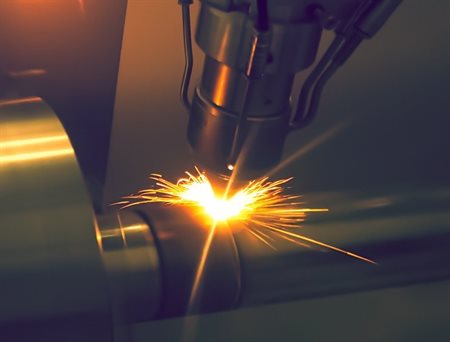
Viele gängige Oberflächenbeschichtungsverfahren sind aus verschiedenen Gründen begrenzt: Das Laserauftragsschweißen ist im Vergleich zu anderen Verfahren vergleichsweise langsam und führt dem darunter liegenden Substrat relativ viel Wärme zu; thermische Spritzverfahren sind im Allgemeinen energie- und materialaufwendig und weisen keine metallurgische Haftfestigkeit auf; und Galvanisierungsverfahren sind umweltschädlich, was zur Einführung von Vorschriften führt, die ihre Anwendung einschränken, und leiden unter Haftungsmängeln und Fehlern.
Durch die Entwicklung von EHLA wurde versucht, jedes dieser Probleme zu lösen, um die industriellen Anwendungsmöglichkeiten des Laserauftragschweißens zu erweitern.
Wie unterscheidet sich EHLA vom konventionellen Laserstrahl-Auftragschweißen?
Beim konventionellen Laserstrahl-Auftragschweißen erzeugt ein optisch fokussierter Laserstrahl auf der Oberfläche des Bauteils ein Schmelzbad, in das Pulver oder Draht über eine Düse eingebracht werden und durch eine Kombination aus Schmelzbadtemperatur und Laserstrahlung aufschmelzen, um Form und Funktion hinzuzufügen. Während die Düse das Substrat durchquert, entfernt sich die Wärmequelle, und das abgeschiedene Material verfestigt sich auf dem Substrat mit einer Zone aus vermischtem Material (300µm-1000µm tief) zwischen dem Substrat und der Beschichtung.
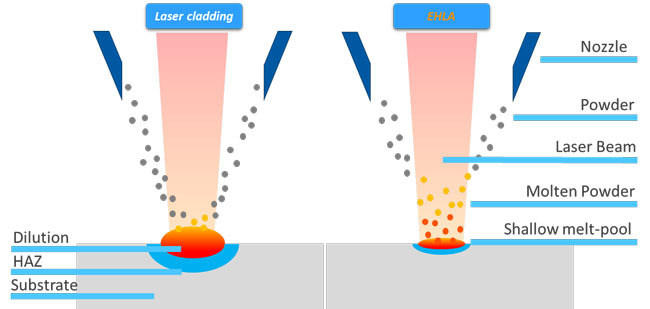
Beim EHLA-Verfahren wird das Pulver in der Linie des fokussierten Laserstrahls über dem Substrat zugeführt. Dadurch wird sichergestellt, dass das abgeschiedene Material bereits geschmolzen ist, bevor es mit dem Substrat in Berührung kommt. Auf dem Substrat bildet sich dennoch ein sehr flaches Schmelzbad, das es dem abgeschiedenen Material ermöglicht, abzukühlen und in Kontakt mit dem darunter liegenden Material zu erstarren, wodurch die Wärmemenge, die das darunter liegende Bauteil erreicht, und die Tiefe der Vermischung und der Wärmeeffekte verringert werden. Diese geringe Vermischung ermöglicht die Herstellung viel dünnerer Schichten (20-300 µm), die die gewünschte chemische Zusammensetzung innerhalb von 5-10 µm erreichen. Dies ist auch die Grundlage für die hohen Verfahrgeschwindigkeiten, die mit EHLA erreicht werden können.
Was sind die Anwendungen von EHLA?
EHLA zielt in erster Linie auf die Beschichtung von Bauteilen ab: Das macht sie zu einer vielversprechenden Technologie für alle Bereiche, in denen Bauteile einem hohen Verschleiß unterliegen oder korrosionsgefährdet sind, oder eine Kombination aus beidem. Beispiele für diese Art von Anwendungen können sein:
- Bremsscheiben
- Hydraulikzylinder und Kolbenstangen
- Lagerzapfen
- Ventile und Schäfte
Welche Vorteile hat EHLA?
Für die Qualität der Beschichtung
Durch das Einbringen der Pulverpartikel in den Weg des Lasers wird weniger Energie direkt in das darunter liegende Bauteil oder Substrat eingebracht. Dadurch werden die thermischen Auswirkungen des Lasers auf das Bauteilgefüge stark reduziert und das Verzugs-Risiko minimiert.
Was die Integrität der Beschichtung betrifft, so weisen EHLA-Beschichtungen eine Materialdichte von über 99,8 % auf und weisen eine äußerst geringe Fehler- und Porositätsrate auf. Wie beim Laserstrahl-Auftragschweißen hängt die Materialintegrität stark von der Pulverqualität und der Wahl der Prozessparameter ab. Zwischen der Beschichtung und dem Substrat bildet sich eine starke metallurgische Verbindung, die eine hohe Schlagfestigkeit gewährleistet.
Dank der geringen Vermischung können EHLA-Beschichtungen bis zu 20 µm dünn aufgetragen werden, bis zu 300 µm pro Schicht, wobei jede nachfolgende Schicht metallurgisch mit der darunter liegenden Schicht verbunden ist, die erreichbare Gesamtdicke ist unbegrenzt. Die geringe Vermischung ermöglicht es EHLA auch, ungleiche Materialien zu verbinden, die mit konventionellen Techniken nur schwer zu verbinden oder zu beschichten sind.
Für die Umwelt
EHLA ist ein vielversprechender Kandidat für den Ersatz von Chrombeschichtungen, da es einen erheblichen Korrosionsschutz ohne die von sechswertigem Chrom ausgehenden Umwelt- und Gesundheitsrisiken bietet.
EHLA weist außerdem eine Materialerfassungsrate von bis zu 95 % auf, was den Abfall reduziert und die Effizienz der aufgebrachten Beschichtung verbessert.
Für die Zukunft
So wie TWI in den letzten 15 Jahren das Laserstrahl-Auftragschweißen (DED-LB) von der Beschichtung zur additiven Fertigung geführt hat, so planen wir, die Entwicklung von EHLA so schnell wie möglich auf ähnliche Weise durchzuführen. Aufgrund der Ähnlichkeit der Technologien eignet sich EHLA für eine rasche Entwicklung der additiven Ultrahochgeschwindigkeitsfertigung. Die Freiheit der Pulver-AM-Technologien wird erhalten bleiben, wobei EHLA wahrscheinlich in der Lage sein wird, sowohl die Freiform-Neuwaren-Produktion, das Hinzufügen von Merkmalen zu bestehenden Komponenten als auch die Freiform-Reparatur von Komponenten durchzuführen.