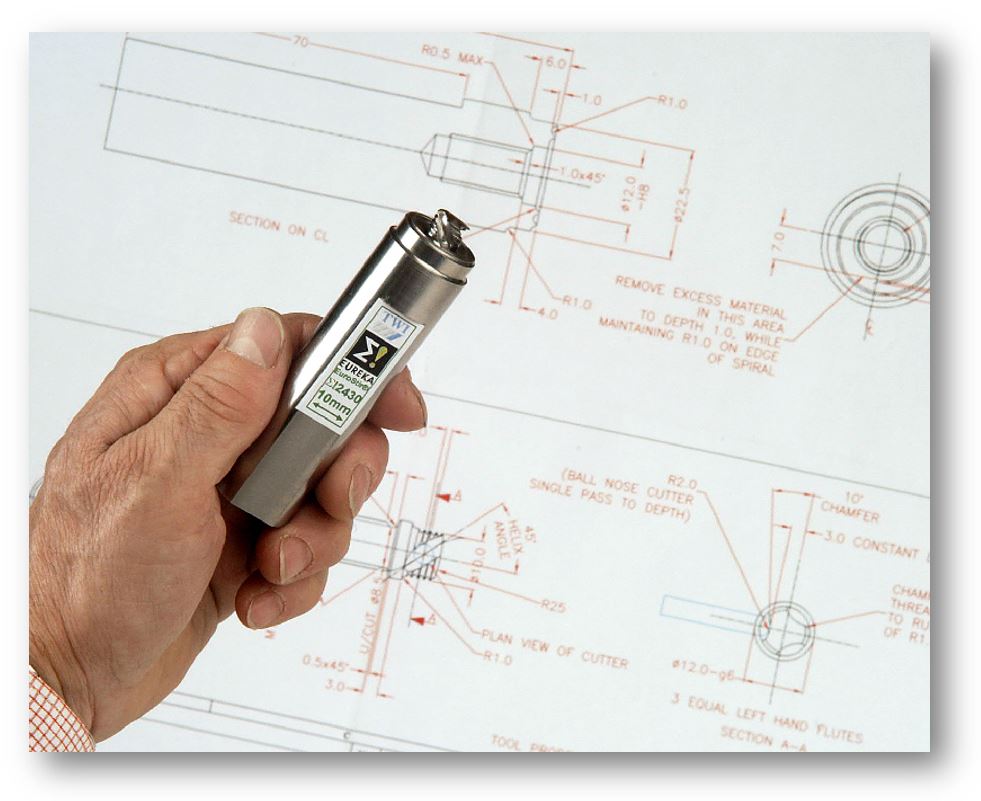
Abbildung 5: Ein im EuroStir®-Projekt (Eureka S! 2430) entwickeltes FSW-Werkzeug
Ein FSW-Einzelkundenprojekt bei TWI umfasst in den meisten Fällen die Lieferung eines FSW-Werkzeugdesigns (das dann in das Eigentum des Kunden übergeht), zusammen mit Zeichnungen zur Werkzeugherstellung und den effektivsten und robustesten Produktionsschweißparametern, die aus einem vereinbarten Schweißparameter-Entwicklungsprogramm anhand von Leistungskennzahlen (Key-Performance-Indicators, KPIs) des Kunden abgeleitet werden.
Die Qualität wird im Hinblick auf metallurgische und mechanische Verbindungseigenschaften bewertet, wobei die Abnahmekriterien meist der Norm ISO 25239 entsprechen oder durch die Kundenspezifikation vorgegeben sind. Wenn ein Kriterium nicht verfügbar ist, kann TWI über geeignete Bewertungsprüfpläne beraten, um das Mitgliedsunternehmen bei der Festlegung der tolerierbaren Qualitäts- und Leistungsakzeptanzgrenzen zu unterstützen. Dies kann ein FSW-Programm abkürzen, das ein Unternehmen mit einer FSW-Anwendung aber wenig interner FSW-Prozess-Erfahrung zeitaufwendig durchführen müsste, um erfolgreiche Ergebnisse zu entwickeln.
FSW-Unterstützungsangebot beim TWI
Seit der Erfindung des FSW im Jahr 1991 hat das TWI hart daran gearbeitet, unsere weltweit führende industrielle Unterstützung und Innovation für diese Technologie aufrechtzuerhalten. Nachstehend finden Sie eine nicht auf Vollständigkeit abzielende Auswahl unseres FSW-Angebots an technischer Unterstützung und eine Reihe von FSW-Prozessvarianten:

Abbildung 6 TWIs Dienstleistungsangebote zum Rührreibschweißen: Numerische Modellierung, Fertigungstechnische Dienstleistungen, Materialkunde, Prüfung und Entwicklung von FSW-Prozessvarianten
Typischer FSW-Projektzyklus am TWI
Im Laufe der Jahre hat das TWI einen risikogesteuerten, abgestuften Ansatz für die FSW-Prozessentwicklung und den Technologietransfer entwickelt. Das nachstehende Diagramm gibt einen Überblick über einen typischen FSW-Projektzyklus, der als risikobegrenzender, vertrauensbildender Fahrplan bei der Erkundung und Übernahme der Technologie vorgeschlagen wird.
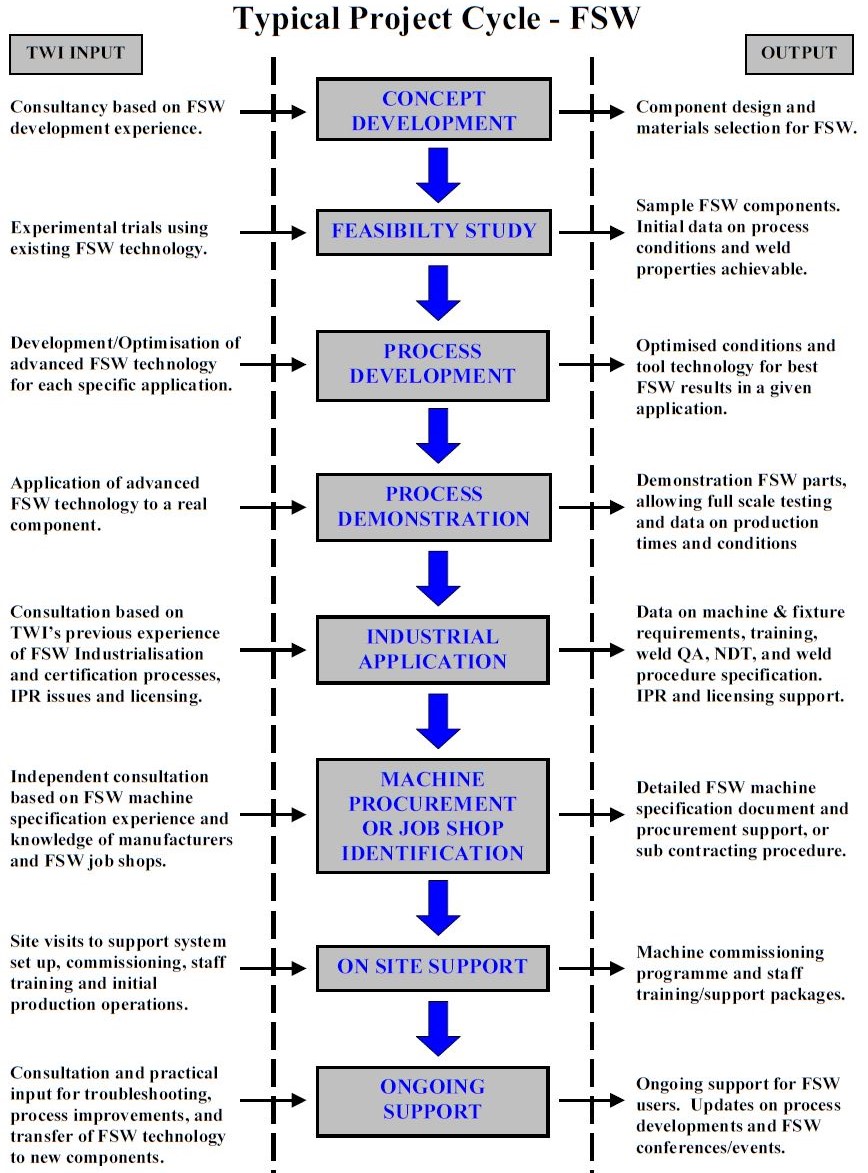
Abbildung 7 TWIs Input und Output im typischen FSW-Projektzyklus: Konzeptentwicklung, Machbarkeitsstudie, Prozessentwicklung, Prozessabnahme, industrielle Anwendung, Maschinenbeschaffung oder Lieferantenbewertung, Unterstützung vor Ort und weiterführende Unterstützung
Dieser Artikel gehört zu einer Reihe von häufig gestellten Fragen (FAQs). Für weitere Informationen zum Rührreibschweißen oder anderen Themen, senden Sie bitte eine englischsprachige E-Mail an:
kontakt@twi-deutschland.com