Frequently Asked Questions
The first important point is that not all MMA electrodes can be used with all polarities. Electrode manufacturer information and specifications such as BS EN ISO 2560:2009 and AWS A5.1-2012, define the polarity with which different coated electrodes may be used. The choice of polarity also depends on the type of the material, welding position and joint design. A welding procedure should specify the polarity for each weld run.
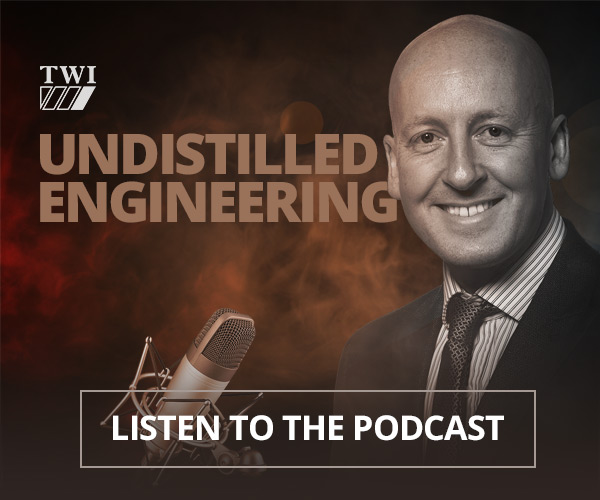
It is necessary to define terms to specify the polarity of the welding process. The part of the welding circuit that is positive (attracts electrons in the arc) is the anode. The part of the welding circuit that is negative (produces electrons in the arc) is the cathode. A useful mnemonic for this is PANiC (Positive Anode, Negative Cathode).
When the welding process is performed in DC mode, the electrode (either MMA electrode, MIG/MAG/flux- or metal-cored wire or tungsten electrode), can be either positive or negative. This results in either Direct Current Electrode Positive (DCEP) or Direct Current Electrode Negative (DCEN). DCEP was also historically known as Direct Current Reverse Polarity (DCRP) or simply "Reverse", whereas DCEN was also known as Direct Current Straight Polarity (DCSP) or simply "Straight".
In TIG welding, the split of heat between the anode and cathode is significant. Approximately 2/3rds of the heat is generated at the positive anode, due to the impingement of high speed, high energy electrons. The negative cathode does not experience this effect, and can even undergo cooling by thermionic emission dependent on the material. For example, the tungsten electrode is thermionic, so will experience this cooling effect. For this reason, DCEN polarity is the most common choice for TIG welding when the cleaning action of the DCEP process is not needed. The use of DCEP for TIG welding necessitates larger diameter tungsten electrodes and water-cooling, and is most commonly used as only part of the cycle in AC welding.
The MMA process however, with its consumable electrode, does not have these concerns. The heat distribution between the electrode and the workpiece is also different, and is not as strongly controlled by the polarity. In particular, the movement of material directly from the consumable electrode to the workpiece results in significant balancing of the heat between the two points.
What is more important than the heat distribution is the effect of polarity on penetration in MMA welding. In general, operating on DCEP results in greater penetration, and DCEN results in reduced penetration and a reduction in dilution of the weld metal with the substrate. This is important for electrodes that are capable of being used on both DC polarities (and AC). The DCEN mode is often used on open root runs to reduce the risk of burn-through, whereas DCEP is used to reduce the risk of lack of fusion defects. DCEN can also be used for surfacing applications in order to minimise penetration, and thin sheet welding. AC is also used as a method of reducing the potential for arc blow. The overruling factor however is still the electrode flux coating, which is inherent to the welding electrode, and results in polarity restrictions specified by the manufacturer.
For completeness, information is given here about the MIG/MAG and submerged arc process and the influence of polarity.
For MIG/MAG welding, DCEN and AC are not commonly used because it is difficult to achieve a stable spray condition, mostly operating in globular transfer, which does not necessarily result in an acceptable weld. Equipment manufacturers are increasingly looking to develop power sources that can use these conditions however. The DCEP condition also aids melting of the wire due to the impingement of electrons. This heat is again transferred to the weld pool through the passage of molten droplets, helping balance the anode and cathode.
Submerged arc welding is similar to MIG/MAG, with DCEP being the most commonly used polarity, but DCEN is seen more often in this process, particularly for surfacing applications, where reduced penetration and dilution with the substrate is preferred. AC is used when performing multiple wire welding, typically with a DC leading wire and AC for all trailing wires to reduce arc blow problems.
References
AWS Welding Handbook - American Welding Society
Jefferson's Welding Encyclopedia, 18th Edition - American Welding Society
Principles of Welding - Robert W. Messler, Jr
Procedure Handbook of Arc Welding - Lincoln Electric
Welding Metallurgy, 2nd Edition - Sindo Kou
ANSI/AWS A5.1-2012 Specification for carbon steel electrodes for shielded metal arc welding
BS EN ISO 2560:2009 Welding consumables. Covered electrodes for manual metal arc welding of non alloy and fine grain steels. Classification
For more information, please contact us.